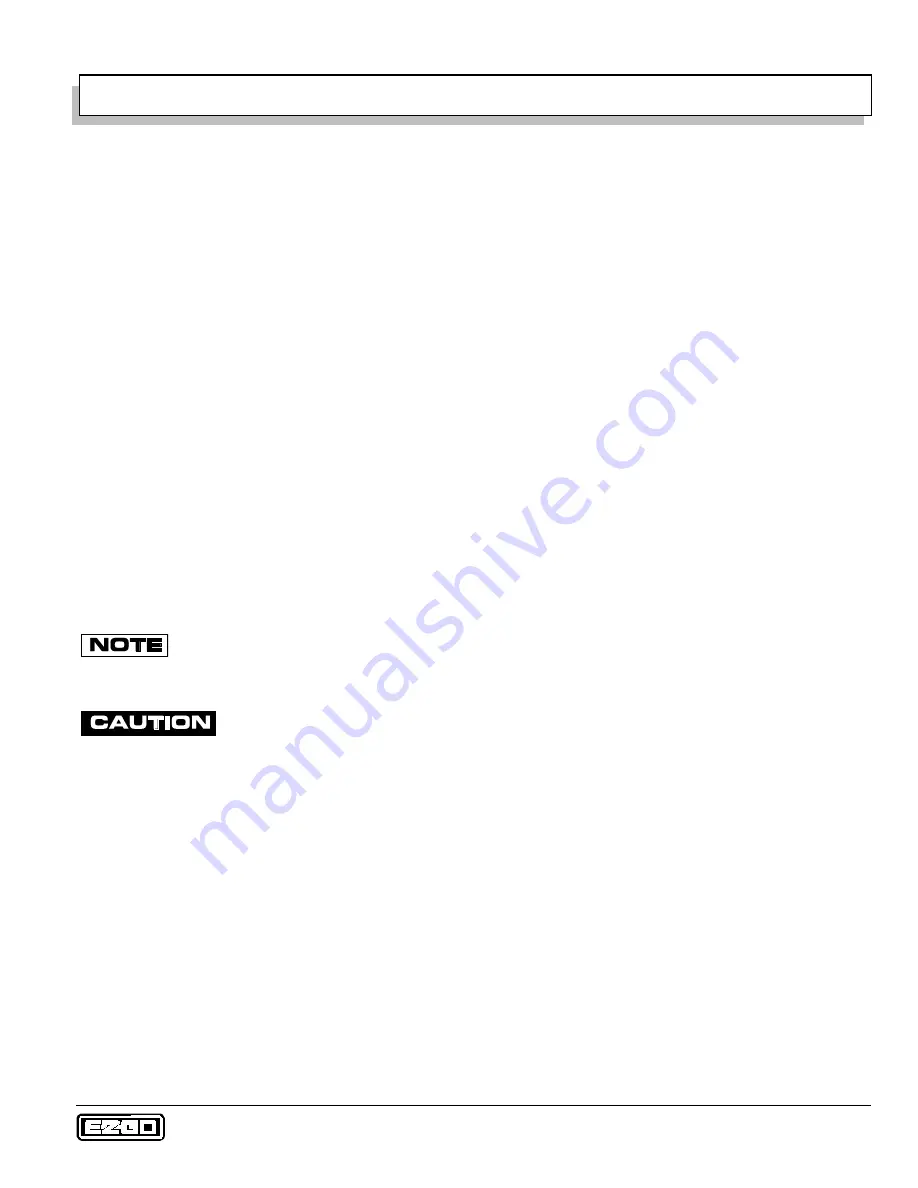
ENGINE REASSEMBLY
Page E-3
Engine Shop Rebuild and Parts Manual
F. Install the camshaft cover (ITEM 14) and new gasket
(ITEM 15).
1. With the flanged side of the cover oriented away
from the engine, hold the cover and gasket in
place and install three (3) bolts (ITEM 16,
M6x1.0x12L) and one (1) stud (ITEM 17, M6x1.0).
The stud is mounted in the top right corner of the
cover.
2. Tighten the mounting bolts and stud to specified
torque.
