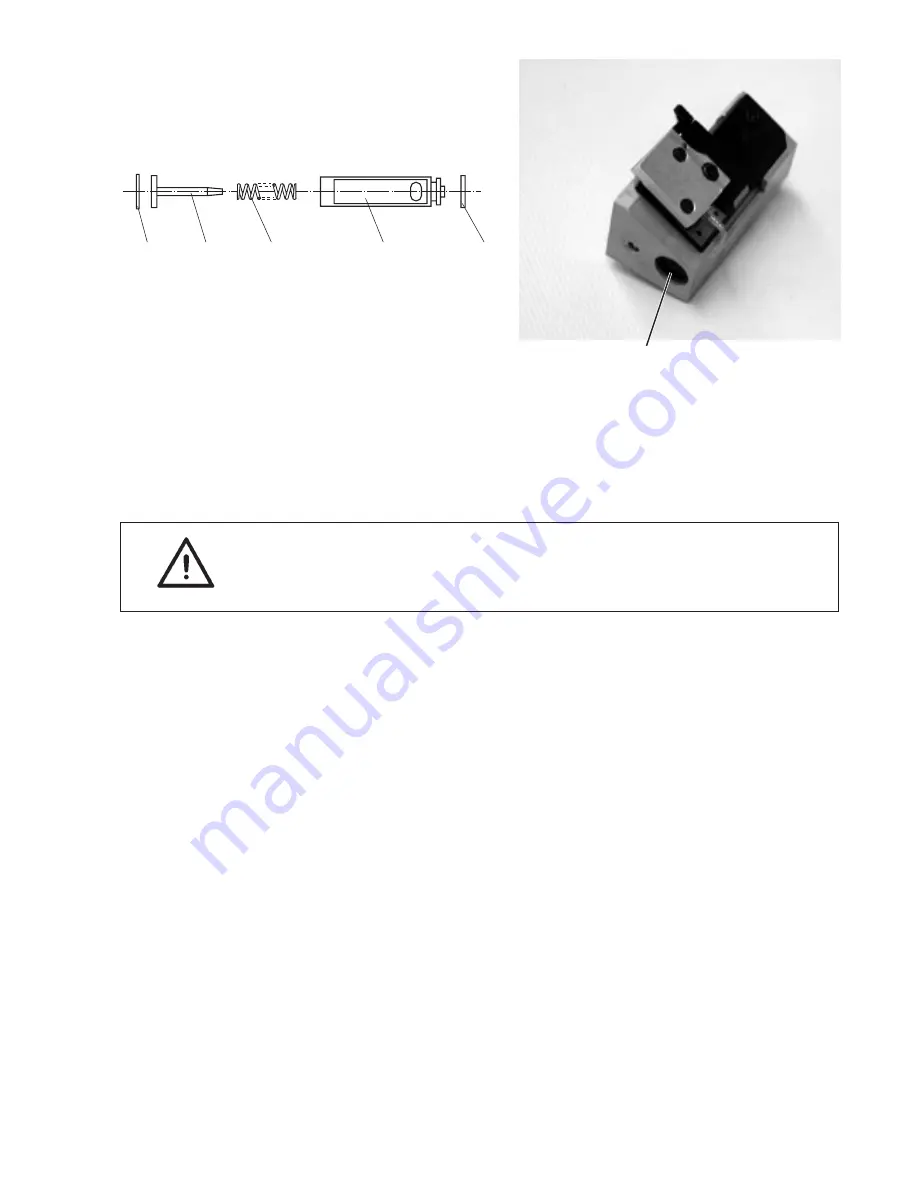
Replacement of piston
The movable blade is lifted pneumatically.
The piston operating the blade is installed in the body part of the
scissors.
CAUTION!
The thread surface of the hole is anodised.
When replacing the piston, ensure that the anodised layer is not
damaged!
–
Remove circlip 20.
CAUTION!
Pin 21 is under pressure!
–
Remove pin 21, pressure spring 22 and piston 23 with O-ring 24.
–
Lubricate thread surface of the hole with ESSO fluid grease S420.
(DÜRKOPP ADLER AG order no.: 791 000304)
–
To install piston, proceed in reverse order.
–
Complete test cut with sewing thread (test programme).
3-
17
20
21
22
23
24
20