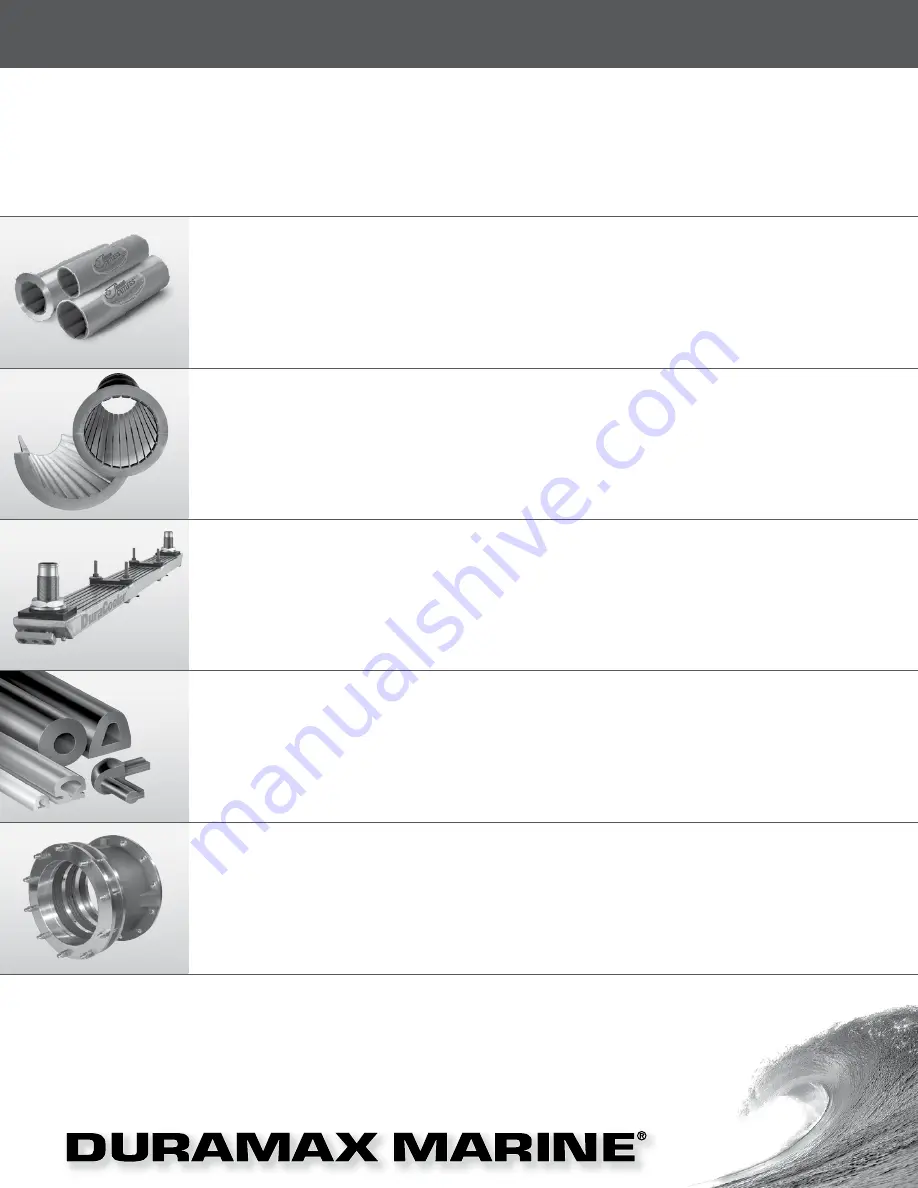
INNOVATION.
EXPERIENCE.
RESULTS.
Duramax Marine
®
is committed to providing excellence in every product
we manufacture. Our Johnson Cutless
®
marine and industrial bearings,
heat exchangers, impact protection systems and sealing systems are known
worldwide for their engineered quality and dependable performance. Please contact
the factory for information on any of the following Duramax Marine
®
products:
Duramax Marine
®
is an ISO 9001:2015 Certified Company
©2019 Duramax Marine
®
17990 Great Lakes Parkway
Hiram, Ohio 44234 U.S.A.
PHONE 440.834.5400
FAX 800.497.9283 USA & Canada
or 440.834.4950
www.DuramaxMarine.com
JOHNSON CUTLESS
®
WATER-LUBRICATED BEARING SYSTEMS
Johnson Cutless
®
Sleeve and Flanged Bearings
DX 490 Rudder Bushings
DURAMAX
®
HEAT EXCHANGE SYSTEMS
DuraCooler
®
Keel Coolers
Duramax
®
Demountable Keel Coolers
Duramax
®
BoxCoolers
Duramax
®
Plate Heat Exchangers
DURAMAX
®
IMPACT PROTECTION SYSTEMS
Johnson
®
Commercial Dock Bumpers, Fenders & Tow Knees
Weatherstrip Door Gaskets, Window Channel and Hatch Cover Gaskets
LINERITE
®
Composite Batterboard Systems
DURAMAX
®
ADVANCED WATER-LUBRICATED BEARING SYSTEMS
Johnson
®
Demountable Stave Bearings
ROMOR
®
I Stave Bearings and Segmental Housings
ROMOR
®
C- Partial Arc Bearings
DMX
®
Polymer Alloy Bearings
DuraBlue
®
Bearings, Rudder & Pintle Bushings, Thrust Washers, and Wear Pads
Industrial Pump Bearing Systems
DURAMAX
®
SHAFT SEALING SYSTEMS
DryMax
®
Shaft Seal & Rudder Seal
Duramax
®
Mechanical Shaft Seal
Johnson
®
Heavy-Duty Air Seal Stuffing Boxes
Duramax
®
Ultra-X
®
High Performance Compression Packing
Johnson
®
Strong Boy Stern Castings and Stuffing Boxes
DM-1025.102 BCI 08-15-19