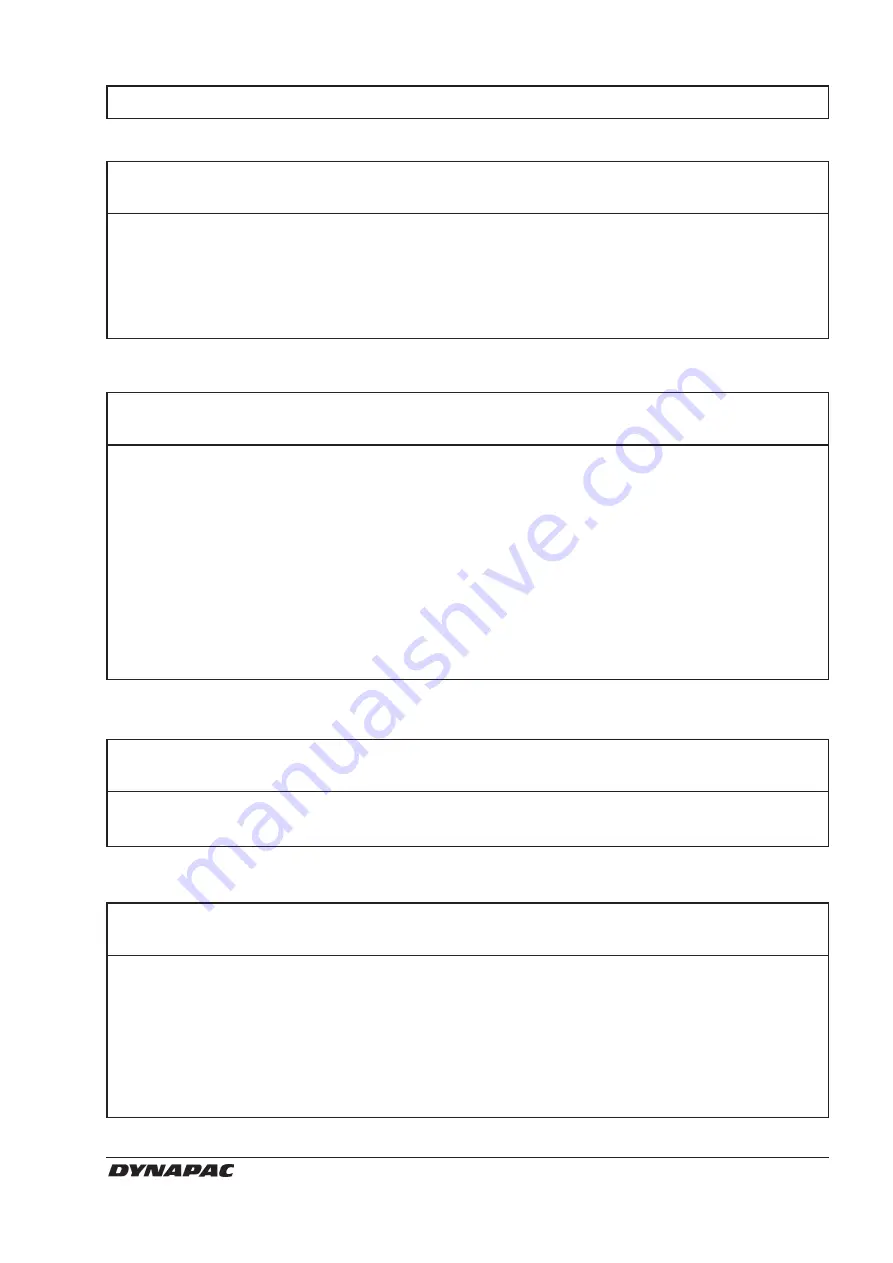
9
CC 722/722C M722EN2
MAINTENANCE MEASURES
Items in
Measure
See page
Comments
fig. 1
16
Check belt tension of the radiator fan and
alternator
See engine manual
21
Change the engine oil and oil filter
See engine manual
9
Check the oil level in the pump drive
18
18
Check oil level in the drum drives
(2 on CC 722)
18
Items in
Measure
See page
Comments
fig. 1
12
Change the hydraulic fluid
21
6
Check oil in the drums
(2x2 on CC 722)
21
18
Change oil in the drum drives (2 on CC 722)
22
1
Empty and clean the water tanks
9
Change oil in the pump drive
22
10
Replace the hydraulic filter and clean the
outside of the hydraulic fluid cooler
17
Every 2000 hours of operation (yearly)
Every 250 hours of operation (monthly)
Every 500 hours of operation (every three months)
Items in
Measure
See page
Comments
fig. 1
6
Check oil level in the drums
(2x2 on CC 722)
19
19
Lubricate controls, pivoted joints and the
control table bearings
19
4
Control tighten engine suspension and
bolted joints
20
3
Drain condensation from the fuel tank
20
12
Drain condensation from the hydraulic
reservoir
20
22
Replace the engine fuel filters (2 off)
See engine manual
21
Change the engine oil and oil filter
See engine manual
Items in
Measure
See page
Comments
fig. 1
Check/adjust engine valve clearance
See engine manual
16
Check the belt stretcher, engine
See engine manual
Every 1000 hours of operation (every six months)
Summary of Contents for CC 722C
Page 2: ...19 ILF015WO1...