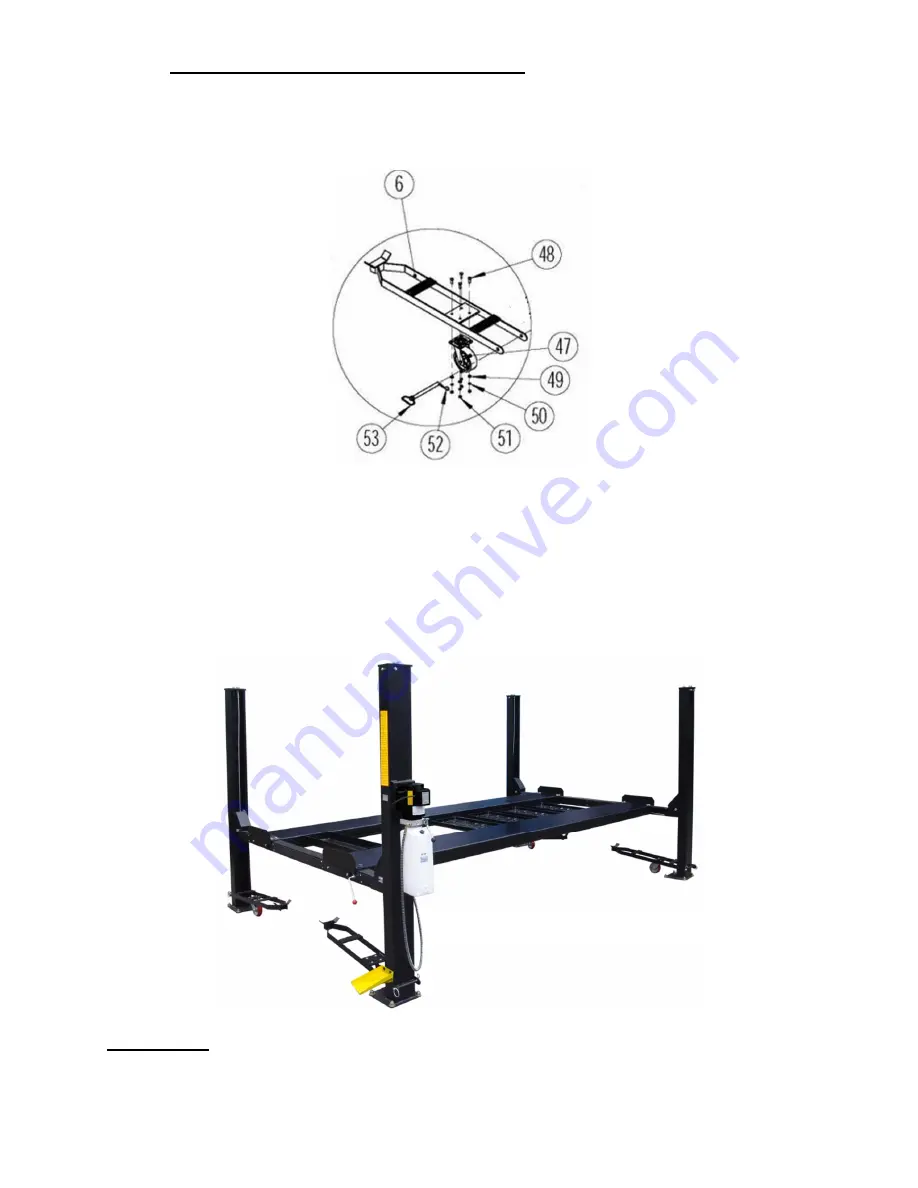
14
DM4P10K
July 2018
(OPTIONAL) - CASTER KIT ASSEMBLY INSTALLATION
1. Raise the Lift two to four feet high.
2. Assemble Caster assemblies as shown below.
3. Position each of the four Caster assemblies below the Crossbeam rails, as shown on page
6 and on Fig. 9.
4. Install the four Pivot Pins (#53) and Hairpin Cotter Pins (#52) to secure Caster assembly to
each Column.
5. Lower the Lift confirming that the Caster assemblies engage the underside of Crossbeams
and all four Columns rise to clear the floor.
CAUTION:
DO NOT maneuver Lift with Casters, while vehicle is on Lift.
Read Safety & Operation Instructions before operating Lift.
(Shown with optional Caster Kit, Jack Tray & Drip Trays)