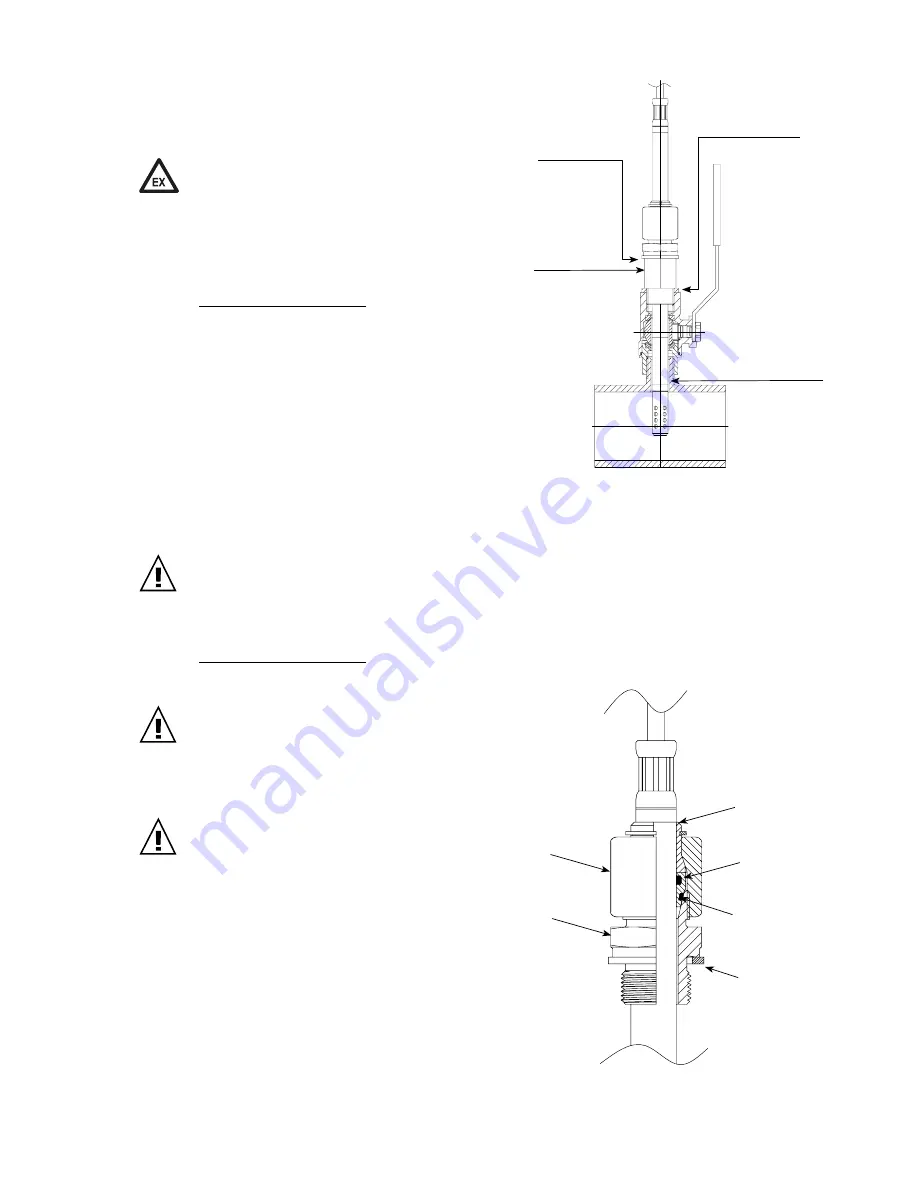
18
3.5.3 Mounting the probe using ball valve (optional)
With ball valve mounting, the system being meas-
ured does not need to be emptied or brought to a
standstill to mount or remove the probe.
Install the sensor head against the flow direction.
It is only permitted to use one ball valve that is
approved for use in explosion hazard areas.
The process pressure must be below 10bar
(145psi).
The two metal sealing rings (see figure) should be
replaced each time after being screwed on.
MOUNTING THE PROBE:
The mounting temperature is not permitted to
deviate from the usage temperature by more than
±40°C
(104°F)
.
•
Mount the probe with the ball valve closed.
•
Open the ball valve.
•
Insert the sensor head through the ball valve
into the process. A manual pressing tool is
recommended at high pressure.
•
To ensure that the probe is securely installed, the closing nut must be tightened at a
defined torque of 30Nm.
If there is no torque wrench present, tighten the closing nut by hand as far as possible.
Turn another ~50° using a suitable open-ended spanner.
A tightening torque that is too low results in a lower clamping force (fixing force) of the
clamp sleeve. There is therefore a risk of injury due to the probe tube being driven out.
An excessively high tightening torque can result in the permanent deformation of the
clamping sleeve and the probe tube. This makes the removal and re-mounting process
more difficult or impossible.
REMOVING THE PROBE:
•
Hold the probe tube tight. (Caution: Do not
bend the connection cable)
•
Slowly unfasten the closing nut using a
spanner (spanner size 24) until the drive-
out force affects the tube. Never fully
remove the closing nut when installed, and
instead screw on only as far as possible!
•
After the sensor head has been removed
from the process as far as it will go, close
the ball valve.
•
The probe can be fully removed.
Both for mounting and removal, ensure that
O-ring 1 is correctly installed.
If damaged, O-ring 1 can be replaced by the
user.
O-ring type: 13x1.5mm
(0.5"x 0.06")
- FKM-60
Spare part order no. HA050308
Metal sealing ring
(included with the ball
valve set as standard)
Internal diameter:
≥
13.1 mm (0.51")
Extension
(not provided with an NPT
thread)
Metal sealing ring
(as standard
with probe)
Clamp sleeve
Sealing
nut
Fitting body
O-ring 2
O-ring 1
no aluminium
is permitted
Summary of Contents for EE300E Series
Page 26: ...34 10 EC Declaration of Conformity...
Page 27: ...35 11 IECEX CERTIFICATE OF CONFORMITY COC...
Page 28: ...36...
Page 29: ...37...
Page 30: ...38...