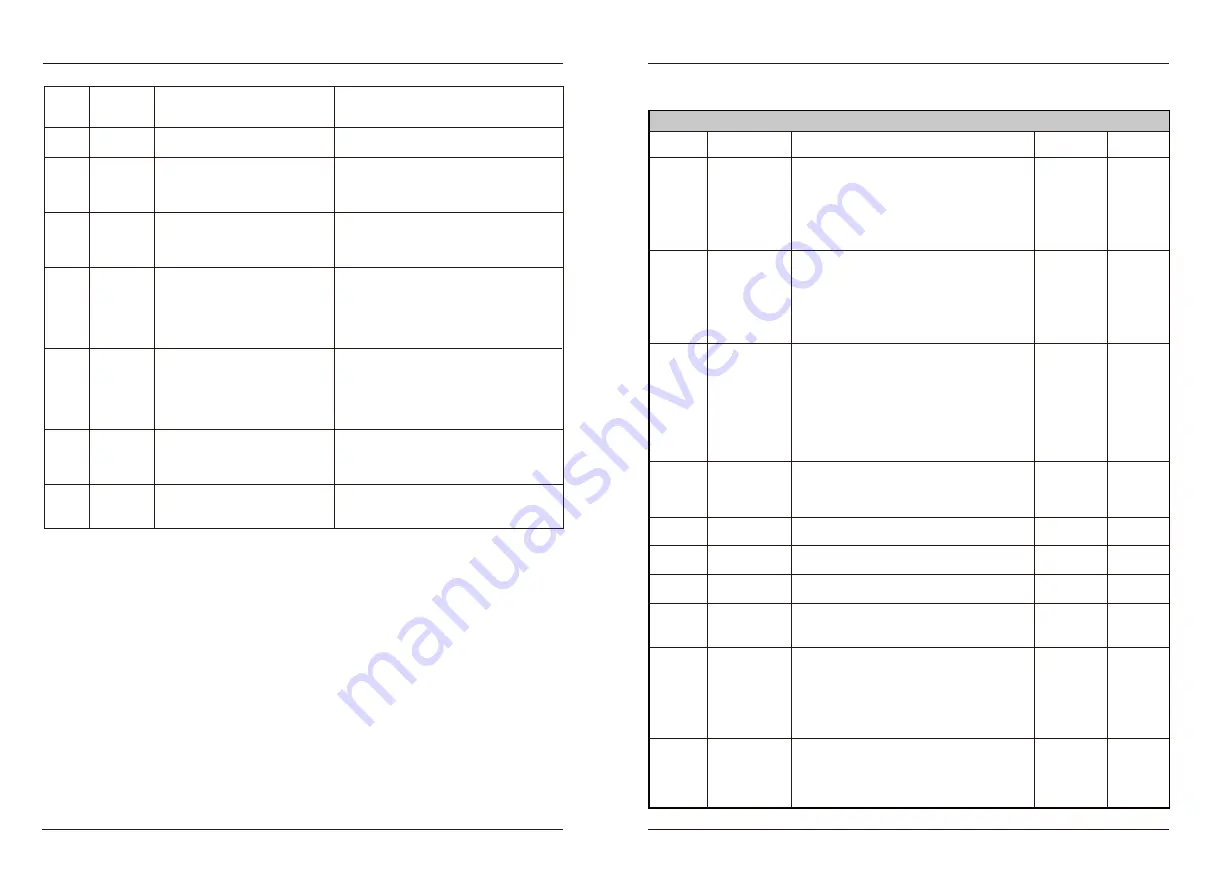
Err27
power-on
time
reached
Err28
1: Accumulative power-ontime
reaches the setting.
1: The AC drive running current
is lower than P9-38
.
1: Clear the record through the parameter
initialization function.
1: Check that the load is disconnected or
the setting of P9-38 and P9-39 is correct.
