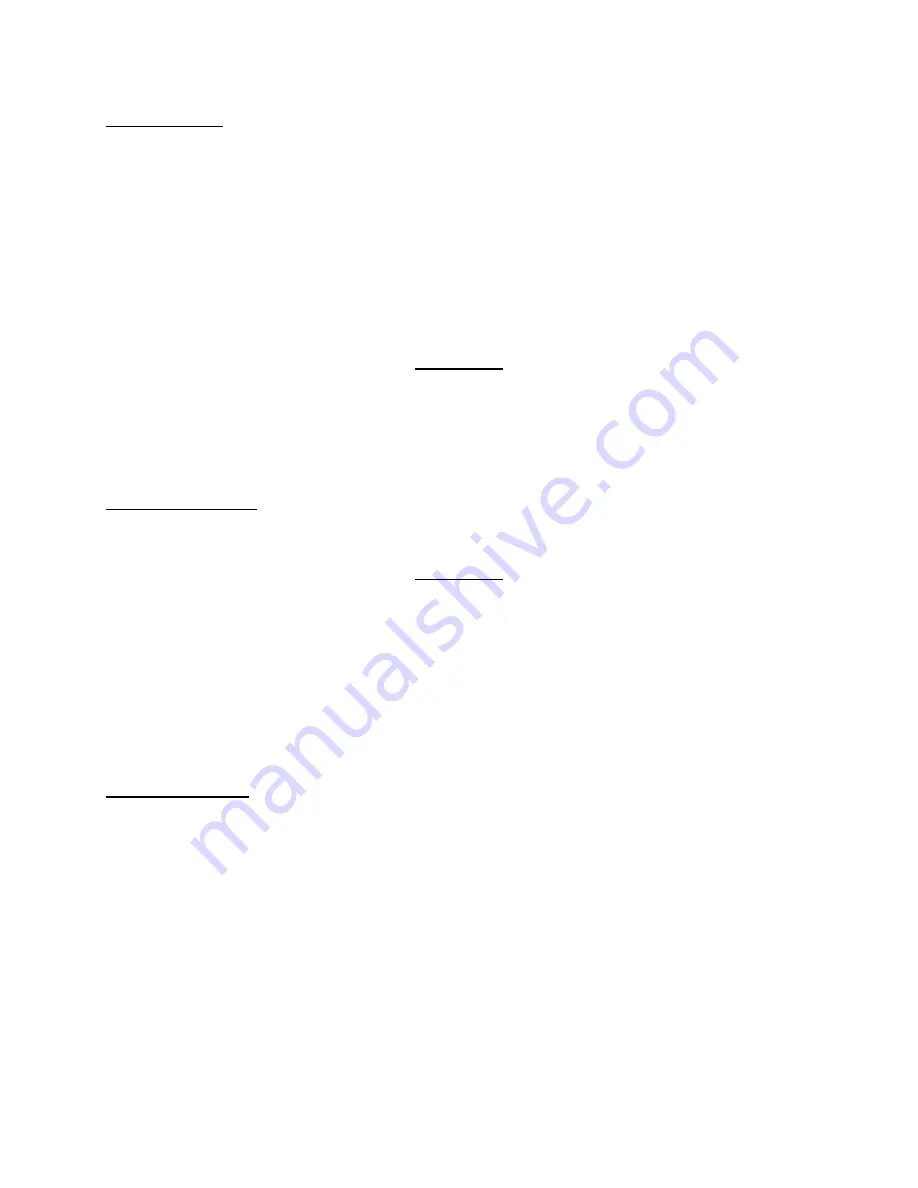
A7
Gas installation
•
The customer must install a manual shut off valve at the end of the gas supply pipe near the burner
which is approved by the American Gas Association Standard in U.S. or with the Canadian Gas
Association in Canada.
•
Plug the oven to the gas supply.
(The pipe, the fittings and the compound must be certified for gas.)
•
The gas pipe sealing compound tightness must be verified using a solution of water and soap prior
to firing the unit.
•
Clean the air contained in the gas supply pipe at the installation to insure a successful firing on the
first try.
WARNING
Make sure not to obstruct the overpressure opening on the gas regulator.
Exhaust: A draft hood is provided with the unit and it must be used when the chimney is
directly connected to a gas vent pipe. The exhaust pipe must be certified for use of gases.
2. To the electrician
Electrical supply installation must be in accordance with the electrical rating on the nameplate.
WARNING
The electrician must make sure that the supply cable does not come in contact
with the oven top which becomes hot.
A phase sequence and loss of phase relay is installed on 3 phases models to avoid wrong rotation
direction of the blowers. If the oven does not light up, swap two phases conductors in the supply
box and try again. Be sure that the power is really on the 3 phases wires next to the fuses in the
control compartment on the front of the oven. Check also if the control fuse located near the main
switch is not blown.
3. To the plumber
This equipment is to be installed to comply with the applicable federal, state or local plumbing
codes.
•
Connect the water supply pipe to the oven using good quality sealing compound. Take care
that combustible water pipes do not come in contact with hot parts on the top of the oven.
•
Check for leaks of solenoid valve.
Connect the steam system (1/4 NPT) to the cold water distribution network.
We highly recommend a water softener to eliminate minerals in the water. We suggest you to use
CUNO # CFS6135 (Doyon part number PLF240).
Note: The water flow valves for steam have been adjusted, DO NOT TOUCH.
Summary of Contents for TLOIG
Page 20: ...A18 ...
Page 23: ...SECTION B DIMENSIONS ...
Page 24: ...B1 ...
Page 25: ...B2 ...
Page 26: ...B3 ...
Page 27: ...B4 ...
Page 28: ...B5 ...
Page 29: ...B6 ...
Page 30: ...B7 ...
Page 31: ...B8 ...
Page 32: ...B9 ...
Page 33: ...B10 ...
Page 34: ...B11 ...
Page 35: ...B12 ...
Page 36: ...B13 ...
Page 37: ...B14 ...
Page 38: ...SECTION C BURNER AJUSTEMENT ...
Page 39: ...C1 ...
Page 40: ...SECTION E COMPONENT PARTS ...
Page 41: ...E1 ...
Page 43: ...E3 ...
Page 45: ...E5 ...
Page 46: ...E6 ...
Page 47: ...E7 ...
Page 48: ...E8 ...
Page 49: ...E9 ...
Page 51: ...E11 ...
Page 53: ...SECTION F CONTROL PANELS ...
Page 54: ...F1 CONTROL PANEL 120V 208V 3PH 120V 240V 3PH ...
Page 55: ...F2 ...
Page 57: ...F4 CONTROL PANEL 220V 1PH 50hZ ...
Page 58: ...F5 ...
Page 60: ...F7 CONTROL PANEL 120V 208V 3PH WATLOW 120V 240V 3PH WATLOW ...
Page 61: ...F8 ...
Page 63: ...SECTION G ELECTRIC SCHEMATICS ...
Page 64: ...G1 ...
Page 65: ...G2 ...
Page 66: ...G3 ...
Page 67: ...G4 ...
Page 68: ...G5 ...
Page 69: ...G6 ...
Page 70: ...G7 ...