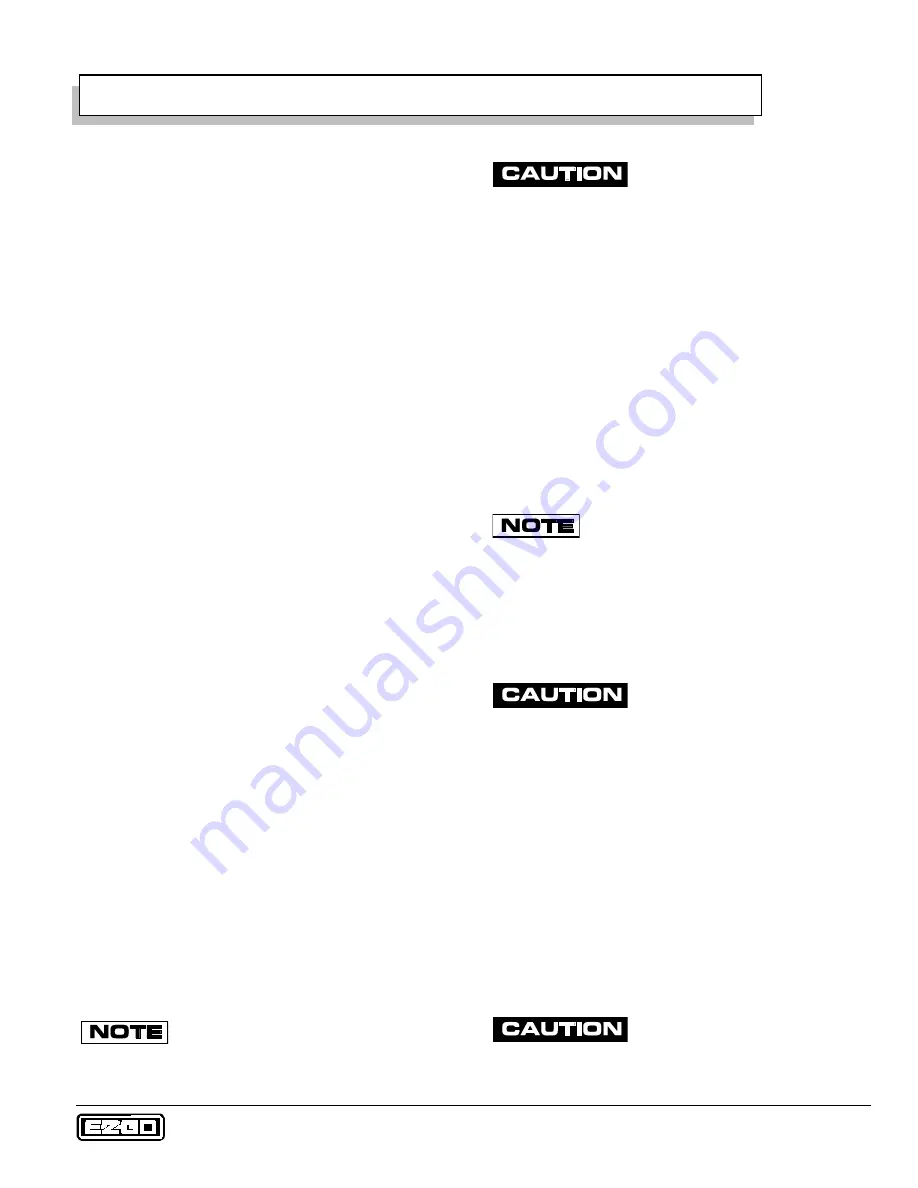
D
ENGINE REASSEMBLY
Page D-1
Engine Shop Rebuild and Parts Manual
‘CRANKCASE ASSEMBLY
Tool List
Qty. Required
Compressor, piston ring .............................................. 1
Drill, electric ................................................................ 1
Gauge, feeler
(E-Z-GO P/N 72525-G01) ........................................... 1
Gauge, wire spark plug ............................................... 1
Flex Hone, ball, 240 grit, 2 1/2 “cylinder
(E-Z-GO P/N 72517-G01) ........................................... 1
Installer, piston ring
(E-Z-GO P/N 72521-G01) ........................................... 1
Engine assembly lube, 8 oz.
