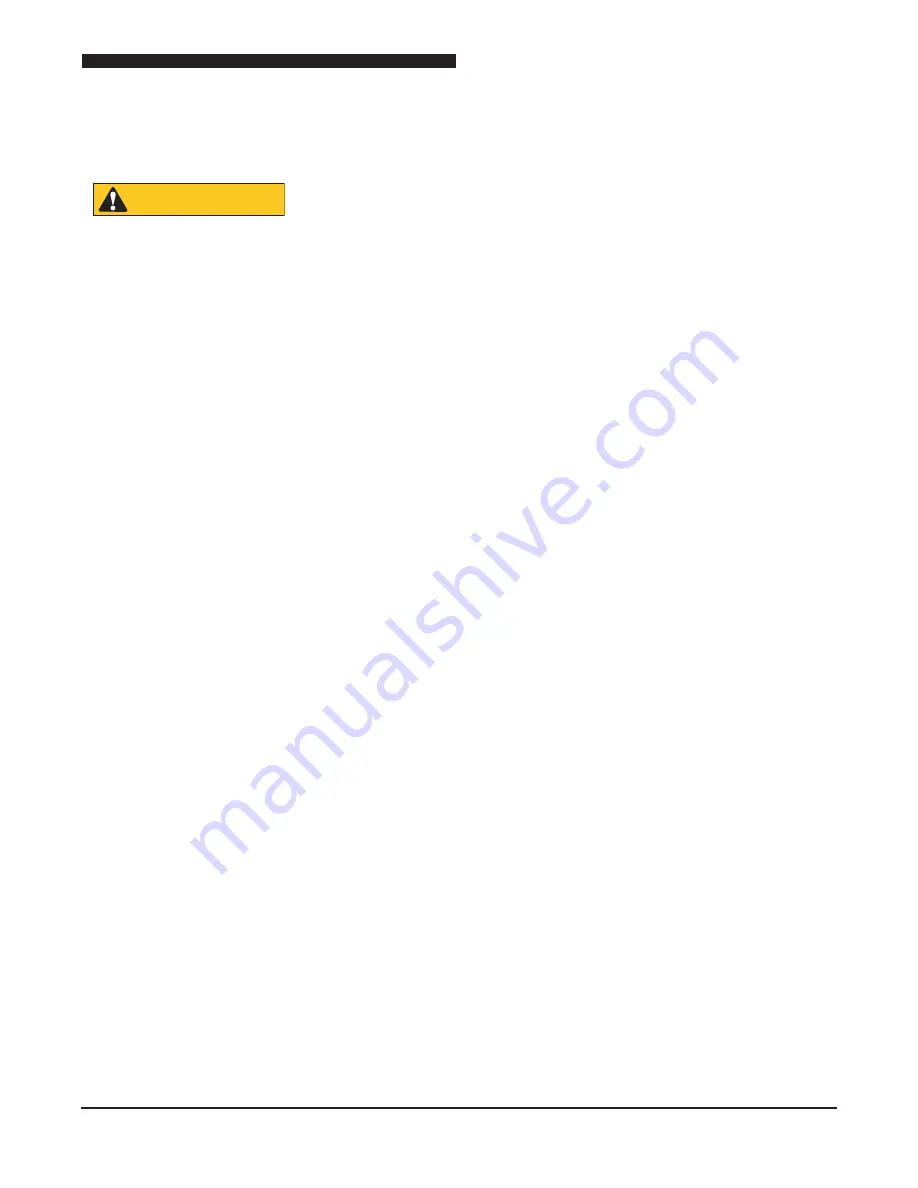
7
Installation and Operation of Flexible Batch Broiler
With Touch Screen Control
WARNING
IMPROPER INSTALLATION,
ADJUSTMENT, ALTERATION,
SERVICE, OR MAINTENANCE CAN
CAUSE PROPERTY DAMAGE,
INJURY, OR DEATH. READ THE
INSTALLATION, OPERATING, AND
MAINTENANCE INSTRUCTIONS
BEFORE INSTALLING OR
SERVICING THIS EQUIPMENT.
Installation and/or service repair of gas
appliances requires Skilled or Qualified
Personnel. Skilled or Qualified Personnel are
individuals, firms, companies or corporations
which are directly authorized by Duke
Manufacturing (Assignee) or meet the
requirements of governmental authority having
jurisdiction for the task.
Electrical wiring tasks must be in conformance
with National Electrical Code ANSI/NFPA70
Gas supply interconnection must be in
conformance with National Fuel Gas Code
ANSI Z223.1/NFPA54 and Natural Gas and
Propane Installation Code CSAB149 including
the following:
• The appliance must have an individual manual
shutoff valve at the connection to the gas supply
piping system during any pressure testing of
that system at test pressures in excess of ½ psi
(3.5kPa).
• The appliance must be isolated from the gas
supply piping system by closing its individual
manual shut off valve during any pressure
testing of the gas supply systems at test
pressures equal to or less than ½ psi (3.5kPa).
For a broiler mounted on casters, the
installation must be made with a connector
that complies with ANSI Z21.69 / CSA 6.16
Connectors for Moveable Gas Appliances
and a quick-disconnect device that complies
with ANSI Z21.4 / CSA 6.9 Quick –Disconnect
Devices for Use with Gas Fuel.
When installing a broiler mounted on casters
with quick-disconnect hose, adequate means
must be provided to limit the movement of the
broiler without depending on the connector,
hose, or system piping to limit movement. A
restraining device may be attached to the rear
vertical portion of the broiler’s base frame.
A. VENTILATION:
This appliance requires a ventilation system
to prevent unacceptable concentrations of
substances harmful to health in the room where
the appliance is installed.
Ventilation System Specifications:
Must be a Mechanically Driven Exhaust Hood
System
Minimum Capacity: 1,700 m3/hr (1,000 cfm)
Minimum Opening: 39.4” x 51.2” (100cm x
130cm)
The Ventilation System must be inspected,
maintained, and annually serviced by
Qualified Personnel as part of or in addition to
governmental requirements
NOTE: Ventilation Systems for multiple or
additional appliances must have capacity
in addition to the specifications for this
appliance.
II. INSTALLATION INSTRUCTIONS
The installation must conform with local codes, or in the absence of local codes, with the National Fuel Gas Code,