Err33
Err34
Err29
Err30
Err31
Err32
Load
becoming 0
Motor
overheat
Initial
position
fault
PID
feedback
lost during
running
Pulse-by-
pulse
current
limit fault
Too large
speed
deviation
Motor
over-speed
1: The cabling of the temperature
sensor becomes loose.
2: The motor temperature is too
high.
1: The motor parameters are not
set based on the actual situation.
1: The PID feedback is lower than
the setting of PA-27.
1: The load is too heavy or
lockedrotor occurs on the motor.
2: The AC drive model is of too
small power class.
1: The encoder parameters are set
incorrectly.
2: The motor auto-tuning is not
performed.
3: P9-42 and P9-43 are set
incorrectly.
1: The encoder parameters are set
incorrectly.
2: The motor auto-tuning is not
performed.
3: P9-40 and P9-41 are set
incorrectly
1: Check the temperature sensor cabling
and eliminate the cabling fault.
2: Lower the carrier frequency or adopt
other heat radiation measures.
1: Check the motor para-meters are set
correctly and whether the setting of rated
current is too small.
1: Check the PID feedback signal or set
PA-27 to a proper value.
1: Reduce the load and check the motor and
mechanical condition.
2: Select the AC drive of higher power
class.
1: Set the encoder parameters properly.
2: Perform the motor autotuning.
3: Set F9-69 and F9-70 correctly based on
the actual situation.
1: Set the encoder parameters properly.
2: Perform the motor autotuning.
3: Set P9-40 and P9-41 correctly based on
the actual situation.
7
.
Function Code Table
F u n c t i o n C o d e T a b l e
EC670
F a u l t s a n d s o l u t i o n s
EC670
-
9
-
-
10
-
A0
Basic parameter group
Address
Function
Code
Setting Range
A0
-
00
A0
-
01
A0
-
02
A0
-
04
A0
-
03
A0
-
07
Command source
selection
Preset main
frequency
Motor control
mode
Main frequency
source X
selection
Maximum
frequency
Rotation
direction
1000H
1001H
1002H
1004H
1003H
1007H
0
~
2
0: Voltage/Frequency (V/F)control
(direction LED on)
1: Sensorless flux vector control(SFVC)
(direction LED blinking)
2: Closed-loop vector control(CLVC)
(direction LED fast blinking)
0
~
4
0: Operation panel control (LOC LED on)
1: Terminal control (REM LED on)
2: RS485 Communication control (REM LED
blinking)
3.PV Auto-control (LOC REM on)
4: Terminal switchover (REM LOC LED blinking)
0
~
12
0: Digital setting P0-08
1: AI1 2: AI2 3: AI3
4: Pulse setting(HDI)
5: Communication setting
6: UP/DW setting 7: PID
8: Simple PLC 9: Reserved
10: Reserved 11: Option card
12: Terminal switchover
0.01
~
Maximum output frequency
0.00
~
50.00Hz
The maximum frequency limit allowed by the
frequency converter is also the acceleration
and deceleration time reference.
0000
~
0011
BIT0:0:Same direction 1:Reverse direction
BIT1:0:Reverse enable 1:Reverse disable
Default
0
4
0
50.00Hz
50.00Hz
Acceleration
time1
A0
-
05
1005H
0.1
~
30.0s
3s
0
Parameter Name
1008H
A0
-
08
Carrier
frequency
1
.
0
~
15.0KHz
If the carrier frequency is set higher than
the factory value, it will cause the tempe-
rature rise of the converter radiator to
increase. At this time, the user needs to use
the converter derating, otherwise the conver-
ter will have the danger of overheating alarm.
By type
Deceleration
time1
A0
-
06
1006H
0.1
~
30.0s
2s
1009H
A0
-
09
Restore
default
settings
0
~
65535
0
~
1:No function 2:Reset err mesage
3
~
6:Resv 7:Reset—User data
10:Back up current user parameters
210:Restore user backup parameters
0
~
210