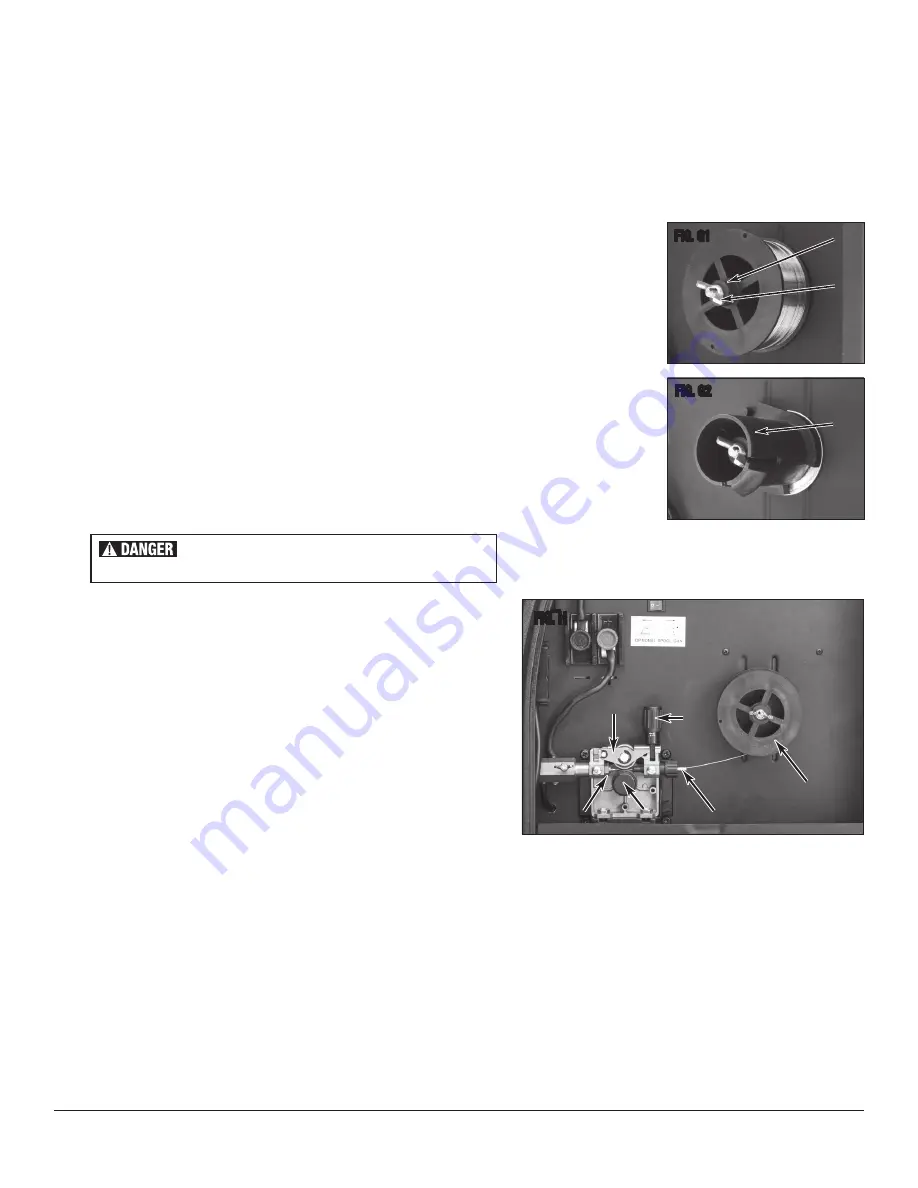
8
Eastwood Technical Assistance: 800.343.9353 >> [email protected]
INSTALLING WIRE SPOOL
The Eastwood MIG175 can be used with either a 4”or an 8” Wire Spool. To use the larger 8” spool an included adaptor is necessary.
To install a 4” Wire Spool:
1.
Open the door of the welder and remove the wing nut
(FIG. G2)
, spacer
(FIG. G1)
, and 8” Spool Adaptor
(FIG. G3)
from the Wire Spool Spindle.
