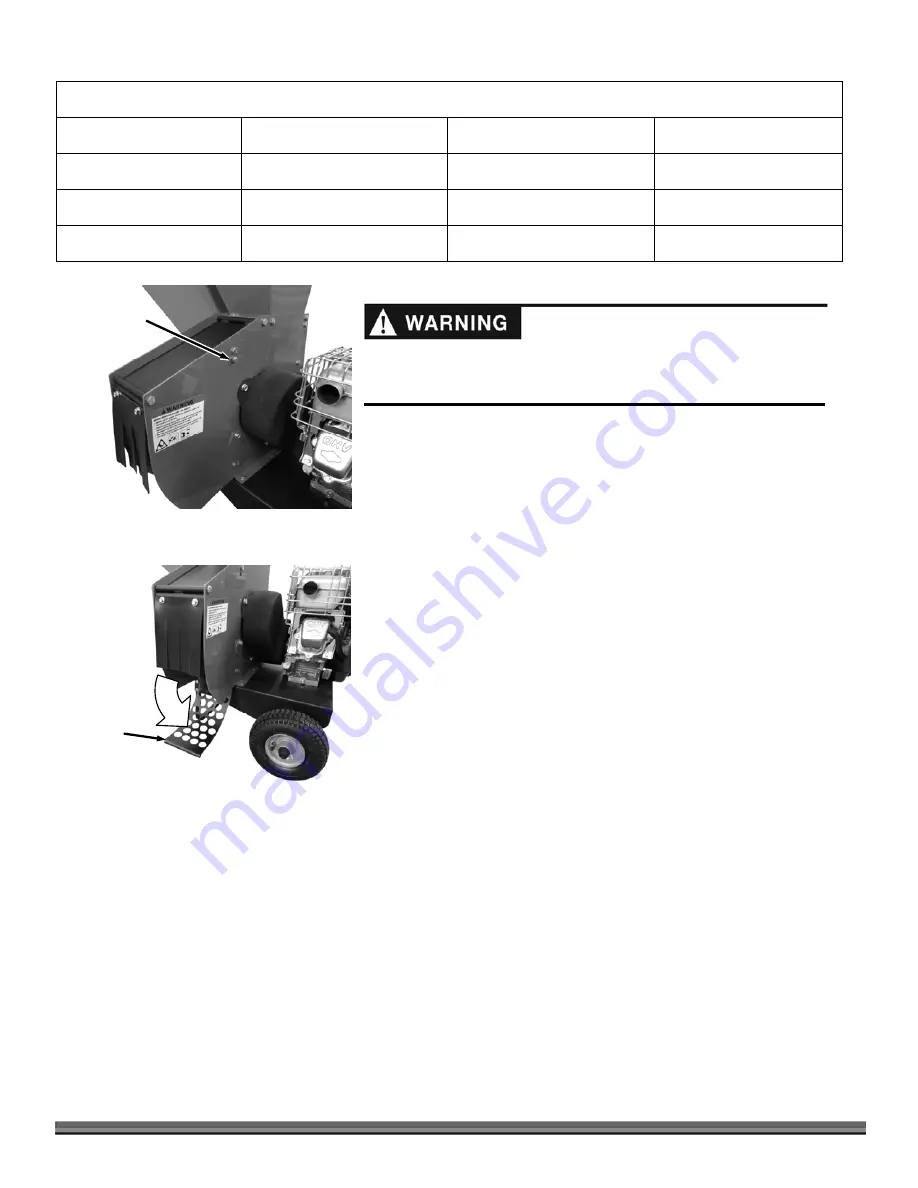
16
DR
®
11.5 CHIPPER SHREDDER
MATERIALS BEST SUITED FOR SHREDDING
Leaves Flowers Corn Stalks
Roots
Soil Palm
frond
tops
Grass
clippings Garden
debris
Potato vines
Straw and Hay
Hedge clippings
Tomato vines
Manure
Kitchen Waste
Small branches
Removing a Clog
1.
Remove any material left in the Chipper Chute and Shredder Hopper with a
wooden stick.
2.
Remove the top Screen Bolt and Locknut using two 1/2" Wrenches (
Figure
10
).
3.
Rotate the Screen down to gain access to the cutting chamber (
Figure 11
).
Note:
If the Screen will not rotate down freely, the nearby bolts can be loosened
slightly.
4.
Clear all clogged material from the machine.
5.
Rotate the Screen back into the operating position and reinstall the
hardware.
Note:
Make sure the bolt goes through the screen rather than just
behind it
.
6.
Start the machine and allow any remaining material to discharge.
7.
If you have been shredding wet/green materials the clog may be near the
shredder housing inlet. Shred a wood stick of up to 1" diameter to clear the
clogged wet material.
8.
If the clog does not clear repeat the above process.
9.
Be certain the cutting chamber is clear before trying to process more
material.
Shredder
Screen
Figure 11
Remove Bolt
and Locknut
Figure 10
Before performing any maintenance procedure or inspection, stop the
Engine, wait five minutes to allow all parts to cool. Disconnect the Spark
Plug Wire, keeping it away from the Spark Plug.
Summary of Contents for 11.5 Chipper Shredder
Page 2: ...2 DR 11 5 CHIPPER SHREDDER...
Page 24: ...24 DR 11 5 CHIPPER SHREDDER...
Page 27: ...CONTACT US AT www DRpower com 27...
Page 29: ...CONTACT US AT www DRpower com 29 Schematic Hopper Chute and Discharge...
Page 31: ...CONTACT US AT www DRpower com 31 Schematic Drive Assembly...
Page 33: ...CONTACT US AT www DRpower com 33 Schematic Cutting Chamber...