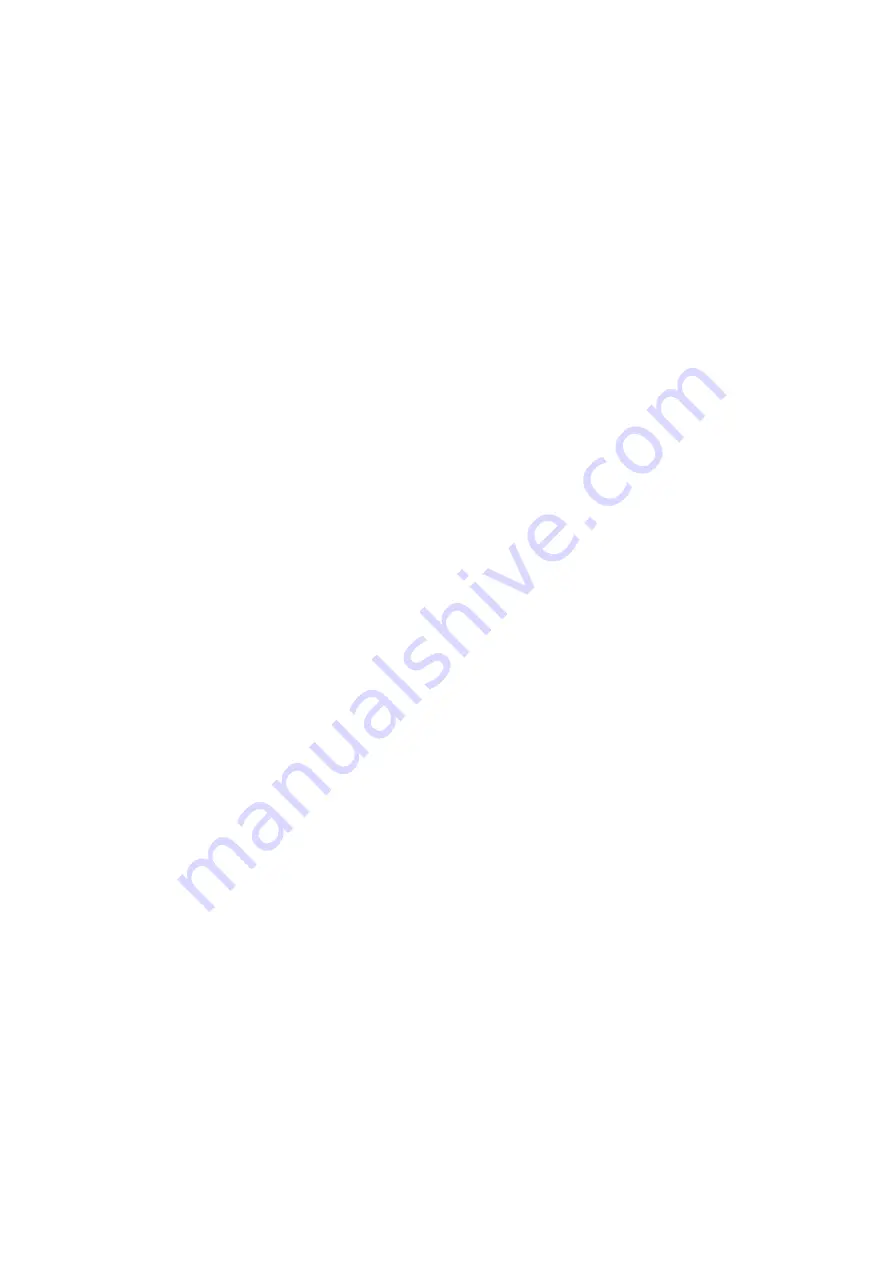
3.12
Driving toothed belt
............................................................................................................................................................... 17
3.12.1
To exchange the driving toothed belt
3.13
Lubrication
.............................................................................................................................................................................. 18
3.13.1
Description
3.13.2
Refilling oil
3.13.3
Multiple oil use
4.
Thread trimming
................................................................................................................................................................................. 19
4.1
Description of the trimming mechanism
4.2
Setting the pickup roller
4.3
Setting the cam
4.4
Setting the fork
4.5
Setting the moving knife
4.6
Setting the fixed knife
4.7
Setting the retaining spring of the hook thread
4.8 Position of the lower thread - lefthand side
4.9
Setting switching of the electromagnets
5.
Lifting the presser foot by electromagnet
.................................................................................................................................. 22
5.1
Description
5.2
Setting the electromagnet pin
5.3
Setting the electromagnet current
5.4
Assembly of the top roller lifting electromagnet
6.
Backtacking using electromagnet
.................................................................................................................................................. 22
6.1
Description
6.2
Electromagnet height setting
6.3
Setting the position of push-buttons
6.4
Change of the function of push-buttons
7.
Connecting the electric elements on the machine head
......................................................................................................... 23
8.
Drive, control panel, position sensor
........................................................................................................................................ 23
9.
Maintenance (table of operations)
............................................................................................................................................... 24
10.
Setting the machine according to the sewing category
............................................................................................................ 24
10.1
Introduction
10.2
Table of setting the machine according to the sewing category
All manuals and user guides at all-guides.com