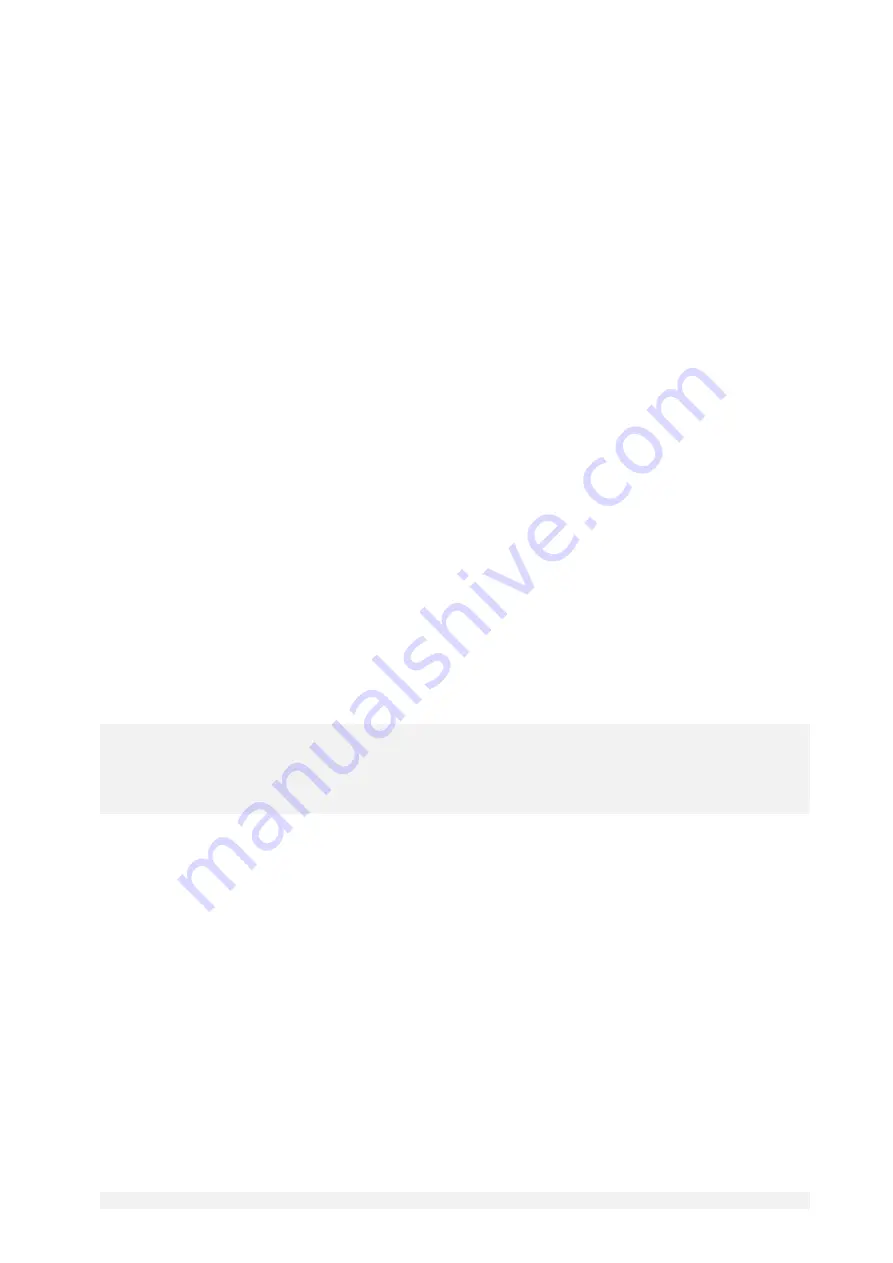
C20008IE – Pneumatically driven pump - Rev. 0 February 99 Page 2 of 9
0.0
INTRODUCTION AND WARNING
This user’s and maintenance manual refers to series
3413--- and 31040 pneumatically driven pumps,
for use in
mineral oil or grease lubrication systems.
It is recommended that this manual is carefully kept in good condition and is always available to persons requiring
to consult it.
To request further copies, updates or clarifications with respect to this manual contact the Engineering Department
at Dropsa SpA.
The use of the pump referred to in this manual must be entrusted to qualified personnel with a knowledge of
hydraulics, mechanical and electrical systems; the non-observance of the information given in this manual or the
improper use of the equipment by non-qualified or non-authorised personnel can put persons or the environment at
risk due to the escape of fluids under pressure.
It is of extreme importance that the instructions for use are read and understood both by the operators and
maintenance personnel, in cases of doubt please contact the area representative or our “Customer Service”
department.
The manufacturer reserves the right to update the product and/or the user’s manual without the obligation to revise
previous versions. It is however, possible to contact the Engineering Department for the latest revision in use.
It is the responsibility of the installer to utilise tubing suitable for the system; the use of unsuitable tubing can
generate problems with the pump, risks to persons and cause pollution.
The loosening of connections can cause serious safety problems and all such connections should be checked before
and after installation and tightened if necessary.
Never exceed the maximum operating pressure values allowed for the pump and the components to which it is
connected.
Before any maintenance or cleaning operations, close off the air supply and release the pressure from the pump and
the tubing to which it is connected.
Do not subject the pump, the tubing or other parts under pressure to violent impacts; damaged tubing or
connections are dangerous and should be replaced.
After prolonged periods of inactivity, ensure the tightness of all connections subjected to pressure.
It is required that personnel make use of protection devices, clothing and necessary tools, suitable to the place and
employment of the pump both while in operation and during the undertaking of maintenance tasks.
The pump, and any accessories mounted on it, should be carefully checked immediately on receipt and in the event
of any discrepancy or complaint the Dropsa SpA Sales Department should be contacted without delay.
DROPSA S.p.A. declines to accept any responsibility for injuries to persons or damage to property in the event of
the non-observance of the information presented in this manual.
Any modification to component parts of the system or the different destination of use of this system or its parts
without prior written authorisation from DROPSA S.p.A. will absolve the latter from any responsibility for injury or
damage to persons and/or property and will release them from all obligations arising from the guarantee.
The list of importers and instructions for ordering the required model are shown in Section 4.
1.0
DESCRIPTION OF THE PUMP
These pumps utilise compressed air to control the delivery of the lubricant and are ideal for lubrication systems
installed on machines already supplied with compressed air.
The solenoid control valve must be:
3 way (line-cylinder-discharge) for single action pumps
4 way (line-cylinder-discharges) for double action pumps
Deliverable lubricant
: mineral, not containing abrasive substances.
Compressed air supply pressure
: min. 4 bar (0.4 MPa) – max 8 bar (0.8 MPa)
Tank filling valve
: G 1/2 UNI-ISO 228/1 – only for pump 3413026 hydraulic connection
Lubricant outlet
: Rp 1/4 UNI-ISO 7/1
Compressed air inlet
:
for pump type 3413… G 1/8 UNI-ISO 228/1 fitting for 6 mm tube
for pump type 31040.. G 1/4 UNI-ISO 228/1 fitting for 8 mm tube
Filter for oil recovery (where fitted) in metal and/or paper.
Magnet type electrical minimum oil level indicator. Maximum operating temperature: +80 °C