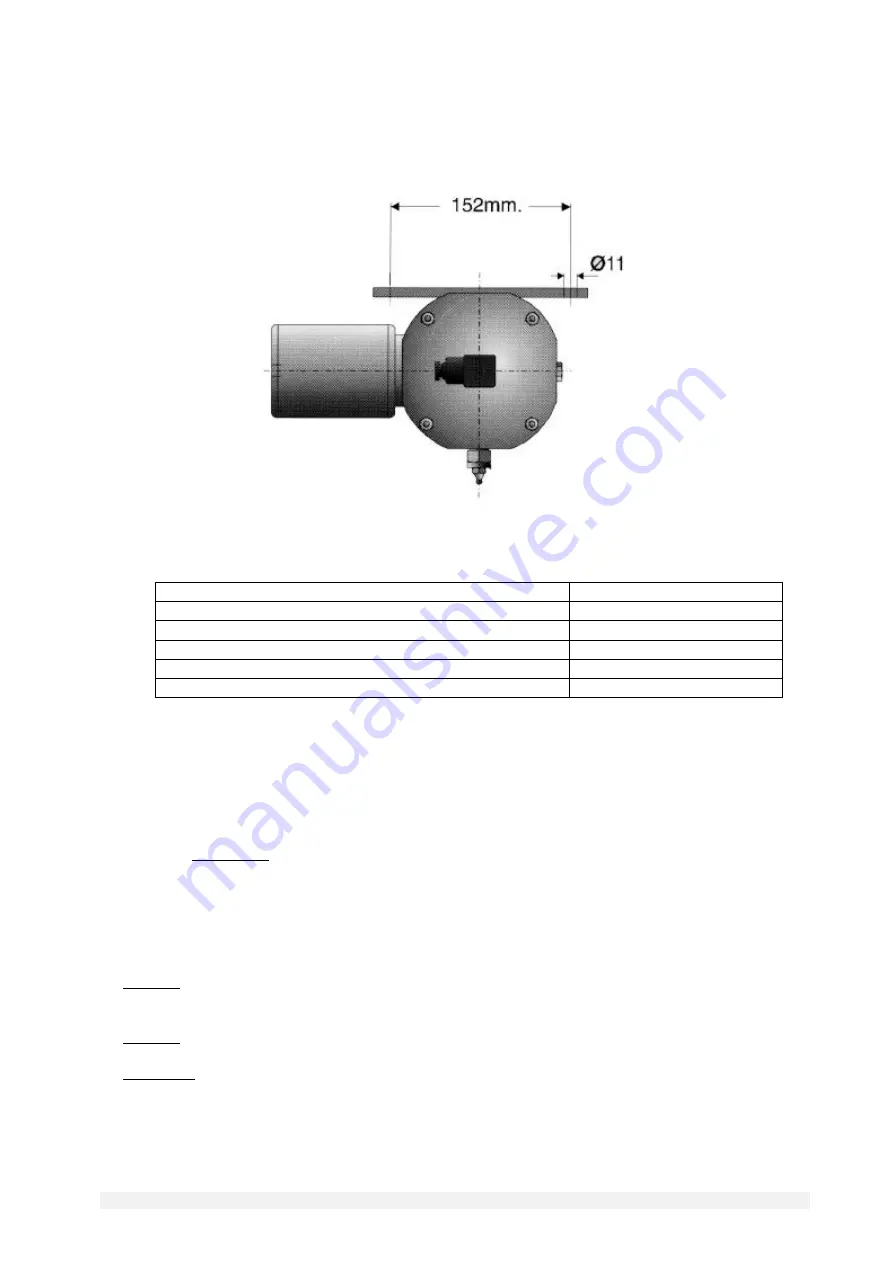
C20008IE – Pneumatically driven pump - Rev. 0 February 99 Page 4 of 9
2.2
Fixing dimensions
2.3
Other data
NLGI grease rating at working temperature
see table at sub-section 4.0
Viscosity of the lubricant at working temperature
Between 15 - 2000 cSt
Working temperature
+ 5 - + 80
°
C
Working humidity
90 % relative humidity.
Preservation temperature
- 20 - + 50 °C
Sound pressure level
< 70 dB(A)
3.0
CORRECT USE
3.1
Putting into service
♦
The unit may be used, opened and repaired only by specialised personnel.
♦
The pump MUST NOT be submersed in fluids or utilised in environments which are particularly aggressive or
explosive/inflammable if not prepared for this purpose beforehand by the supplier.
♦
For correct fixing verify the distance between centres shown in the diagram in Section 2.2.
♦
Use gloves and safety glasses as required in the lubrication oil safety chart.
♦
DO NOT use aggressive lubricants with NBR gaskets and seals; if in doubt consult the Engineering Department
of Dropsa SpA, who will provide a chart with the details of recommended oils.
♦
DO NOT ignore dangers to health and observe all hygiene standards.
♦
WARNING! All electrical components must be grounded. This refers to both electrical components and control
devices. In this regard ensure that the ground cable is correctly connected. For reasons of safety the ground cable
must be approx. 100 mm longer than the phase cables. In the event of accidental detachment of the cable, the
ground terminal must be the last to be removed.