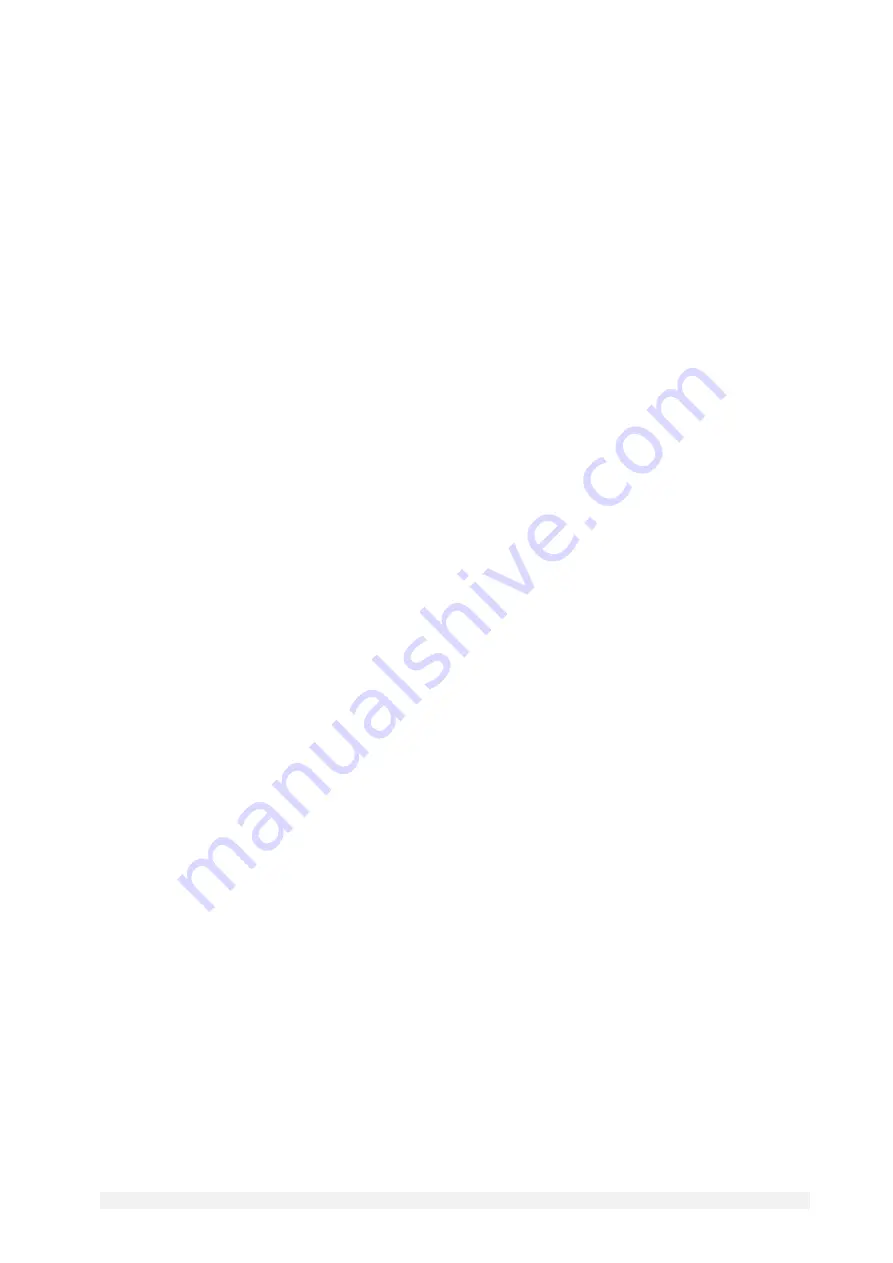
C20008IE – Pneumatically driven pump - Rev. 0 February 99 Page 6 of 9
Disassembly must be effected in the following manner:
1. disconnect the tubing attached to the pump.
2.
remove the fixing screws and remove the tank,
paying PARTICULAR ATTENTION to models containing a
grease pressure loading spring (it could be under pressure– in this case empty the remaining lubricant
first).
3. remove the pump and any filters.
4. unscrew the pneumatic cylinder of the pump
paying PARTICULAR ATTENTION
to the loading of the
spring; the component parts of the pump unit can then be disassembled.
In this way all component parts of the pump unit can be removed allowing the disassembly and cleaning of the
release and suction valves.
All pieces should be washed in petrol and lubricated prior to reassembly.
The following should be checked periodically:
VERIFY
WORK CYCLES
The state of lubrication
100
The oil level
200
The cleanliness of the suction filter
400
The cleanliness of the loading/return filter
400
That the tank is clean and the bottom free from
deposits
600
The machine does not require any special tools to carry out checks or maintenance tasks, However, it is
recommended that only tools suitable for the tasks and in good condition should be utilised (DPR 547/55) to avoid
injury to persons or damage to machine parts.
3.7
Repairs
The following diagnostic table indicates the main anomalies which may be encountered, the probable causes and
possible solutions.
The anomalies shown are:
•
the pump fails to deliver sufficient oil or no oil at all
•
the pump fails to deliver oil at the prescribed pressure
In case of doubts and/or problems which cannot be resolved do not attempt to disassemble parts of the machine but
contact the Engineering Department of DROPSA S.p.A.