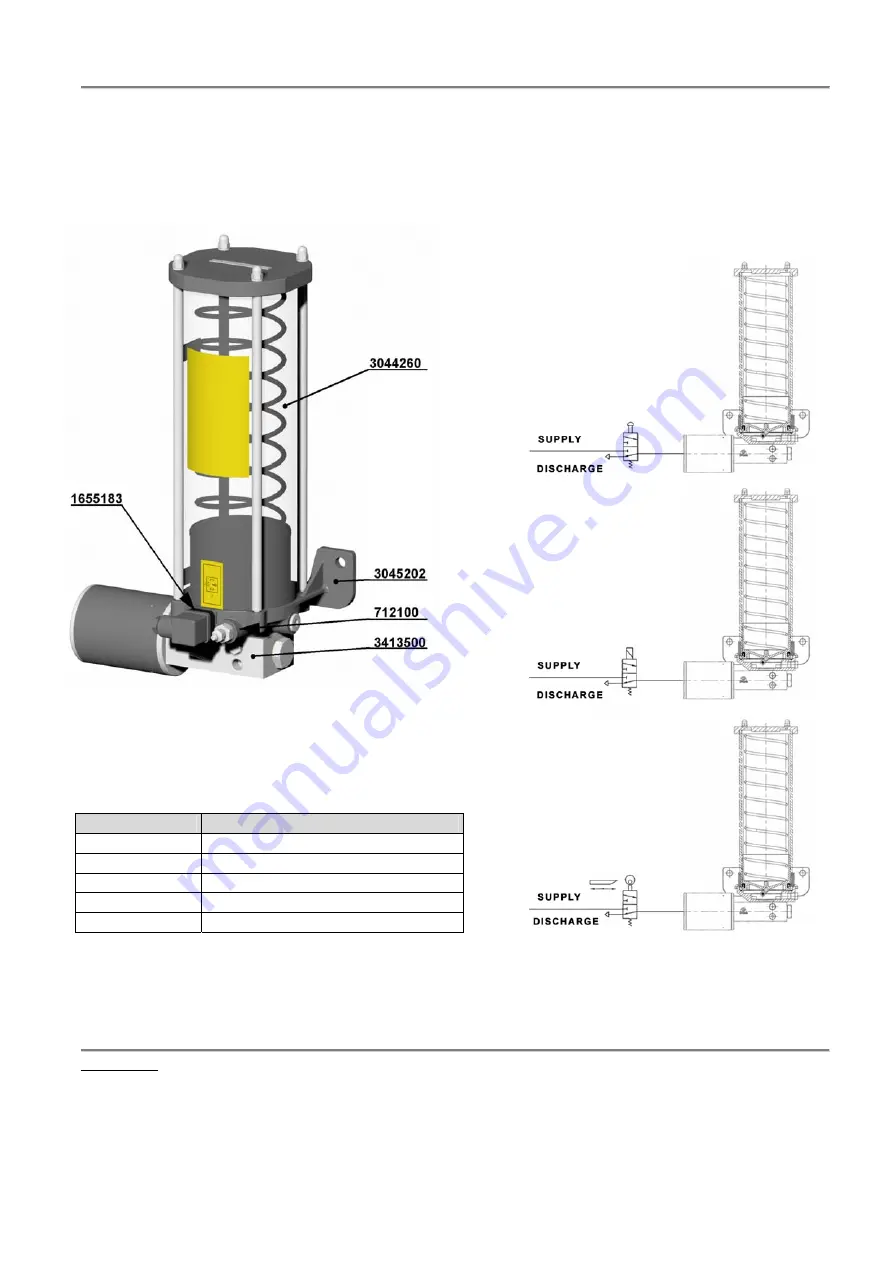
3
5. PUMP COMPONENTS
All the main pump components are fixed to the mounting bracket.
Oil Reservoir:
constructed in transparent plastic and compatible with commercial lubricants.
Pump Assembly:
constructed in steel and containing a non-return valve. At the working pressure of 300
bar (4410 Psi), the pump can deliver up to 2 cm³ (0.12 cu.in.) per stroke.
Electric Level Control-Switch:
Provides remote low level sensing. The switch can be set to either
operate normally open (N.O.) or normally close (N.C.). Standard configuration is N.C.
6. UNPACKING AND INSTALLING THE PUMP
WARNING:
The unit can only be opened and repaired by authorized Dropsa personnel.
6.1 UNPACKING
.
Once a suitable location has been found to install the unit remove the pump from the packaging. Check the
pump has not been damaged during transportation or storage. No particular disposal procedures are necessary
as packaging materials are no dangerous for health or environment. However, packaging should be disposed of
in accordance with regulations that may be in force in your area or state.
CODE
DESCRIPTION
3044260
Reservoir 2 Kg (4.4 lb.)
3045202 Mounting
bracket
3413500 Pump
body
1655183
Electric Level Control-Switch
712100 Re-filling
filter