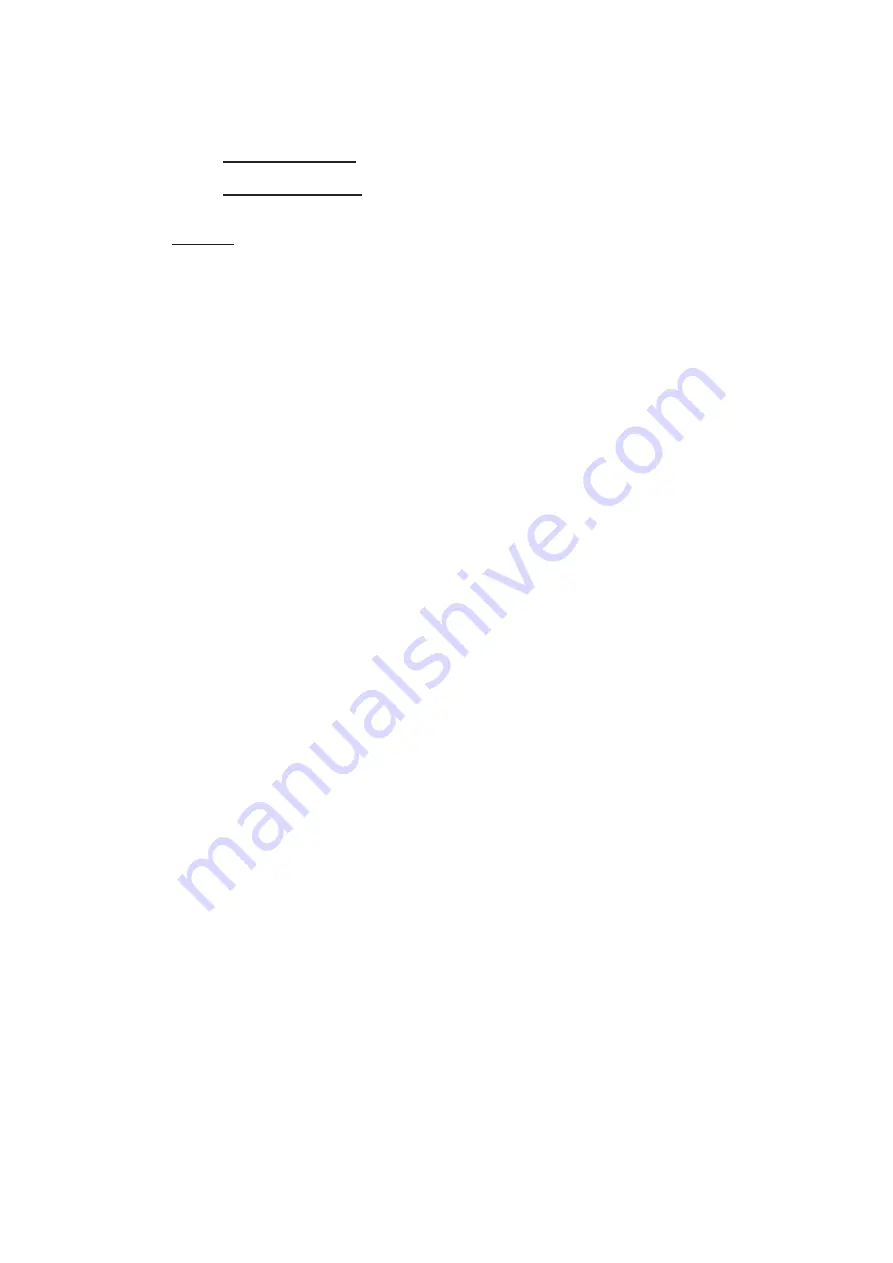
11
Hardware
6.1.2 General Information on 2-point v/T Calibration:
With 2-point calibration, v/T calibration / adjustment is performed at 2 different calibration points.
To ensure the smallest possible deviation in measuring results over the entire measuring range,
the two calibration points should be selected as follows:
- The
low calibration point should be in the lower third of the measuring range.
Calibration / adjustment must be performed using the V/T-CAL LOW function.
- The
high calibration point should be in the upper third of the measuring range.
Calibration / adjustment must be performed using the V/T-CAL HIGH function.
Example: EE75 T3***HV23 - measuring range = 0 ... 2 m/s
(0 - 400 ft/min).
Low calibration point (V-CAL LOW) should be around 0.4 m/s (0...0.7).
High calibration point (V-CAL HIGH) should be around 1.8 m/s (1.4...2).
6.2 Velocity Calibration
6.2.1 Calibration Procedure Using Configuration Software
See Configuration Software, chapter 4.9.3 - V Calibration Process Using a Configurator
6.2.2 Calibration Procedure Using Buttons on the Display Module (Optional)
1. Position the sensor head in the middle of the reference system (wind tunnel).
2. Stabilise the probe at the reference velocity (for at least 1 minute). The temperature of
the measuring probe and the reference system must be approximately the same.
3. Press both buttons for approx. 5 s to display the menu window.
4. Use the buttons and cursor so select the menu item "CALIBRATION" and confirm the
selection.
5. Select "V-Cal" and confirm the selection.
6.1 "1-point calibration":
- Select the calibration point as described in chapter 6.1.1.
- If calibration point > 50% of measuring range, select "V-CAL HIGH" and
confirm the selection.
- If calibration point < 50% of measuring range, select "V-CAL LOW" and
confirm the selection.
6.2 "2-point calibration":
- Select the low (high) calibration point as described in chapter 6.1.2.
- Approach the low (high) calibration point in the reference system, select
"V-CAL LOW" ("V-CAL HIGH”) on the sensor and confirm the selection.
7. The status line should display either CAL LOW (CAL HIGH).
8. The measuring value can now be adjusted with the reference value in 0.1m/s (20ft/min)
increments by pressing the UP or DOWN button. The updated value is displayed
immediately and present at the analogue output.
9. To save the adjusted measuring value in the instrument, press both buttons
simultaneously for approx. 5 s, then select "YES" in the "SAVE" menu and confirm the
selection. This exits the calibration routine and the sensor returns to normal
operating mode.
Selecting "NO" in the "SAVE" menu exits the calibration routine without saving the
adjusted measuring value.
10. In the case of 1-point v calibration, the procedure is now complete.
11. For 2-point v calibration, repeat steps 6.2-9 with the (high) calibration point.
6.3 Temperature Calibration
6.3.1 Calibration Procedure Using Configuration Software
See Configuration Software, chapter 4.9.4 - T Calibration Procedure Using a Configurator
6.3.2 Calibration Procedure Using Buttons on the Display Module (Optional)
1. Insert the sensor head in the temperature reference system.
2. Allow it to stabilise (min. 15 minutes). The greater the difference in temperature
between the measuring probe and the reference system, the longer the required
stabilisation time.
3. Press both buttons for approx. 5 s to display the menu window.
Summary of Contents for EE75
Page 23: ...22 Configurations Software...