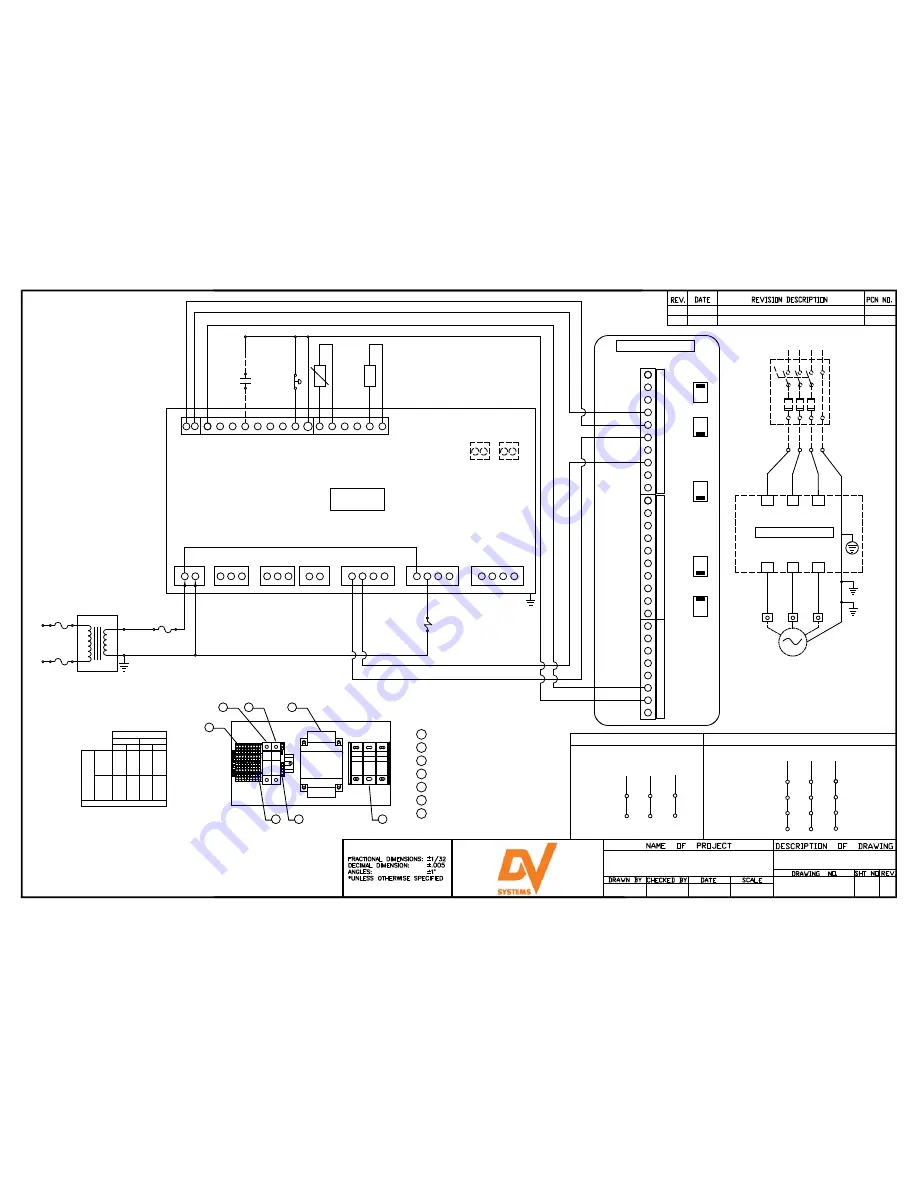
SCREW COMPRESSOR VARIABLE SPEED
CONTROLS G25-30 II, 200/230V
ELECTRICAL SCHEMATICS
CSC300 & VACON 100 VFD
GII-VSD-CSC300-200230
E.H.
01/27/17
N.T.S.
VOLTAG
E
F1
F2
F3
1
1
2
TRANSFORMER
PRIMARY FUSE F1
3
PRIMARY FUSE F2
4
SECONDARY FUSE F3
5
TERMINAL BLOCK
6
GROUND TERMINAL
PANEL SCHEMATIC
MOTOR
T3
T2
T1
T1
T2
T3
L1
L2
L3
POWER CIRCUIT SCHEMATIC
L1
OR
DE
R S
E
P
A
R
A
T
E
L
Y
FU
SI
BL
E DI
SC
O
N
N
E
C
T
F4
5
L2 L3 GND
CONTROL
PANEL
CONTROL
PANEL
DOOR
1.5 1.5
IMPORTANT NOTE: This print is the confidential property of DV SYSTEMS, INC.
It is not to be used or reproduced in any manner, nor submitted to other parties
for examination without the prior approval of DV SYSTEMS, INC.
DV SYSTEMS, INC. is continuously trying to improve its products, specifications
subject to change without notice.
FUSE TABLE
WARNING: USE THE SAME FUSE TYPE & RATING
R
E
FE
R TO
S
A
LE
S D
R
A
W
O
M
G
VACON100 VFD
POWER CONNECTION
FO
R IN
FO
MOTOR CONNECTION
MOTOR WIRING CONNECTION
( DELTA )
5
4
10
6
11
12
MOTOR
WIRING
230
NA
5
1.5 1.5
200
T1
T2
T3
1
6
2
4
3
5
230V MOTOR WIRING
200V MOTOR WIRING
MOTOR
WIRING
24 VAC
XO5
T
0
+24VAC
P
F1
F2
L1
L2
F3
+
C
CSC300
1
2
2
0
0
10 15 14
12
+
BLK
WHT
-
16
X13
XO9
RELAY OUTPUTS
9
S
13
-
3 PHASE
X12
L1 L2 L3
a
CT1
X11
b
c
CT2
X10
a
C
C R1 R2 R3
XO8
RELAY OUTPUTS
C R4 R5 R6
XO7
PROGRAMMABLE
C R7
R8
C
RELAY OUTPUTS
AN
A-
O
AN
A-G
DI
1
DI
2
DI
3
DI
4
DI
5
DI
6
DI
7
DI
8
C-A
N
1
AN1
AN2
AN3
C-A
N
2
C-A
N
3
L1 L2
XO6
L1 L2
3
4
6 5
9
X01
DIGITAL INPUTS
X02
ANALOGUE INPUTS
X03
E
10
10
8
RSS
10
MICROPROCESSOR
NA
E
- EMERGENCY STOP
P
- PRESSURE TRANSDUCER
S
- SOLONOID N.C.
T
- TEMPERATURE SENSOR
RSS - REMOTE START/STOP
(FIELD OPTION:
INSTALL RSS TO #16 AND
#10 TERMINAL BLOCK.
INSTALL WIRE FROM #16
TO DI5. ON P18 CHANGE
P18.08 FROM 'OFF' TO
'DI REMOTE START'.
ON P10 CHANGE P10.12
FROM 'KEYPAD' TO
'EQUIPMENT DI')
X07
- R7 AND R8 FOR
PROGRAMMABLE RELAY
OUPUT FUNCTION
*WITHIN 20.4V AND 27.6V*
01/27/17
NEW PRODUCT
15-24
(DSC-002361)
12
34
56
78
9
10
11
12
13
14
15
16
17
18
19
30
VACON100 VFD
CONTROL CONNECTION
3
4
5
6
A
B
21
22
23
24
25
26
8
10
U
I
A1
U
I
FLOAT
GND
A2
DIO'S
U
I
AO1
OFF
ON
RS-485
termination
T1
T2
T3
3
9
2
8
1
7
7
POWER BLOCK
3
4
5
2
6
7
ATQR, CC
5MM