Install the Rear Timing Belt Cover
(See Fig. E-5 “Timing Belt Covers, Drive and Cam Pulleys, Idler and
Timing Belt” on page D-10)
(See Fig. E-6 “Timing Belt Covers, Drive and Cam Pulleys, Idler and
Timing Belt con’t” on page D-11)
A. Hold the cover in place and install two (2) bolts (ITEM
2, M6x1.0x8L, 10mm socket). (Later models have
only one (1) bolt)
B. Tighten the mounting bolts to specified torque.
Install the Drive and Cam Pulleys, Idler and
Timing Belt
(See Fig. E-5 “Timing Belt Covers, Drive and Cam Pulleys, Idler and
Timing Belt” on page D-10)
A special tool for holding the drive and cam pul-
leys in proper timing position while installing
the timing belt is available from the E-Z-GO Service Parts
Department (See Tool list).
Do not twist, crimp or turn the belt
inside out. This will cause the belt to
fail.
A. Install the drive pulley (ITEM 3).
1. If the key (ITEM 4) in the crankshaft does not align
with the crankcase mark, rotate the fan hub until it
is aligned.
2. Align the key slot in the rear belt retainer (ITEM 5)
with the key in the crankshaft and install it onto the
shaft.
3. Align the keyslot in the drive pulley (ITEM 3) with
the key in the crankshaft and slide the pulley onto
the shaft, flange side toward the engine.
B. Install the cam pulley (ITEM 6).
1. Align the notch on the rear of the cam pulley with
the pin on the cam shaft and slide the pulley onto
the shaft.
2. Rotate the cam pulley until the smallest of the
three holes on the face of the gear aligns with the
notch at the top of the rear timing belt cover.
3. Install the mounting bolt with lock washer (ITEM 7,
M8x1.25x20L) and washer (ITEM 8, 8.5x28x2.3t).
Do not tighten the bolt. (If the E-Z-GO CAM PUL-
LEY TOOL is being used, position it on the drive
and cam pulleys. See NOTE above.)
C. Install the idler (ITEM 9).
1. Insert the short extension of the idler spring (ITEM
10) into the small hole on the rear face of the idler
and position the spring on the raised surface of the
face. (DETAIL A)
2. Place the washer (ITEM 11, 8.5x16x1.2t) on the
idler mounting bolt (ITEM 12, M8x1.25x30L), and
insert the bolt through the idler. While holding the
short spring extension in place, position the idler
against the crankcase. Hand tighten the bolt into
the crankcase. Rotate the spring into the spring
stop.
D. Install a new timing belt (ITEM 13). (DETAIL A)
1. If the E-Z-GO CAM PULLEY TOOL is not being
used, check that the drive and cam pulleys are
aligned with their marks.
2. Position the belt on the drive pulley. Do not twist,
crimp or turn the belt inside out.
3. Rotate the idler counterclockwise until it the belt
can be placed on the cam pulley. Place the belt on
the cam pulley, then snug the bolt. (If the E-Z-GO
CAM PULLEY TOOL is being used, remove it.)
4. Install the drive pulley front belt guide (ITEM 14),
washer (ITEM 15, 6.5x22x2t) and retaining bolt
with lock washer (ITEM 16, M6x1.0x16L). Torque
to specification.
5. Loosen the idler bolt and allow the idler to tension
the belt. Rotate the crankshaft two turns and
tighten the bolt to specified torque.
Summary of Contents for 295cc
Page 7: ...Page vi TABLE OF CONTENTS Engine Shop Rebuild and Parts Manual Notes ...
Page 9: ...viii HOW TO USE THIS MANUAL Engine Shop Rebuild and Parts Manual ...
Page 11: ...ENGINE DISASSEMBLY Page A ii Repair and Service Manual Notes ...
Page 19: ...ENGINE DISASSEMBLY Page B ii Repair and Service Manual Notes ...
Page 29: ...ENGINE DISASSEMBLY Page B 10 Engine Shop Rebuild and Parts Manual Notes ...
Page 31: ...ENGINE MEASUREMENTS Page C ii Engine Shop Rebuild and Parts Manual Notes ...
Page 45: ...ENGINE MEASUREMENTS Page C 14 Engine Shop Rebuild and Parts Manual Notes ...
Page 47: ...ENGINE REASSEMBLY Page D ii Engine Shop Rebuild and Parts Manual Notes ...
Page 63: ...ENGINE REASSEMBLY Page D 16 Engine Shop Rebuild and Parts Manual Notes ...
Page 65: ...ENGINE REASSEMBLY Page E ii Engine Shop Rebuild and Parts Manual Notes ...
Page 95: ...LIMITED WARRANTY Page G ii Engine Shop Rebuild and Parts Manual Notes ...