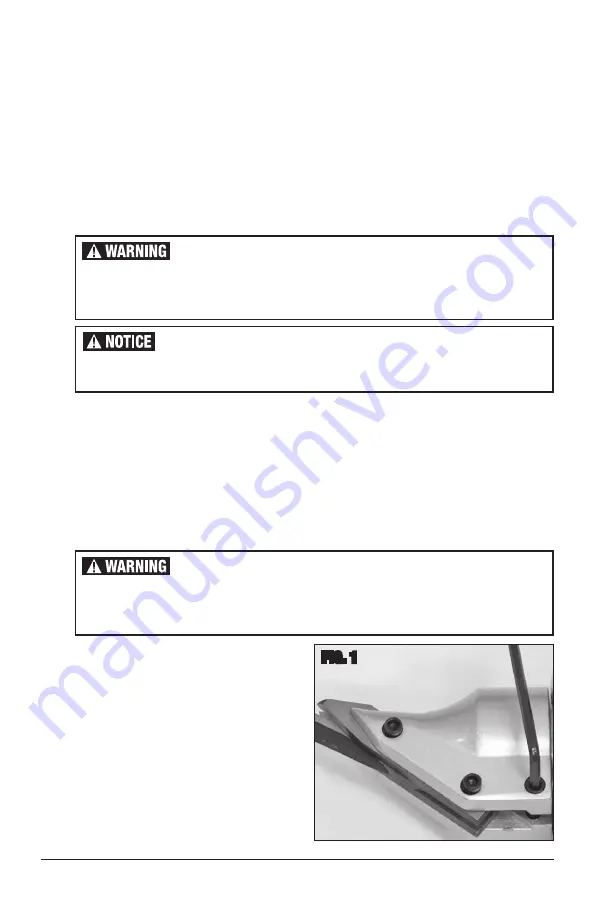
4
Eastwood Technical Assistance: 800.343.9353 >> [email protected]
EYE INJURY HAZARD!
Rapidly reciprocating Blades will eject sharp metal chips out of the front at
high velocity. Always wear ANSI approved eye protection when operating
this tool.
DO NOT attempt to exceed 18 Gauge (0.050”) [1.2mm] mild steel, aluminum
and copper or 20 Gauge Maximum (0.036”) [0.91mm] for stainless steel.
POSITIONING CUTTING HEAD
The Cutting Head may be rotated 360° in relation
to the Handle of the Shear Body to accommodate
cutting in difficult to reach areas. To do so:
• Using the included 4 mm Hex Key, loosen
(but do not remove) the three socket head
cap screws on the Cutting Head adequately
to release clamping pressure
(FIG 1).
• Rotate the Cutting Head about the axis of
the Shear Body to the desired position then
re-tighten the three screws.
SET-UP & CONNECTION
• Be sure that the air supply to the tool is clean and dry. Moisture in the supply line will quickly
damage the motor and valves.
• A minimum 3/8” I.D. air line should be used for optimal performance.
• Thread the included 1/4” Male Quick-Disconnect Fitting into the air inlet of the tool using a
quality thread sealing tape (not included).
OPERATION
• Place the cutting blades against work piece and depress trigger to actuate cutting.
• Always maintain a firm grip while operating tool, do not force but allow the reciprocating action
of the Cutting Blade to do the work.
• Be sure that the workpiece is clamped down or held securely to minimize the danger of injury
while operating tool.
INJURY HAZARD!
This Metal Shears can quickly start up when handling while connected to an
air supply causing serious personal injury. Always disconnect the tool from the
air supply before changing Cutting Blades or performing maintenance.
FIG. 1