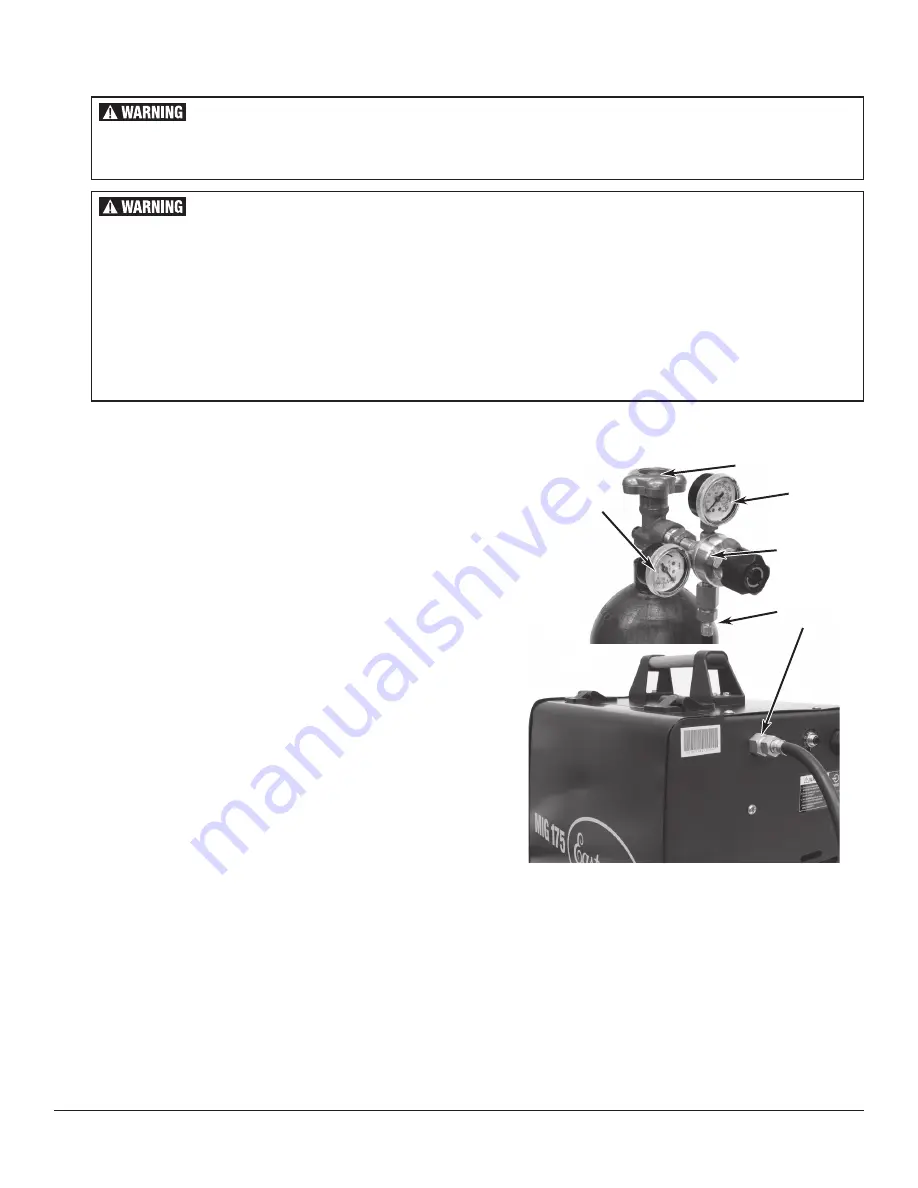
To order parts and supplies: 800.343.9353 >> eastwood.com
7
INSTALLING SHIELDING GAS SUPPLY
A Shielding Gas Bottle is not included with your Eastwood MIG175 but is necessary
to welding using Solid Wire. This can be bought at most local Welding Supply Stores.
Eastwood recommends the use of 75% Argon/25% CO2 for shielding gas when MIG
welding Steel, 100% Argon for Aluminum, and Tri-Mix (90% He/7.5% Ar / 2.5% CO2)
for Stainless Steel.
1.
Place the Eastwood MIG175 in its dedicated area or on a welding cart.
2.
Secure your Shielding Gas Bottle to a stationary object or mount to your welding
cart if it is equipped to hold one so that the cylinder cannot fall over.
3.
Remove the cap from the Shielding Gas Bottle.
4.
Insert the large brass male fi tting on the Shielding Gas Regulator into the female
fi tting on the Shielding Gas Bottle.
NOTE:
Do not use White Tefl on Tape on this connection as it is a compression
fi tting and does not require it, if you have a leak check for burrs or dirt in the
threads. If the leak persists, use gas type sealing tape.
5.
Tighten the fi tting with a wrench till snug, do not over tighten.
6.
Connect either end of the Gas Line included with your Eastwood MIG175 to
the fi tting on the regulator and wrench tighten till snug.
7.
Connect the other end of the gas line to the fi tting on the rear of the
Eastwood MIG175 and wrench tighten till snug.
8.
Check the gas line for leaks by slowly opening the valve on the gas bottle.
When welding the valve on the bottle should always be all the way open.
FIG. F
✓
✓
Flow
Regulator
✓
Hose feeds
to gas input
✓
Valve
✓
Bottle
Pressure
Gauge
✓
Gas Flow
Output
Gauge
BUILDUP OF GAS CAN INJURE OR KILL!
• Shut off shielding gas supply when not in use.
• Always ventilate confined spaces or use approved air-supplied respirator.
• Always turn your face away from valve outlet when opening cylinder valve.
CYLINDERS CAN EXPLODE IF DAMAGED!
Shielding gas cylinders contain gas under high pressure. If damaged, a cylinder can explode. As gas cylinders are a normal
component of the welding process, use extra care to handle them carefully.
• Protect compressed gas cylinders from excessive heat, mechanical shocks, physical damage, slag, open flames, sparks and
• Install cylinders in an upright position by securing to a specifically designed rack, cart or stationary support to prevent falling
or tipping over.
• Never weld on a pressurized cylinder or explosion will occur.
• Use only correct shielding gas cylinders, regulators, hoses and fittings designed for the specific application; maintain them and
all related components in good condition.
• Keep protective cap in place over valve except when cylinder is in use.
• Use proper equipment, procedures and have adequate help when moving or lifting cylinders.
Summary of Contents for MIG 175
Page 1: ...MIG175 WELDER SERVICE MANUAL Item 12012...
Page 16: ...16 Eastwood Technical Assistance 800 343 9353 tech eastwood com EXPLODED VIEW WITH PARTS LIST...
Page 18: ...18 Eastwood Technical Assistance 800 343 9353 tech eastwood com NOTES...
Page 19: ...To order parts and supplies 800 343 9353 eastwood com 19 NOTES...