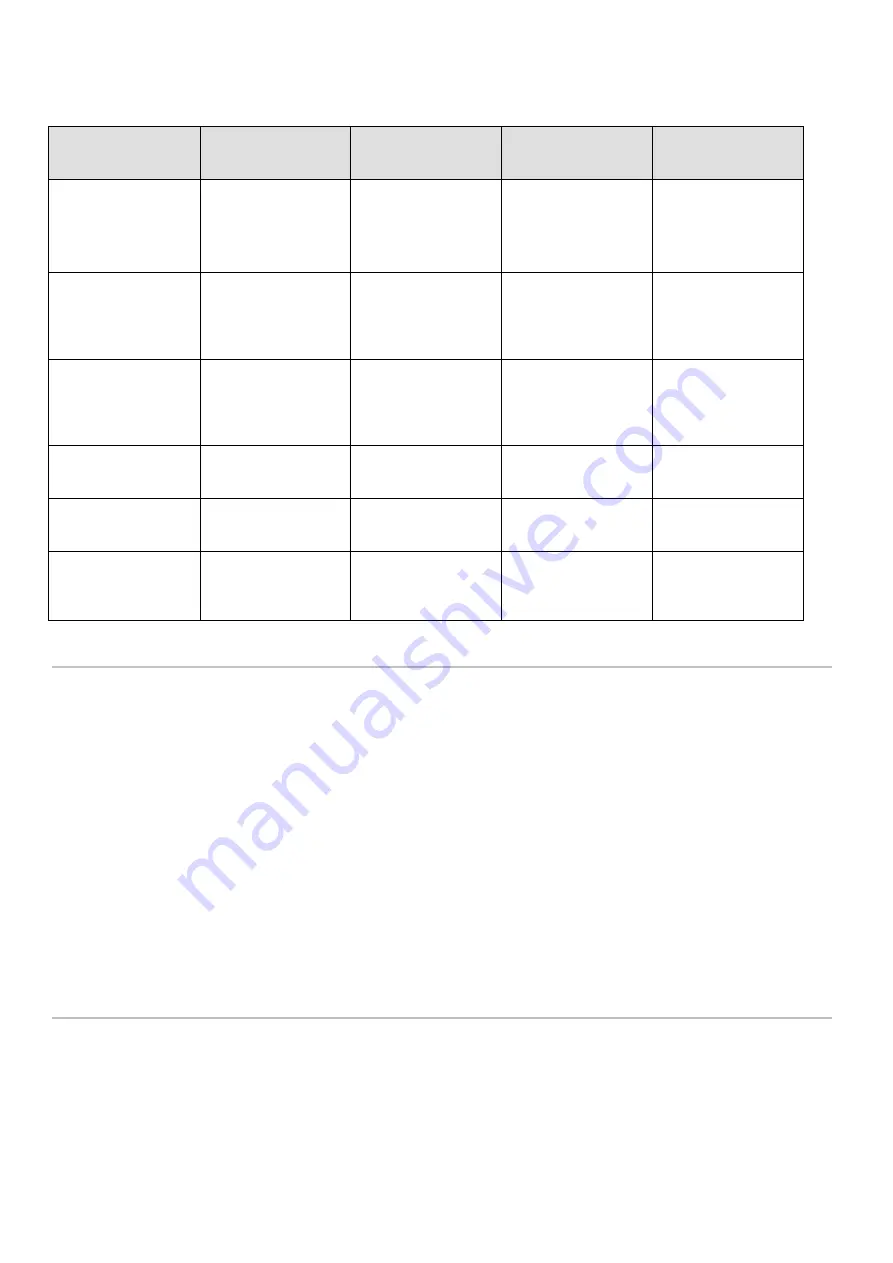
8
7.6
APPROXIMATE CONSUMPTION FOR LRT OILS (3226661) USAGE
Grams per lubrication nozzle in 8 hours operating time
ALUMINIUM
LEADED BRASS
LEADED STEEL
SOFT STEEL
ALLOY STEEL
STAINLESS STEEL
REFRACTORY
AND TITANIUM
ALLOYS
Saw cutting
Turning
Shearing
Cutting off
35-40
30
30
30-60
Boring
Drilling
Milling
Slotting
30-40
30
60
70
Threading
Tapping
Planing
Shaving
60
70
80
90
Threading blind
tapping
60
70
80
90-100
Moulding and
standard drawing
60
70
80-90
90-100
Broaching
Toothing
Bending
70
80
90
100/110
8. MAINTENANCE
The pump has been designed and constructed so as to reduce maintenance to a minimum.
To simplify maintenance it is recommended that the equipment be mounted in an easily reached location
(see paragraph 6.2)
.
Periodically check the tubing connections for leaks. Always maintain the equipment in a clean condition in
order that any leaks will be immediately evident.
When necessary replace the oil filling filter P/N 3130139.
Periodically empty the pressure regulator condensate trap by rotating the small red valve located at its
base.
The machine does not require any special tools for carrying out checks and/or maintenance tasks. It is
recommended that suitable tools and personal protection clothing (gloves) are used in accordance with
current regulation(Safety at Work legislation), and that they are in good condition (according to current
regulation) in order to avoid injury to persons and damage to the machine.
Ensure that electrical, pneumatic and hydraulic supplies are disconnected before undertaking any
maintenance tasks.
9. DISPOSAL
During the maintenance of the machine, or in the event of its being scrapped, do not discard polluting
components in the environment. Refer to local regulations for their correct disposal. At the time of final
disposal of the machine it is necessary to destroy the identification plate and all other documentation.