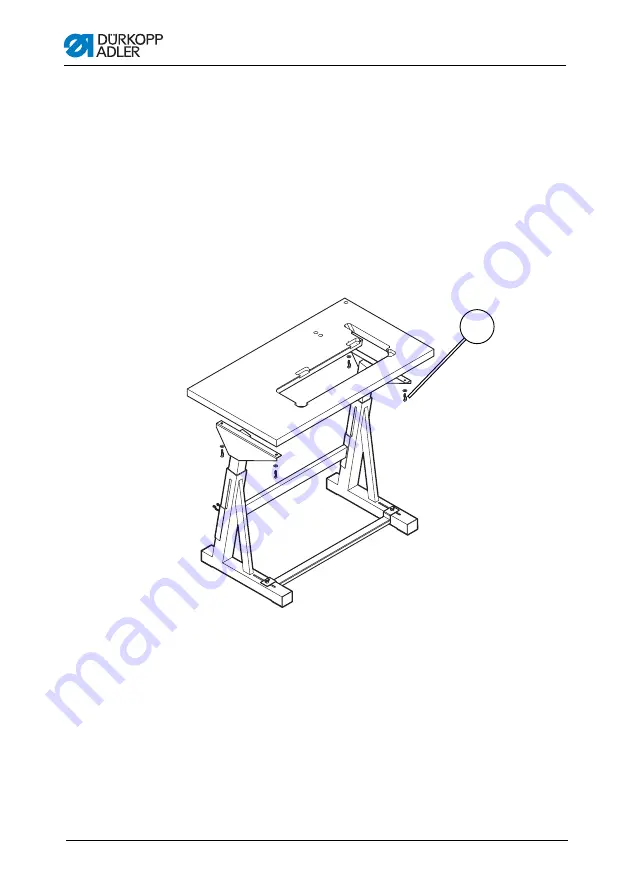
Set-up
Operating manual H868 Version 00.0 - 07/2013
52
6. Screw the thread real holder and the unwinding bracket onto
the thread reel holder (1) in such a way that they are exactly
opposite each other.
7. Insert the plug (2) in the hole.
8. Insert the rubber mounts of the hinge in the recesses (6).
9. Insert the rubber corners in the corner protrusions (3) of the
recess for the machine.
6.6
Fastening the table plate to the frame
Figure 34: Fastening the table plate to the frame
1. Place the table plate on the head sections of the inner bars.
2. Screw the table plate
firmly in place at the 4 screw holes (1).
(1) - Screw holes and screws
1
Summary of Contents for H868
Page 1: ...H868 Operating Manual ...
Page 18: ...Device description Operating manual H868 Version 00 0 07 2013 16 ...
Page 72: ...Set up Operating manual H868 Version 00 0 07 2013 70 ...
Page 74: ...Decommissioning Operating manual H868 Version 00 0 07 2013 72 ...
Page 76: ...Disposal Operating manual H868 Version 00 0 07 2013 74 ...
Page 79: ......