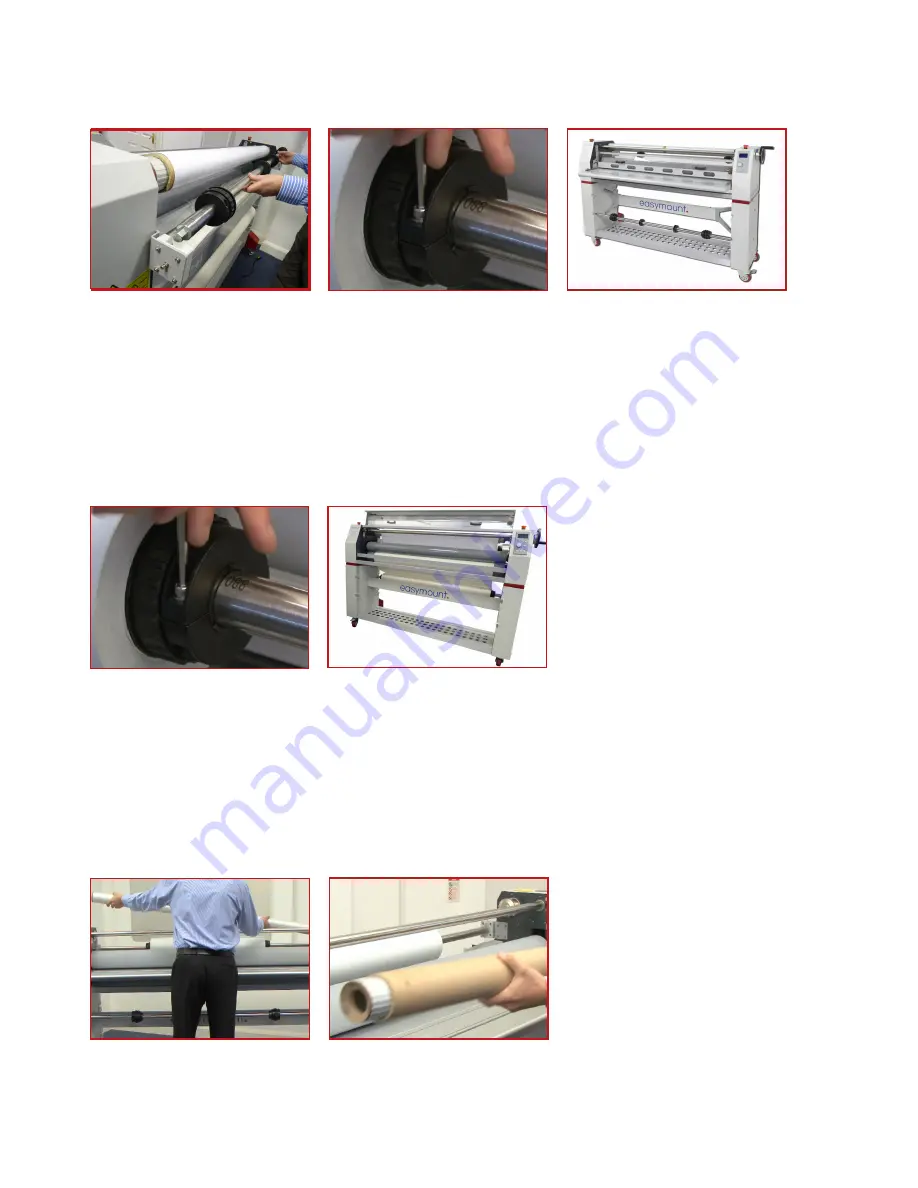
6
Installation of Laminating Films
Pressure sensitive film (loaded on the top mandrel)
1. Remove the top mandrel from the
mandrel support brackets
5. Re-load the mandrel on to the
bracket with the film feeding from
the bottom of the mandrel if the
film is wound with the film on the
outside of off the top of the roll if the
film is wound on the inside.
Liner paper/Mount film (loaded on the bottom mandrel)
1. Remove the mandrel from the
mandrel support brackets
2. Loosen the two fastening screws
on the mandrel core grips, slide off
one side
3. Slide on the liner paper/mount film
and position centrally to match the
top
4. Re-load the mandrel into the
brackets
1. The take up mandrel is held in
place with a spring loaded bracket: to
remove push towards the spring and
lift upwards
2. Loosen the two fastening screws
on one of the mandrel core grips,
slide off one side.
3. Slide on the film positioning it
centrally on the mandrel and re-fix
the core grips.
4. Release the tension on the film
by turning the ‘friction adjustment
sleeve’
Take up mandrel
2. Slide an empty cardboard core
onto the take up mandrel and replace