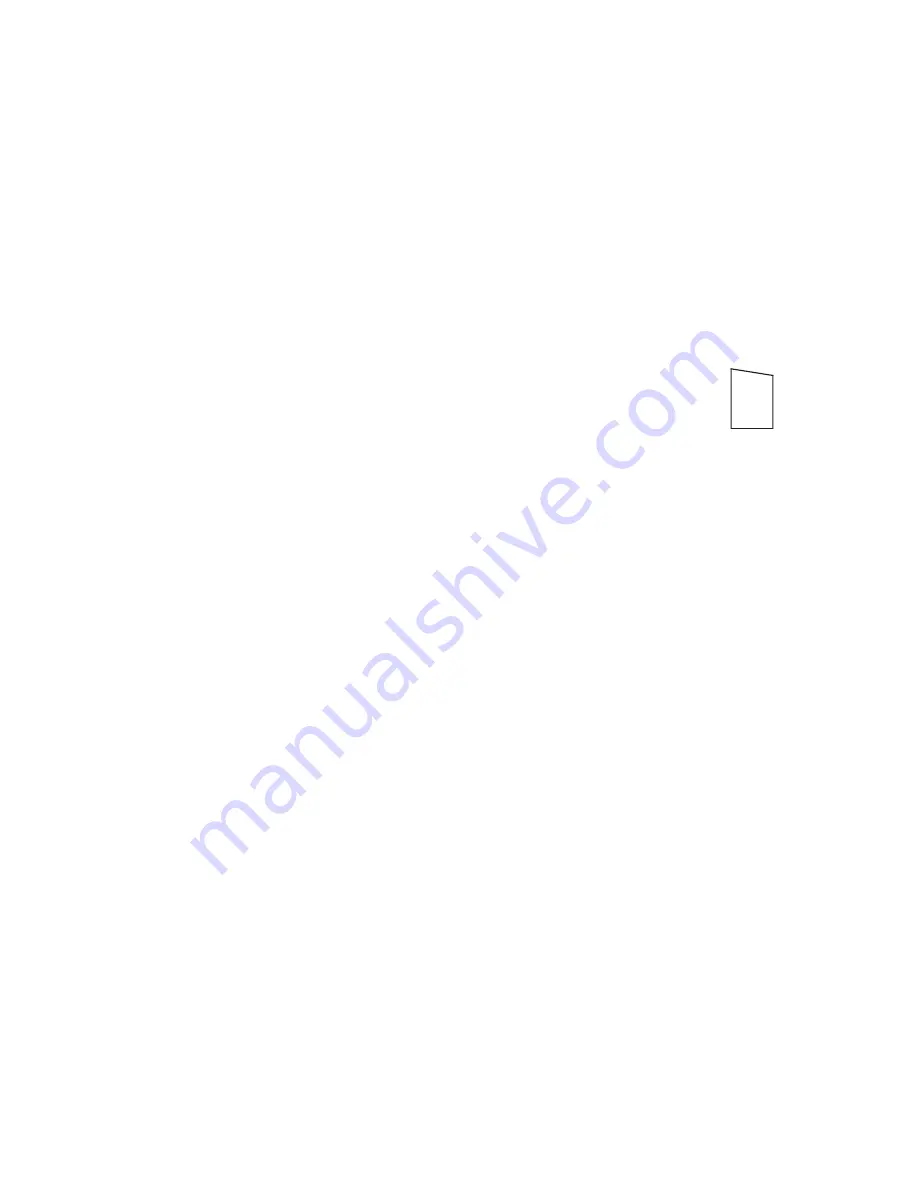
CAB ENDS PREP
17)
The underside of the roof gutter (where the roof gutter meets the door opening) is slightly
angled (a production process aid), carefully file this angle square in order to accurately fit the sides.
Check the fit of the sides against the cab ends - make sure you’ve got the correct end of the side to
work with, i.e. the non-baggage, and non-toilet ends. The sides should be level with the bottom edge
of the cab.
**TIP- Number the ends and sides on the inner surfaces to ensure each side mates with it’s appropriate
end later on.
18)
Prototype photographs reveal that not all units carried windscreen wipers on both left and right
cab windows (the centre window never has a wiper). Drill two 0.4mm dia. holes in the centre of both,
or right hand side window only (your choice) directly above the upper window beading to mount the
windscreen wipers later.
19)
Cut from scrap styrene 4 desk mountings as shown here (right), fix to the
floor of the cab against the cab front with the tallest side forward. See photo:
Craven inside cab for example (Cl. 105 model).
20)
Cut glazing to fit the windscreens now as this is very difficult to do once the body has been
assembled. Start with six pieces 15.5mm x 24.5mm and then round the corners sufficiently to clear
the moulded inside corners of the glazing recess inside the cab. DO NOT FIT just keep safe for now.
If you intend to illuminate the end lights these should now be drilled out as required. No provision is made
for this in the kit and so it is up to the builder to determine how best to achieve the installation.
NON-CAB ENDS PREP
These are our standard BR Mk1 coach ends and so have some details not required on a these units.
21)
Remove the moulded on end step mounting pads (raised rectangular details up the left hand
side), connector details (the two round ‘blobs’) and communication cord details flush with the surface
of the end.
22)
(DMBS only) Remove the pipe retainers at the lower edges of the end.
These operations are best achieved by shaving small amounts off with a sharp blade, followed by a fine
file and finally fine abrasive paper. See photo: End prep (Cl. 105 model).
23)
With a fine razor saw, cut off the moulded on bufferbeam level with the bottom of the end.
Use the underside of the end as a fence to guide the saw blade and finish off with a flat file to remove
any burrs.
24)
Give the ends a final inspection and rub over with fine abrasive paper before moving on.
BODY ASSEMBLY - NOW FOR THE FUN PART!
Whilst the solvents used to assemble the components evaporate very quickly the joints they produce take
considerably longer to achieve maximum strength. DO NOT RUSH THESE NEXT STEPS. Leaving ample
time for the joints to harden is essential and you will be rewarded for your patience by not having
unsound joints later on.
25)
(DMBS) Fix a cab end to one side at the opposite end to the baggage compartment and the
non-cab end to the other side adjacent to the baggage compartment to form an ‘L’ shape half box
as shown right.
4
14 mm
13 mm
10 mm