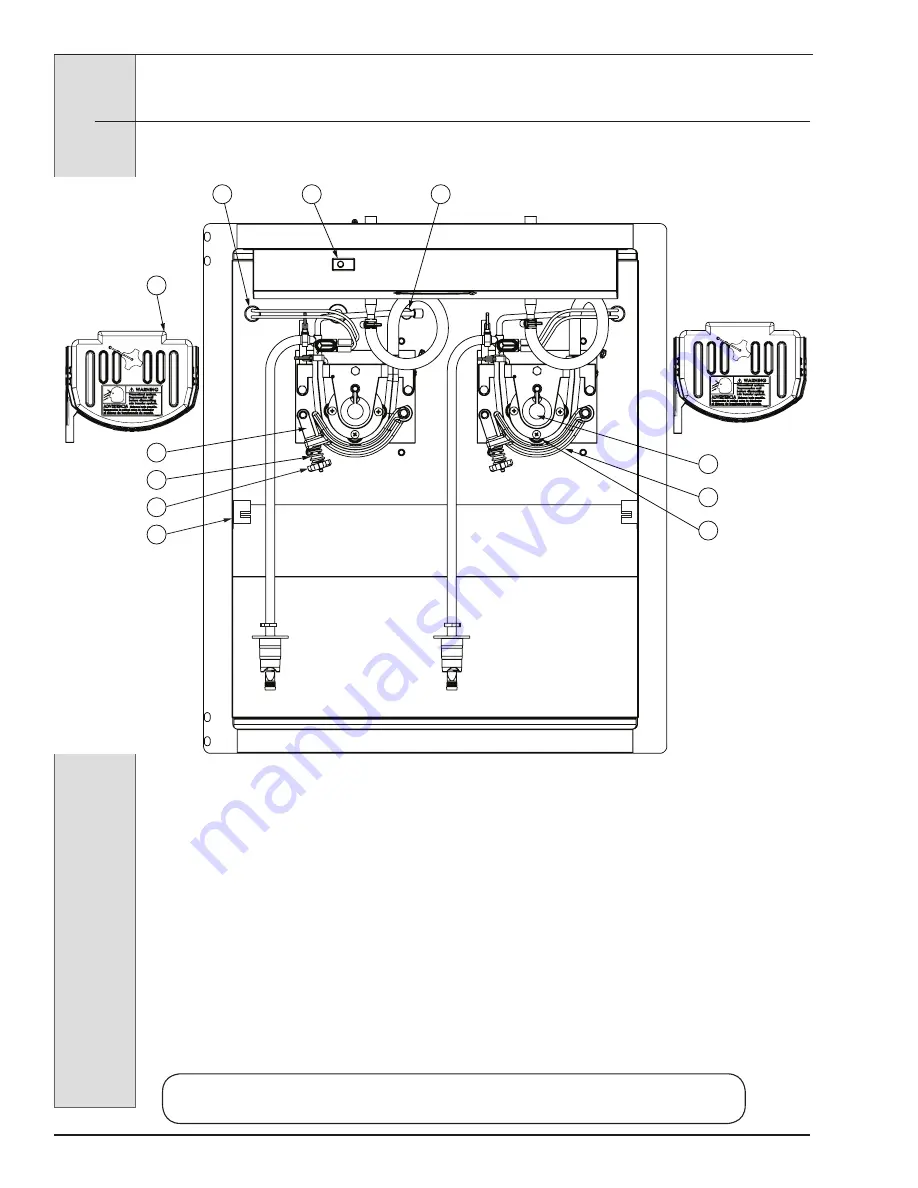
185232
8
Soft Serve Freezer Model GEN-102
Use only original or authorized replacement parts with this freezer.
Use of unapproved parts will void warranty.
Item Part No.
Description
1
2
3
4
5
6
7
8
9
10
11
Item
Part No.
Description
1 ..................HC161313 .............Switch - Proximity Reed NC
2 ..................HC140706 .............Knob - Fluted 1/4-20 Custom
3 ..................HC1623
30
.............Spring - Compression
3 ..................HC140711 .............Washer - Spring End
4 ..................HC138799 .............Arm - Swing Clamp
5 ..................HC121798 .............Cover - Assy Mix Pump Molded
6 ..................HC150536 .............Receptacle
7 ..................HC150612 .............Switch
8 ..................HC117092 .............Retainer - Air Line
9 ..................HC138783-01 ........Support - Roller Bearing
10 ................HC139751 .............Shoe - Roller
11 .................HC116009-01 ........Roller - Assy Complete
Figure 6 Cabinet Parts
Summary of Contents for DQ GEN-102
Page 2: ......
Page 10: ......
Page 20: ...185232 10 Soft Serve Freezer Model GEN 102 5 Part Names and Functions Figure 5 1 Head Assembly...
Page 82: ......
Page 84: ......
Page 100: ...185232 16 Soft Serve Freezer Model GEN 102 Figure 12 Side Rear View WC...
Page 105: ...185232 21 Soft Serve Freezer Model GEN 102 O Ring Chart...