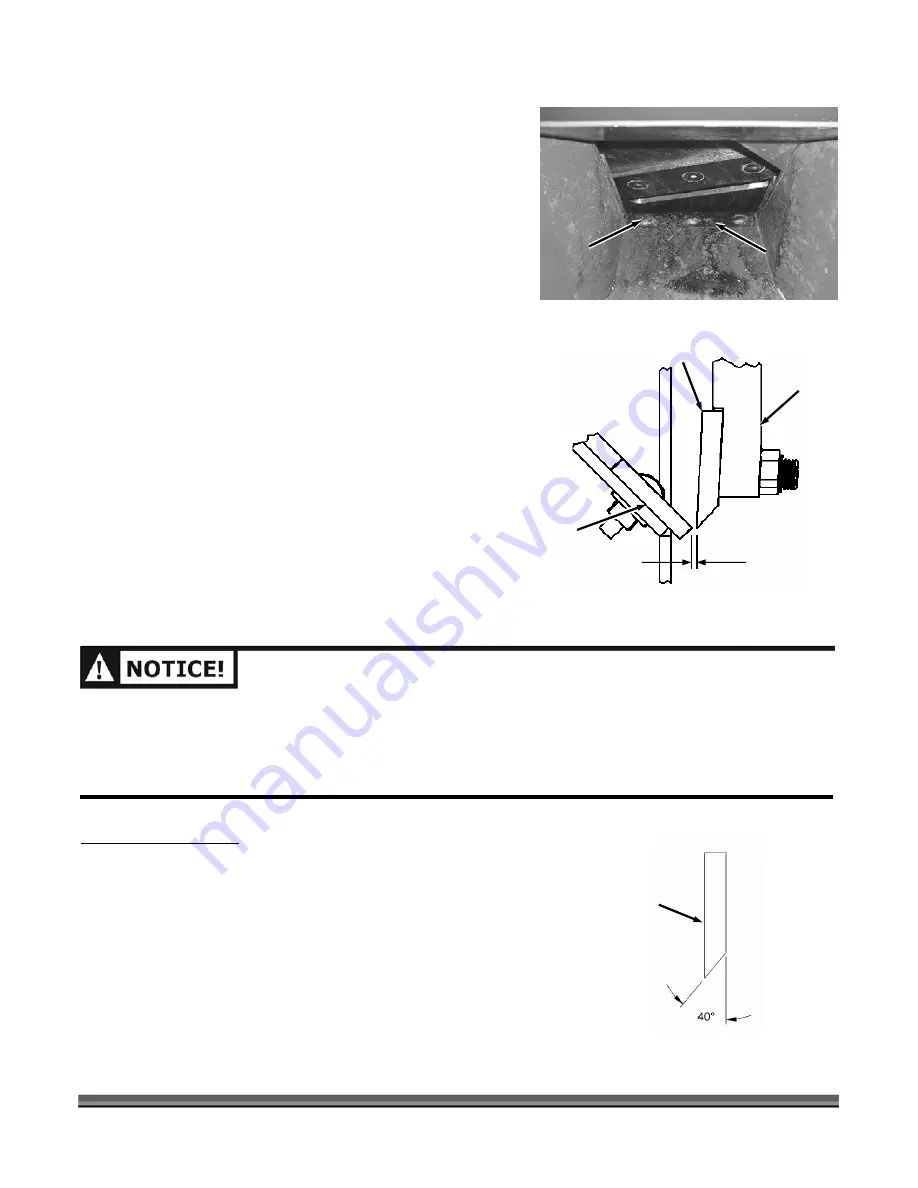
Adjusting the Knife to Wear Plate Gap
CONTACT US AT
www.DRpower.com
or CALL TOLL FREE
1-800-DR-OWNER
39
ave a slight
resistance. Now you can slide the Wear Plate up or
down (in or out) to achieve the correct gap setting
(
Figure 40
).
Wear Plate. Adjust the Wear Plate against the Knife
Gauge and tighten the Locknuts.
3.
Check the adjustment as described in the “Che
n
the Gap” in the previous section.
4.
Position the Chipper Hopper into t
and secure with the six Bolts, Washers an
o
5.
Re-connect the negative battery terminal wire
start only) and the spark plug wire.
Chipper Knife Sharpening
Tools Needed:
•
7/16" wrench
•
Gap Gauge (provided with Chipper)
1.
To adjust the Wear Plate Gap, loosen the three
Nuts
on the Carriage Bolts with a 7/16" wrench just enough
so the Wear Plate will move but still h
NOTE:
See
Figure 41
for a more detailed look at the
relationship of the Knife to Wear Plate.
2.
Take the Gap Gauge and slide it between the Knife and
cki g
he Hopper Bracket
d L cknuts.
(electric
You should never attempt to sharpen the Chipper K
freehand.
•
It is extremely important to consistently m
degree angle for proper performance (
Figure 42
).
•
Excessive heat generated during the sharpening process
will damage Knives and weaken the metal. Be sure not to
overheat the Knife during sharpening because it will
shorten the life of the Knife.
•
nife
aintain the 40-
1/16" Gap
(thickness of
Gap Gauge)
Figure 41
Chipper
Knife
Wear
Plate
Flywheel
AFTER ANY KNIFE OR WEAR PLATE MAINTENANCE OR ADJUSTMENT, ROTATE THE CHIPPER
FLYWHEEL BY USING A WOODEN STICK AND WATCH AND LISTEN CAREFULLY FOR ANY UNUSUAL
NOISES, CLICKING OR VIBRATION. IF YOU DETECT ANY OF THESE, INSPECT THE MACHINE FOR
DAMAGE, OR ANY LOOSE PARTS. REPAIR OR REPLACE N
A Y DAMAGED PARTS AND TIGHTEN ANY
LOOSE PAR
S
TS BEFORE TARTING THE DR RAPID-FEED CHIPPER.
Carriage Bolt
Wear
and Locknut
Figure 40
Plate
Figure 42
Chipper
Knife
Summary of Contents for RAPID-FEED 16.50 PRO
Page 9: ...241841 CONTACT US AT www DRpower com or CALL TOLL FREE 1 800 DR OWNER 5...
Page 16: ...12 16 50 PRO DR RAPID FEED CHIPPER...
Page 24: ...20 16 50 PRO DR RAPID FEED CHIPPER...
Page 50: ...46 16 50 PRO DR RAPID FEED CHIPPER...
Page 65: ...CONTACT US AT www DRpower com or CALL TOLL FREE 1 800 DR OWNER 61...
Page 73: ...Schematic Hopper Assembly CONTACT US AT www DRpower com or CALL TOLL FREE 1 800 DR OWNER 69...
Page 75: ...Schematic Accessories CONTACT US AT www DRpower com or CALL TOLL FREE 1 800 DR OWNER 71...
Page 76: ...72 16 50 PRO DR RAPID FEED CHIPPER...
Page 77: ...Notes CONTACT US AT www DRpower com or CALL TOLL FREE 1 800 DR OWNER 73...