(E-Z-GO P/N 72515-G01 ......................................... AR
Brush, cylinder cleaning, 2 1/2”
(E-Z-GO P/N 72519-G01) ........................................... 1
Oil, cylinder honing
(E-Z-GO P/N 72518-G01) ........................................... 1
Extension, 3/8” drive, 4" .............................................. 1
Extension, 3/8” drive, 6" .............................................. 1
Mallet, medium wood or rubber .................................. 1
Cam pulley alignment tool
(E-Z-GO P/N 27851-G01) ........................................... 1
Punch, non-ferrous ..................................................... 1
Ratchet, 3/8” drive....................................................... 1
Screwdriver, small flat blade ....................................... 1
Screwdriver, medium flat blade ................................... 1
Screwdriver, #2 phillips ............................................... 1
Screwdriver, #3 phillips ............................................... 1
Socket, 8 mm, 3/8” drive ............................................. 1
Socket, 10 mm, 3/8” drive ........................................... 1
Socket, 12 mm, 3/8” drive ........................................... 1
Socket, oil pressure switch ......................................... 1
Socket, 13/16” spark plug, 3/8” drive .......................... 1
Wrench, 7 mm combination ........................................ 1
Wrench, 10 mm combination ...................................... 1
Wrench 12 mm combination ....................................... 1
Wrench, torque, Inch and Ft. Lbs............................... 1
If the engine is not going to be put back into
service immediately, completely coat all inter-
nal engine components with assembly lube. Tape intake and
exhaust openings.
Prior to engine reassembly, all parts
must be thoroughly cleaned; free of
dirt, oil, grease, carbon deposits, or residue of any kind; free of
nicks, burrs, or damage of any kind to wear surfaces; and
inspected for excessive wear. Parts that are damaged or are not
within dimensional specifications should be replaced (or
machined if applicable). We recommend that parts found to be
acceptable but near limits be replaced if the engine will see high
usage.
Because some mating parts with wear surfaces were machined
together when the engine was manufactured, or have estab-
lished wear patterns during operation, the reassembly of engine
parts in their original positions and orientations with their origi-
nal mating parts is critical to the performance and life expectan-
cy of the engine.
When tightening (torquing) a number of screws or bolts in a giv-
en pattern, tighten them in two stages. Tighten them to 1/2 of
specified torque in one pass through the pattern, and then to
specified torque on the second pass.
All 4-cycle engine fasteners are plated, and
some are lubricated when installed. They are
considered “wet” and require approximately 80% of the speci-
fied torque of dry fasteners.
Hone the Crankcase Cylinder Bore
(See Fig. D-1 “Crankcase Cylinder” on page D-6)
A. Hone the cylinder bores only if new piston rings are to
be installed.
Make sure that all carbon residue has
been removed from the cylinder walls
before honing.
B. Install the crankcase end cover as shown in Fig. D-9.
C. Secure the crankcase to the work surface.
D. Lightly coat the cylinder bore with honing oil.
E. Insert the hone and adjust the speed and stroke rate
until a 30 - 50 cross hatch angle is achieved.
F. Allow the hone to stop within the bore before remov-
ing the hone
G. Clean the bore with a brush and shop solvent.
H. Measure the bore.
Reassemble the Pistons and Connecting
Rods
(See Fig. D-2 “Piston and Connecting Rods” on page D-7)
It is critical to the performance and life
expectancy of the engine that parts be
assembled in their original positions with their original mating
parts.
Summary of Contents for 295cc
Page 7: ...Page vi TABLE OF CONTENTS Engine Shop Rebuild and Parts Manual Notes ...
Page 9: ...viii HOW TO USE THIS MANUAL Engine Shop Rebuild and Parts Manual ...
Page 11: ...ENGINE DISASSEMBLY Page A ii Repair and Service Manual Notes ...
Page 19: ...ENGINE DISASSEMBLY Page B ii Repair and Service Manual Notes ...
Page 29: ...ENGINE DISASSEMBLY Page B 10 Engine Shop Rebuild and Parts Manual Notes ...
Page 31: ...ENGINE MEASUREMENTS Page C ii Engine Shop Rebuild and Parts Manual Notes ...
Page 45: ...ENGINE MEASUREMENTS Page C 14 Engine Shop Rebuild and Parts Manual Notes ...
Page 47: ...ENGINE REASSEMBLY Page D ii Engine Shop Rebuild and Parts Manual Notes ...
Page 63: ...ENGINE REASSEMBLY Page D 16 Engine Shop Rebuild and Parts Manual Notes ...
Page 65: ...ENGINE REASSEMBLY Page E ii Engine Shop Rebuild and Parts Manual Notes ...
Page 95: ...LIMITED WARRANTY Page G ii Engine Shop Rebuild and Parts Manual Notes ...