2.
Slide the 4” Wire Spool onto the spindle and reinstall the spacer and the wing nut and place the 8” Spool Adaptor
(FIG. G3)
in a safe place if it is
needed in the future.
3.
To set the tension on the wire, tighten the wing nut till there is a slight resistance to spinning the wire spool on the spindle. If the tension is set too loose
the wire spool will spin on the shaft and unspool all of the wire. If the tension is too tight, the drive roller will have issues pulling the wire off the spool
and some slipping may occur.
NOTE:
Hold exposed wire end to keep the spool from unraveling.
To install an 8” Wire Spool:
1.
Open the door of the welder and remove the wing nut, spacer, and 8” Spool Adaptor from the Wire Spool Spindle.
2.
Slide the 8” Wire Spool Adaptor into the center of the wire spool.
3.
Slide the 8” Wire Spool Adaptor with the wire spool installed onto the spindle and reinstall the spacer and the
wing nut.
4.
To set the tension on the wire, tighten the wing nut till there is a slight resistance to spinning the wire spool on
the spindle. If the tension is set too loose the wire spool will spin on the shaft and unspool all of the wire. If the
tension is too tight, the drive roller will have issues pulling the wire off the spool and some slipping may occur.
CONNECTING THE WELDER TO A POWER SOURCE
The Eastwood MIG175 welder requires a dedicated 220 VAC 30 Amp grounded outlet protected by a time delay breaker.
The MIG175 is equipped with a NEMA 6-50P Plug which requires a NEMA 6-50R outlet to be connected.
THREADING WELDING WIRE THROUGH THE DRIVE MOTOR TO THE WELDING GUN
1.
Unlock the Pressure Adjuster
(FIG. H1)
on the wire tensioner and lift up the rocker
arm
(FIG. H2)
. Insure that the wire drive wheel is appropriate to the welding wire
size, see above describing the installation to wire feed roller installation.
2.
Pull out the welding wire
(FIG. H3)
from the welding wire spool carefully.
NOTE:
Do not let go of the wire prior to step 5 or the spool will unravel and
be useless.
3.
Cut off the small piece of the curved segment at the front of welding wire and
straighten the welding wire approximately 3.0” long.
4.
Thread the welding wire through the guide pipe
(FIG. H4)
and over the wire feed
roller
(FIG. H5)
and into the torch hole
(FIG. 6H)
.
5.
Reattach the rocker arm
(FIG. H2)
and reset the Pressure Adjuster
(FIG. H1)
on the wire feeder (now the welding wire will fed smoothly).
6.
Remove the contact tip and nozzle from the MIG Gun.
7.
Turn on the machine and set the wire speed about 1⁄2 on the scale.
8.
With the gun pointed away from you and others, depress the trigger to begin feeding wire.
NOTE:
Watch the drive roller to see if any slipping is occurring between the roller and the wire – if so turn the machine off and tighten the
Pressure Adjuster 1⁄4 turn and test again.
9.
You do not want too much tension on the tension roller as it will tend to deform the wire. Just enough to feed the wire without slipping
10.
Once the wire has emerged from the tip of the gun, turn the machine OFF and replace the tip and nozzle.
FIG. G2
✓
G3
✓
G2
✓
G1
FIG. G1
FIG. H
✓
H1
✓
H2
✓
H3
✓
H4
✓
H5
✓
H6
ELECTRIC SHOCK CAN CAUSE INJURY OR DEATH!
Disconnect welder from power supply before beginning.
Summary of Contents for MIG 175
Page 1: ...MIG175 WELDER SERVICE MANUAL Item 12012...
Page 16: ...16 Eastwood Technical Assistance 800 343 9353 tech eastwood com EXPLODED VIEW WITH PARTS LIST...
Page 18: ...18 Eastwood Technical Assistance 800 343 9353 tech eastwood com NOTES...
Page 19: ...To order parts and supplies 800 343 9353 eastwood com 19 NOTES...