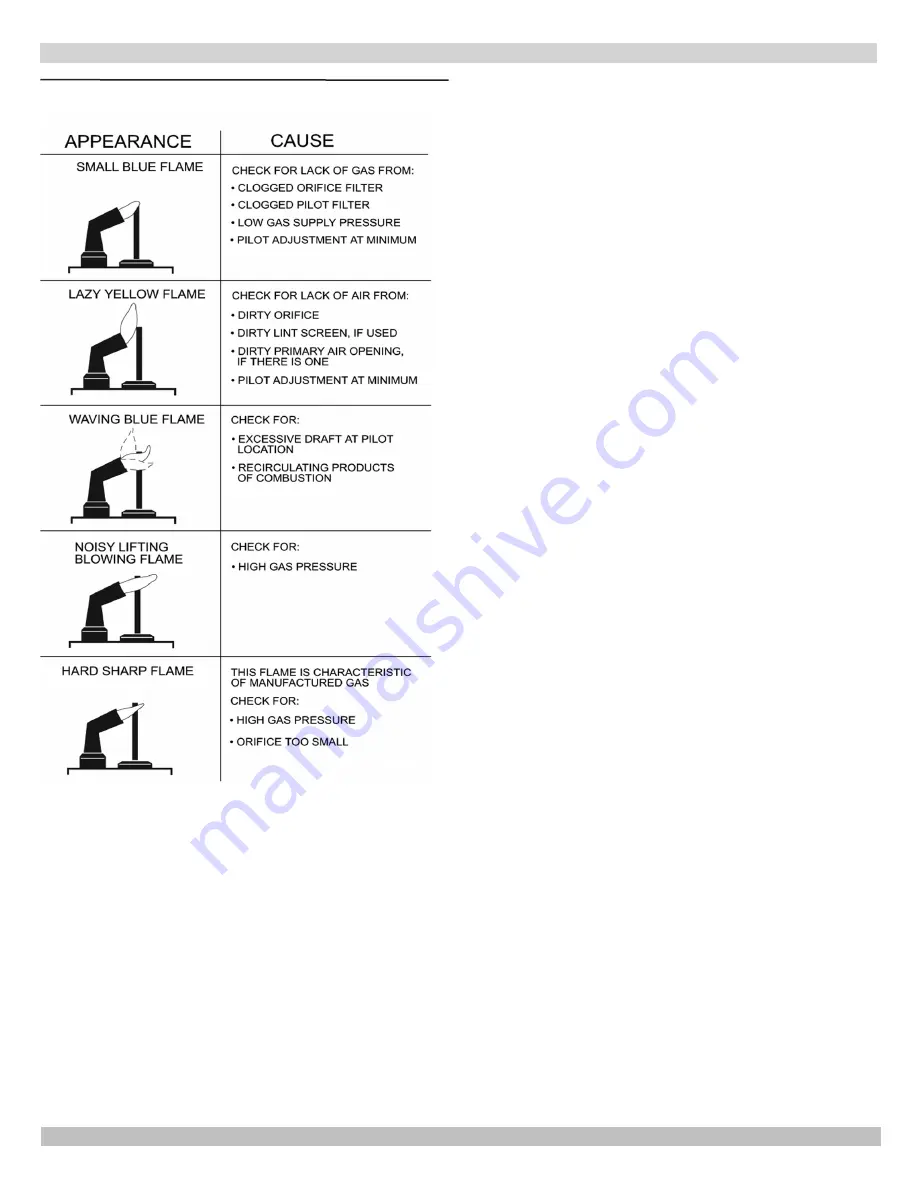
26
INTERMITTENT PILOT TROUBLESHOOTING
Correct Pilot Flame: 3/8 to 1/2 inch in flame.
See Figure 19, Page 20.
Figure 20 - Troubleshooting Pilot Flame
• Recheck ignition sequence as follows.
— Reconnect main valve wire.
— Adjust thermostat above room temperature.
— Verify ignition sequence at burner.
— If spark does not stop after pilot lights, replace
module.
P/N
240009041
, Rev. C [04/30/2017]