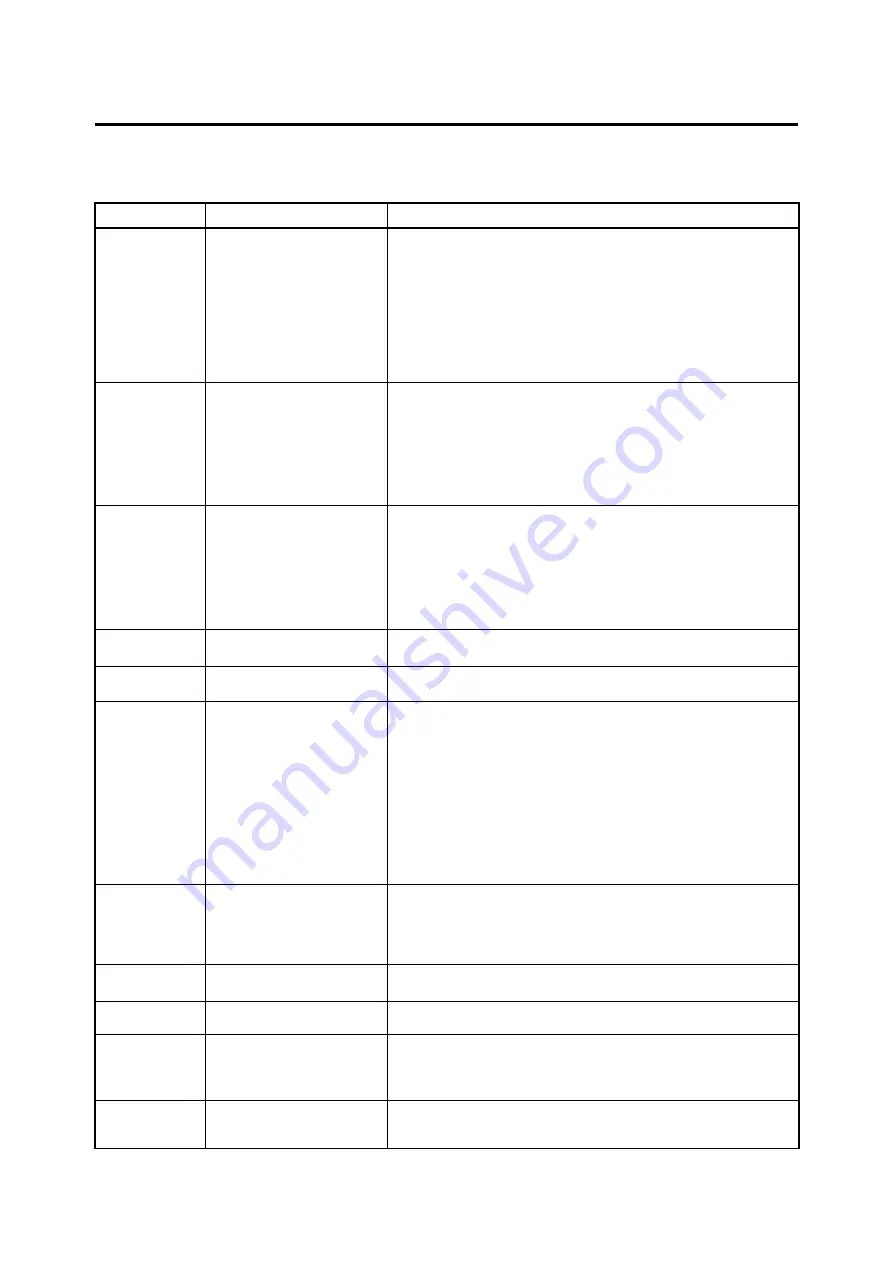
5
.
0 MAINTENANCE
5.7 TROUBLESHOOTING
SYMPTOM
POSSIBLE CAUSE
REMEDY
1. Unit will not
start.
a.) Power off.
b.) No control power.
c.) Compressor circuit
breakers open.
d.) Phase control relay open.
e.) Flow Switch open.
f.) Compressor switch open.
g.) Microcomputer shutdown
not reset.
a.) Check main disconnect switch and main line fuses.
b.) Check control transformer fusing.
c.) Close circuit breakers. If trip, check compressor.
d.) Check for power supply problems (low voltage, phase imbalance).
When corrected, press reset button.
e.) Start pumps, check flow switch.
f.) Turn switch on. Check alarm status. Correct problem.
g.) Press reset button.
