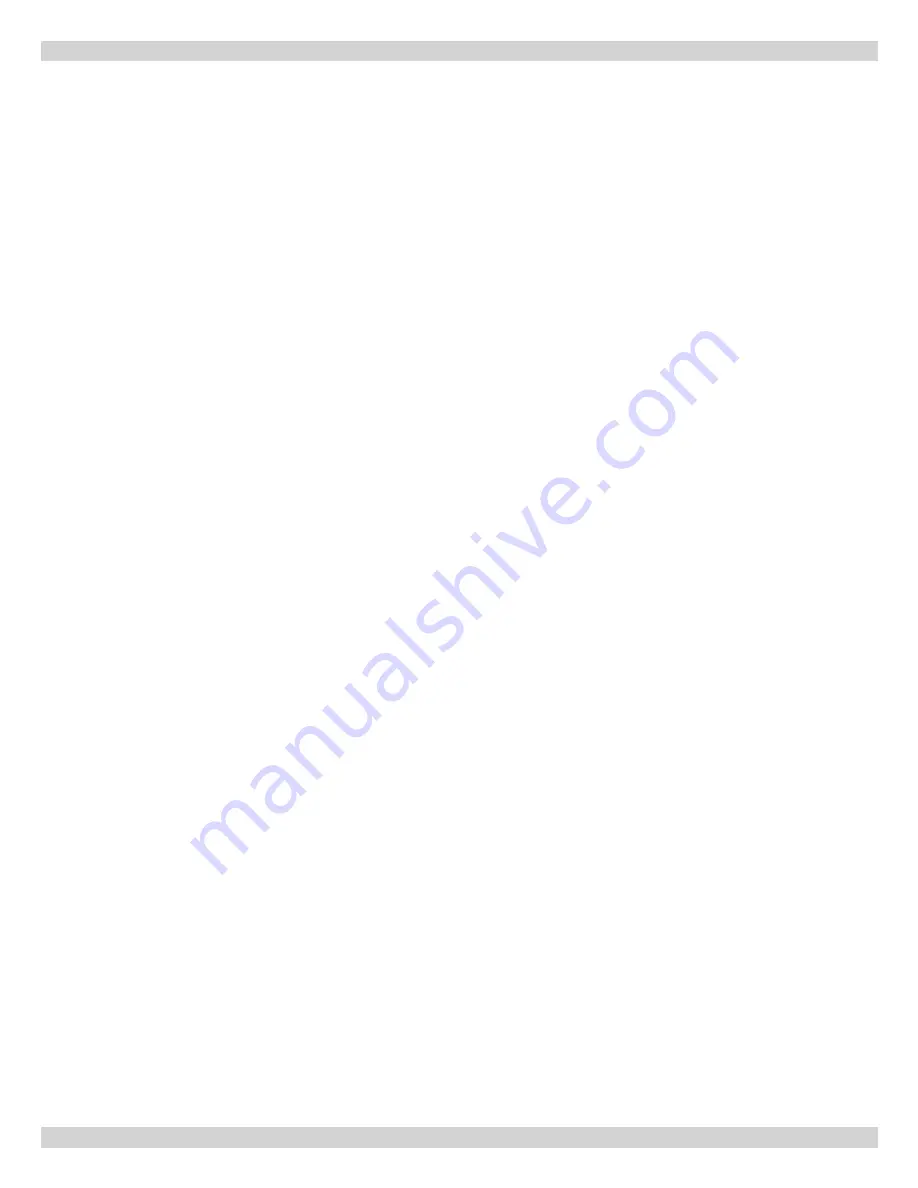
9
In the event that the side wall horizontally vented gas
A.
fueled equipment is installed in a crawl space or an attic,
the hard wired carbon monoxide detector with alarm and
battery back-up may be installed on the next adjacent floor
level.
In the event that the requirements of this subdivision can
B.
not be met at the time of completion of installation, the
owner shall have a period of thirty (30) days to comply
with the above requirements; provided, however, that dur-
ing said thirty (30) day period, a battery operated carbon
monoxide detector with an alarm shall be installed.
Approved carbon monoxide detectors: each carbon monoxide
2.
detector as required in accordance with the above provisions
shall comply with NFPA720 and be ANSI/UL 2034 listed and
IAS certified.
