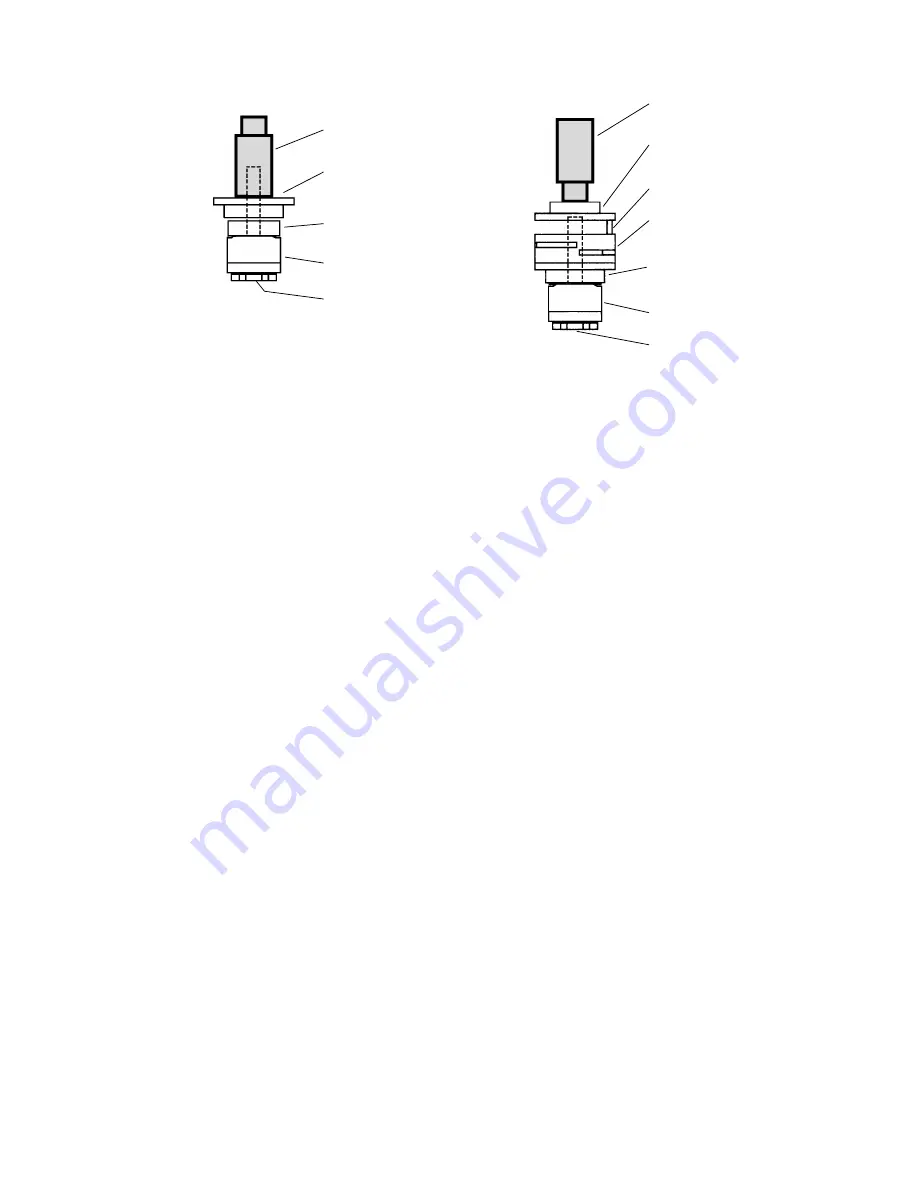
To Assemble (Continued):
10.
Place
59077
Rear Bearing Plate (with
58368
Bearing pressed into place) over shaft and "long" end of line-up pin and press fit in place as
shown in
Drawing 4
.
11.
Install
98463
Snap Ring in groove.
12.
Place
01024
O-Ring into recess in side wall of cylinder.
13.
Install
50659
O-Ring into
59058
Lock Ring. Slide the lock ring assembly over the motor shaft balancer (3/32" and 3/16" orbits only). Apply 1 drop of
pneumatic tool oil and spread between the motor bearing plate and
50659
O-Ring.
14.
Place 1 drop of pneumatic tool oil on
01024
O-Ring.
15.
Secure motor housing in vise, using
57092
Collar or padded jaws. Slide motor assembly into second housing.
Note:
Be certain line-up post enters the
notch in the bottom of the housing and
01024
O-Ring stays seated in cylinder.
16.
Tighten lock ring with
56058
Lock Ring Tool to 23 N•m/200 in.-lbs. Attach weight-mated sanding pad.
Valve and Speed Regulator Assemblies:
1.
Secure housing in vice using
57092
Collar or padded jaws.
2.
Remove inlet bushing,
01468
Spring,
58365
Tip Valve and
01464
Seal from housing. Remove
98927
Pin from housing and lever.
3.
Remove
95697
Snap Ring. Press the speed regulator and valve stem out of the housing. Remove the
01025
O-Rings (2) and
98459
O-Ring.
4.
Place new
01025
O-Rings (2) on the speed regulator and a new
98459
O-Ring on the valve stem. Then place in housing with valve stem. Install new
95967
Snap Ring. Apply a small amount of pneumatic tool oil to valve o-rings.
5.
Place new
01464
Seal in housing. Using tweezers or needle nose pliers, place the tip valve into housing so that the tip valve goes under the valve
stem. Place new
01468
Spring into housing so small end is towards tip valve.
6.
Apply a small amount of #567 Loctite
®
(or equivalent) around the threads of the first inlet bushing and tighten into housing to 23 N•m/200 in. - lbs.
7.
Install Lever on housing with
98927
Pin centered on housing.
Note:
Motor should operate at between 11,000 and 12,000 RPM at 6.2 bar (90 PSIG). RPM should be checked with a tachometer. Before operating,
we recommend that 2-3 drops of Dynabrade Air Lube P/N
95842
(or equivalent) be placed directly into the air inlet with throttle lever depressed. Operate the
machine for approximately 30 seconds before application to workpiece to determine if machine is working properly and safely and to allow lubricating
oils to properly dispense through machine.
Loctite
®
is a registered trademark of the Loctite Corp.
Disc Pad Change:
1.
Insert
50679
Wrench on flats of
57069
Balancer Shaft and twist off sanding pad by hand.
2.
With wrench still in place, hand tighten new pad on tool.
3.
No need to remove shroud or overskirt.
Required Weight of Pads:
3" Models –– Use pad weighing 75g.
3-1/2" Models –– Use pad weighing 80g.
5" Models –– Use pad weighing 100g.
6" Models –– Use pad weighing 130g.
57091
Bearing Press Tool
Balancer Shaft Assembly
Motor Shaft Balancer
58368
Bearing
59076
Front Bearing Plate
Drawing 3
57091
Bearing Press Tool
Balancer Shaft Assembly
Motor Shaft Balancer
59076
Front Bearing Plate
(with
58368
Bearing)
59077
Rear Bearing Plate
(with
58368
Bearing)
59051
Cylinder Assembly
(w/Rotor and Vanes)
Line-Up Pin
Drawing 4
Motor Assembly/Disassembly Instructions - Dynorbital -Spirit
™
8
Buy parts on line at https://Dynashop.co.uk/ for all things Dynabrade
Buy parts on line at https://Dynashop.co.uk/ for all things Dynabrade