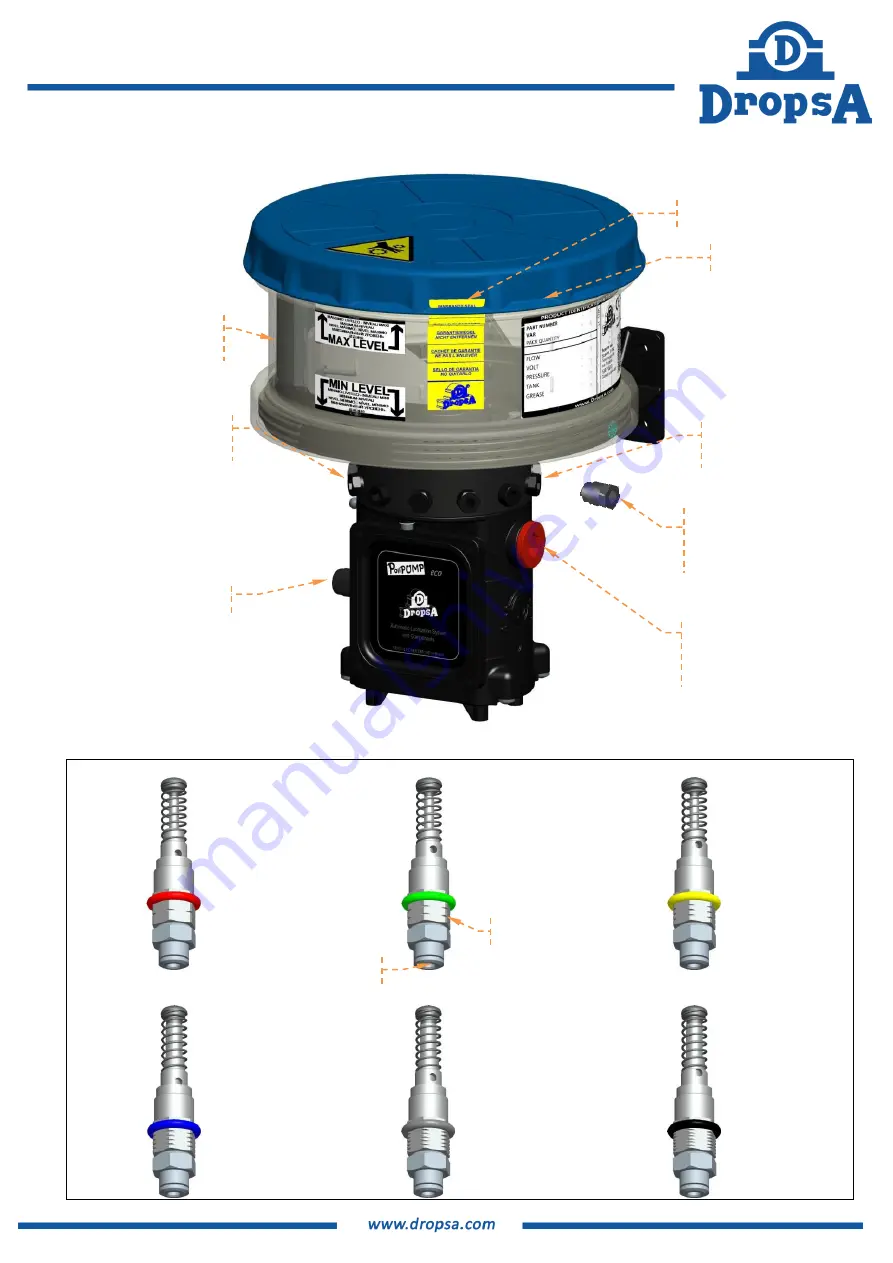
5
5. COMPONENTS
PoliPUMP (standard)
PUMPING ELEMENTS
RED - (1 notch)
0.02cc/cycle
GREEN - (2 notches)
0.03cc/cycle
YELLOW - (3 notches)
0.04cc/cycle
BLUE - (4 notches)
0.08cc/cycle
GREY - (5 notches)
0.10cc/cycle
BLACK - (6 notches)
0.13cc/cycle
Push-in outlet Ø4
Notches
Pump replacement cap
(included within the
scope of supply)
Stirring paddle with
wiper reservoir
Input power cable gland
Pumping element
housing holes/caps
Loading door to the
grease nipple
Cartridge loading
predisposition/eventual
return in pump M22x1.5
Reservoir, 2L
Warranty seal