Signage: a metal or plastic identification plate shall be perma-
3.
nently mounted to the exterior of the building at a minimum
height of eight (8) feet above grade directly in line with the
exhaust vent terminal for the horizontally vented gas fueled
heating appliance or equipment. The sign shall read, in print
size no less than one-half (1/2) inch in size, “gas vent directly
below. Keep clear of all obstructions”.
Inspection: the state or local gas inspector of the side wall
4.
horizontally vented gas fueled equipment shall not approve
the installation unless, upon inspection, the inspector observes
carbon monoxide detectors and signage installed in accordance
with the provisions of 248 CMR 5.08(2)(A)1 through 4.
Product-approved vent/air-intake: a product-approved vent ter-
5.
minal must be used and, if applicable, a product-approved air
intake must be used. Installation shall be in strict compliance
with the manufacturer’s instructions.
Installation instructions: a copy of all installation instructions
6.
for all product approved side wall horizontally vented gas fueled
equipment, all venting instructions, all parts lists for venting
instructions, and/or all venting design instructions shall remain
with the appliance or equipment at the completion of the instal-
lation.
boiler sizing
Check to be sure you have selected the boiler with the proper capac-
ity before starting the installation. The I=B=R Rating of the boiler
selected should be greater than or equal to the calculated peak heat-
ing load (heat loss) for the building or area(s) served by the boiler
and associated hot water heating systems. See the table “BOILER
RATINGS AND CAPACITIES” (page 5 of this document).
Heat loss calculations should be based on approved industry meth-
ods.
Considerations for boiler location
Before selecting a location for the boiler, the following should be
considered. Each boiler considered.
Supplied with the correct type of gas (natural gas or pro-
•
pane).
Connected to a suitable combustion air intake piping sys-
•
tem to supply the correct amounts of fresh (outdoor) air
for combustion, refer to Combustion Air And Vent Pipe
section (near center of this manual) for details.
Connected to a suitable venting system to remove the
•
hazardous products of gas combustion, refer to Combus-
tion Air And Vent Pipe section (page 19 of this manual) for
details.
Connected to a suitable hot water heating system.
•
Supplied with a suitable electrical supply for all boiler mo-
•
tors and controls.
Connected to a properly located thermostat or operating
•
control. (not included with boiler)
Placed on level surface (must NOT be installed on carpet-
•
ing)
Condensate drain line must be pitched down to floor drain
•
or external condensate pump with reservoir at ¼” per foot
(wood frame or blocks may be used to raise boiler).
locating The boiler
Select a location which is level, central to the piping systems
1.
served and as close to the vent and air intake terminals as pos-
sible.
Accessibility clearances, if more stringent (i.e. larger clearances)
2.
than required fire protection clearances, must be used for the
boiler installation. Accessibility clearances may be achieved
with the use of removable walls or partitions.
The boiler is approved for installation in closets and on com-
3.
bustible floors. This boiler shall NOT be installed on carpeting.
The clearances shown in
4.
Table #2
indicate required clearances.
A minimum 1” clearance must be maintained between com-
bustible construction and each of the left, top and back surfaces
of the boiler. A minimum 8” clearance is required on the right
side, to allow room for the inlet air pipe. An 18” clearance must
be maintained at a side where passage is required to access an-
other side for cleaning or servicing, inspection or replacement
of any parts that normally may require such attention. Allow at
least 24” at the front and left side and 8” at the top for servicing.
No clearances are required to venting or combustion air intake
piping.
Equipment shall be installed in a location which facilitates the
5.
operation of venting and combustion air intake piping systems
as described in this manual.
before insTalling THe boiler
Summary of Contents for 90-100
Page 13: ...13 Figure 3 Multi zone Boiler Piping With Zone Valves Near Boiler Piping...
Page 16: ...16 Figure 6 Diaphragm Type Expansion Tank Piping Near Boiler Piping...
Page 17: ...17 Figure 7 Conventional closed type Expansion Tank Piping Near Boiler Piping...
Page 23: ...23 Figure 11 Combustion Air and Vent Piping Combustion Air and Vent Pipe...
Page 27: ...27 Figure 13 Field Wiring Connections Electrical Wiring...
Page 44: ...44 Service Hints Detailed Sequence Of Operation...
Page 50: ...50 TROUBLESHOOTING CHART 2 Troubleshooting...
Page 53: ...53 TROUBLESHOOTING CHART 5 Troubleshooting...
Page 56: ...85 Middle Rd Dunkirk NY 14048...