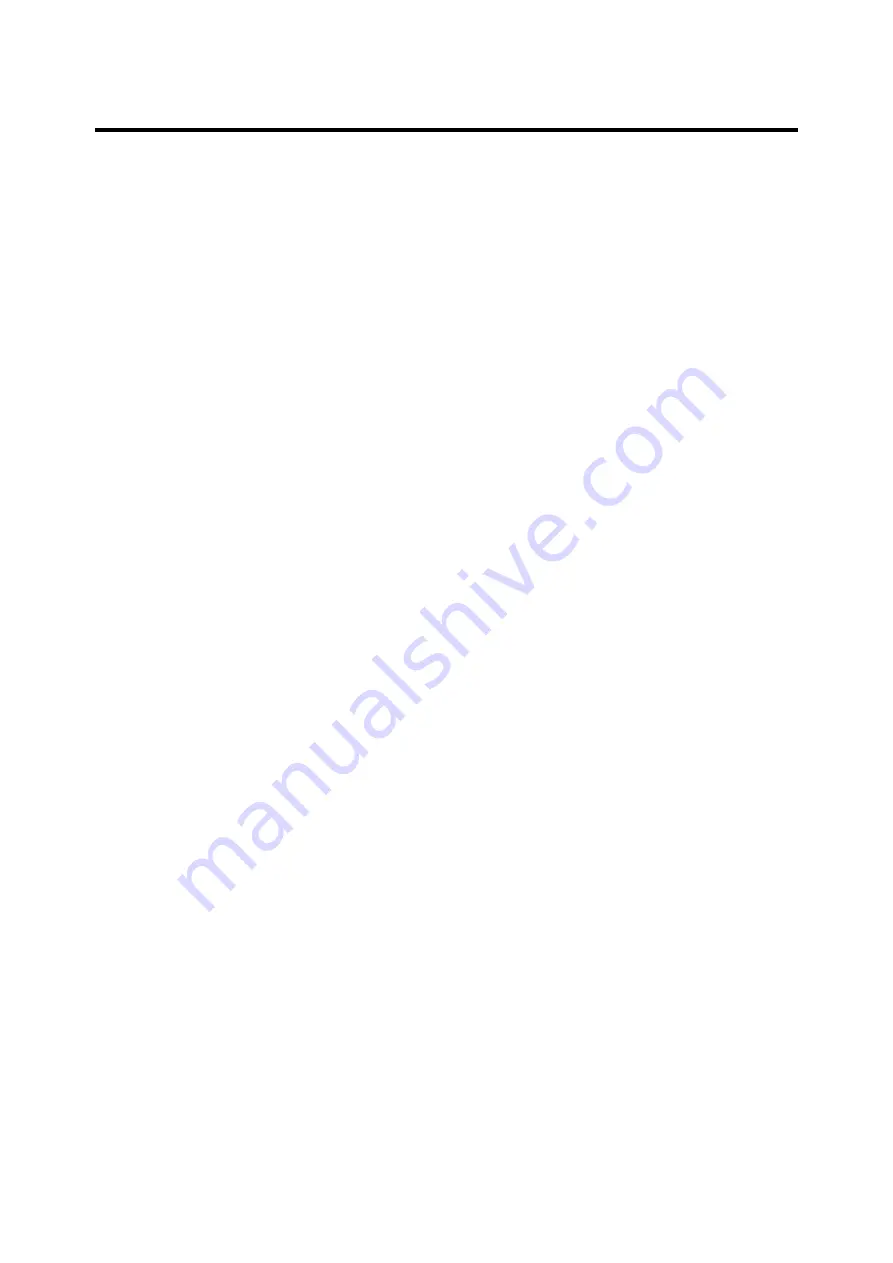
4
.
0 ELECTRICAL
4.6.2 Sequence Of Operation
1.
When the customer enable input is ‘on’ to
start the lead unit, the chilled water pump
starter or motorized valve control point will
close and water will start to flow through the
evaporator, this will activate the flow switch.