2. Compressor
hums but
does not
start.
a.) Low voltage.
b.) No power on one phase
of 3 phase unit.
c.) Faulty starter or
contactor.
a.) Check at main entrance and at unit. Consult power company if
voltage is low and increase wire size to the unit if voltage is normal
at main and low at unit. Voltage must be within 10% of motor
name plate rating.
b.) Check fuses and wiring.
c.) Check the contacts and time delay on part wind start.
3. Compressor
will not start
when reset
button is
pushed.
Check light:
None
a.) Cooling not required.
b.) Computer's time delay
active.
c.) Phase control relay open.
d.) Flow switch open.
e.) Compressor switch open.
f.) Burned out signal light.
g.) Wiring problem
a.) Apply load.
b.) Wait 15 minutes max.
c.) See 1.( d.) above.
d.) See 1.( e.) above.
e.) See 1.( f.) above.
f.) Check signal light bulbs.
g.) Check wiring against drawing.
4. Compressor
overload.
a.) Compressor drawing high
amps.
a.) Check motor megohms. Reset overloads; run compressor an
check amps. Do not exceed RLA x 1.25. Call D/B serviceman.
5. High
oil
temperature
a.) Motor windings failing.
b.) Insufficient motor cooling.
a.) Check megohms.
b.) Open liquid injection valve slightly.
6. Low
suction
pressure
a.) Inadequate feed to
evaporator.
b.) Inadequate refrigerant
charge.
c.) Fouling of waterside of
evaporator.
d.) Inadequate chilled water
flow.
e.) Too much oil in system.
a.) Check to see that liquid line ball valve is open.
b.) See information on charging in Section 5.6.
c.) At high load, check evaporator approach (See Section 5.4). If
approach is more than 2°F [1.1°C] above clean valve, fouling is
probably the trouble. Clean tube.
d.) Measure pressure drop across vessel and determine flow rate
from Figure 2.3. If flow rate is low, check chilled water pump,
valves and strainers.
e.) If all oil level sight glasses are full at all times, remove oil until oil
level shows at top of glass on a compressor.
7. High
discharge
pressure.
a.) Inadequate air flow
across condenser
b.) Fouling of waterside of
condenser.
a.) Check condenser flow rate, either with condenser pressure drop
curve or with pump curve.
b.) At high load, check difference between saturated refrigerant temp.
and leaving water temp. If 2°F [1.1°C] or more above start-up
conditions, remove headers and clean tubes.
8. Oil low in
sump.
a.) Low oil level in
compressor.
a.) Low oil level in compressor sight glass is acceptable.
9. Low
oil
shutdown.
a.) Low oil in compressor.
a.) See Section 5.6.2.
10. Freeze
warning.
a.) Operating setpoint too
low.
b.) Load changing too
rapidly.
a.) Check leaving water setpoint on microcomputer.
b.) Load on package must drop at reasonable rate for automatic
control to work properly.
11. Improper
capacity
control.
a.) Ramp rate incorrect.
a.) See Section 4.4.6.6.
- 63 -
Summary of Contents for WCFX 10
Page 8: ...TWO PASS RIGHT HAND ARRANGEMENT SHOWN 1 0 GENERAL INFORMATION WCFX 20 22 24 27 30 33 36 8...
Page 9: ...1 0 GENERAL INFORMATION WCFX 39 42 45 48 51 54 9...
Page 31: ...3 0 OPERATION FIGURE 3 5 PIPING SCHEMATIC 1 1 COMPRESSOR WCFX 10 12 15 18 31...
Page 32: ...3 0 OPERATION 2 2 COMPRESSORS WCFX 20 22 24 27 30 36 32...
Page 33: ...3 0 OPERATION 3 3 COMPRESSORS WCFX 39 42 45 48 51 54 33...
Page 36: ...4 0 ELECTRICAL FIGURE 4 2 TYPICAL WIRING SCHEMATIC A 1 COMPRESSOR 36...
Page 37: ...4 0 ELECTRICAL 37...
Page 38: ...4 0 ELECTRICAL B 2 COMPRESSORS 38...
Page 39: ...4 0 ELECTRICAL 39...
Page 40: ...4 0 ELECTRICAL 40...
Page 41: ...4 0 ELECTRICAL C 3 COMPRESSORS 41...
Page 42: ...4 0 ELECTRICAL 42...
Page 43: ...4 0 ELECTRICAL 43...
Page 44: ...4 0 ELECTRICAL 44...