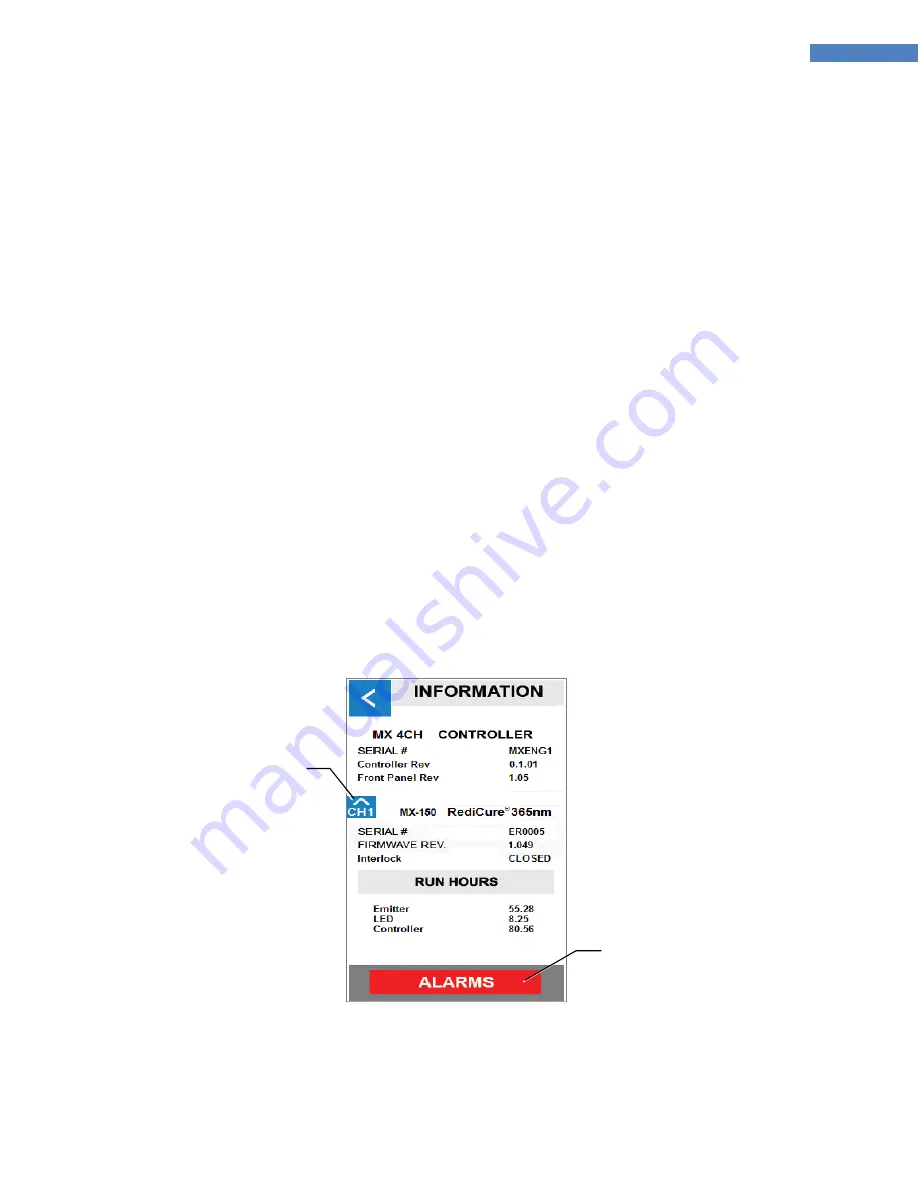
25
BlueWave® MX-Series Multichannel Controller User Guide
Loading and Saving Programs
The curing settings (program) may be saved to internal memory by highlighting a program name and pressing
“SAVE”, which will bring up a QWERTY keyboard for program name entry.
Previously saved programs may be
recalled by highlighting the desired program name and pressing “LOAD”. The Back button will return the user to
the previous screen.
When entering program names for different curing settings, utilize a dash or dot to separate words as the use of a
“
space
”
is not supported by this system.
To load a curing program, press the Program Button on the bottom of the screen. A list of available programs will
appear. Select the appropriate one and press “LOAD”. The program will load and you will be brou
ght back to the
Control Screen.
System Screens
System Information
The System Information Screen can be accessed by pressing the Information Button in the top left corner of the
Production or Admin Screens. Information such as the controller model number and the serial number, firmware
revision, and run hours for the Emitter can be found here.
This screen has two main buttons, the Channel Select Button and the Alarms Display Buttons. Pressing the Channel
Button insert scrolls
through each emitter’s data.
Pressing the Alarm display button will access the Alarms Screen.
Figure 19. Information Screen
Channel Select Button
Pressing the Channel Button
insert scrolls through each
emitter’s data.
Alarm Display Button
Pressing the Alarm display
button will access the Alarms
Screen.