The flow switch and water pump status are
interlocked and feedback as digital input to
the chiller and upon receipt of a valid 'on'
signal, the lead chiller will begin to execute
its running program.
2.
The controller will start and load the
compressor(s), upon achieving full load; it
will send an output signal via the DBLAN to
enable second unit (lag 1)
3.
The second unit will now command its chilled
water pump to start if the customer unit
enable is activated. The second chiller will
start and load the compressor(s) until it
reaches full load
4.
When the second chiller or lag 1 unit reaches
full load, it will enable the third chiller.
5.
The chiller will keep cascading until all
chillers on duty are at full load.
6.
If the leaving water temperature falls below
setpoint, all of the chillers will begin to
unload evenly.
7.
If the load drops below 45% total capacity,
delay the last unit (lag 3) will be disabled, and
the remaining three units will load up to
compensate if necessary. The pump for chiller
4 will be shut off.
8.
As the load demand falls, the lag 2 unit will
be disabled below 45% total capacity, and so
on until the load falls enough to shut off the
lead chiller.
9.
Each unit in the network can monitor the
operation of other units via DBLAN. If the
master unit is having critical alarm, the lag 1
will take over as the master unit automatically.
10.
In order to enable next unit, the following
conditions must met
a)
LWT
≥
(LWT Se Enable Next
deadband)
b)
After a enable next time delay of 3
minutes (adjustable) and
c)
When the lead unit’s packaged capacity is
higher than “Next on setpoint”,
for example, WCFX2, %Capacity C1 &
%Capacity C2
≥
Next on setpoint
or it is being lockout by an alarm.
4.7
VISION 2020i LOCAL
AREA NETWORK
(DBLAN)
A DBLAN network is made up of several
chillers’ controller. Each unit’s controller can be
programmed and connected to the local DBLAN
network that allows multiple units sequencing
control without additional hardware.
Every DBLAN node must be addressed to be
identified by the other nodes. Each address (an
integer number) must be unique in the network
for avoiding messages mismatch: in case two or
more nodes have the same identifying address the
network cannot work.
The max address number selectable is in the 1-16
for the Vision 2020i controller boards and 17-32
range for the Vision 2020i DBG1 User terminal.
The three chiller unit combinations:
Controller with address of 1 connect to Terminal
with address of 17
Controller with address of 2 connect to Terminal
with address of 18
Controller with address of 3 connect to Terminal
with address of 19
Follow the following steps:
- 56 -
Summary of Contents for WCFX 10
Page 8: ...TWO PASS RIGHT HAND ARRANGEMENT SHOWN 1 0 GENERAL INFORMATION WCFX 20 22 24 27 30 33 36 8...
Page 9: ...1 0 GENERAL INFORMATION WCFX 39 42 45 48 51 54 9...
Page 31: ...3 0 OPERATION FIGURE 3 5 PIPING SCHEMATIC 1 1 COMPRESSOR WCFX 10 12 15 18 31...
Page 32: ...3 0 OPERATION 2 2 COMPRESSORS WCFX 20 22 24 27 30 36 32...
Page 33: ...3 0 OPERATION 3 3 COMPRESSORS WCFX 39 42 45 48 51 54 33...
Page 36: ...4 0 ELECTRICAL FIGURE 4 2 TYPICAL WIRING SCHEMATIC A 1 COMPRESSOR 36...
Page 37: ...4 0 ELECTRICAL 37...
Page 38: ...4 0 ELECTRICAL B 2 COMPRESSORS 38...
Page 39: ...4 0 ELECTRICAL 39...
Page 40: ...4 0 ELECTRICAL 40...
Page 41: ...4 0 ELECTRICAL C 3 COMPRESSORS 41...
Page 42: ...4 0 ELECTRICAL 42...
Page 43: ...4 0 ELECTRICAL 43...
Page 44: ...4 0 ELECTRICAL 44...