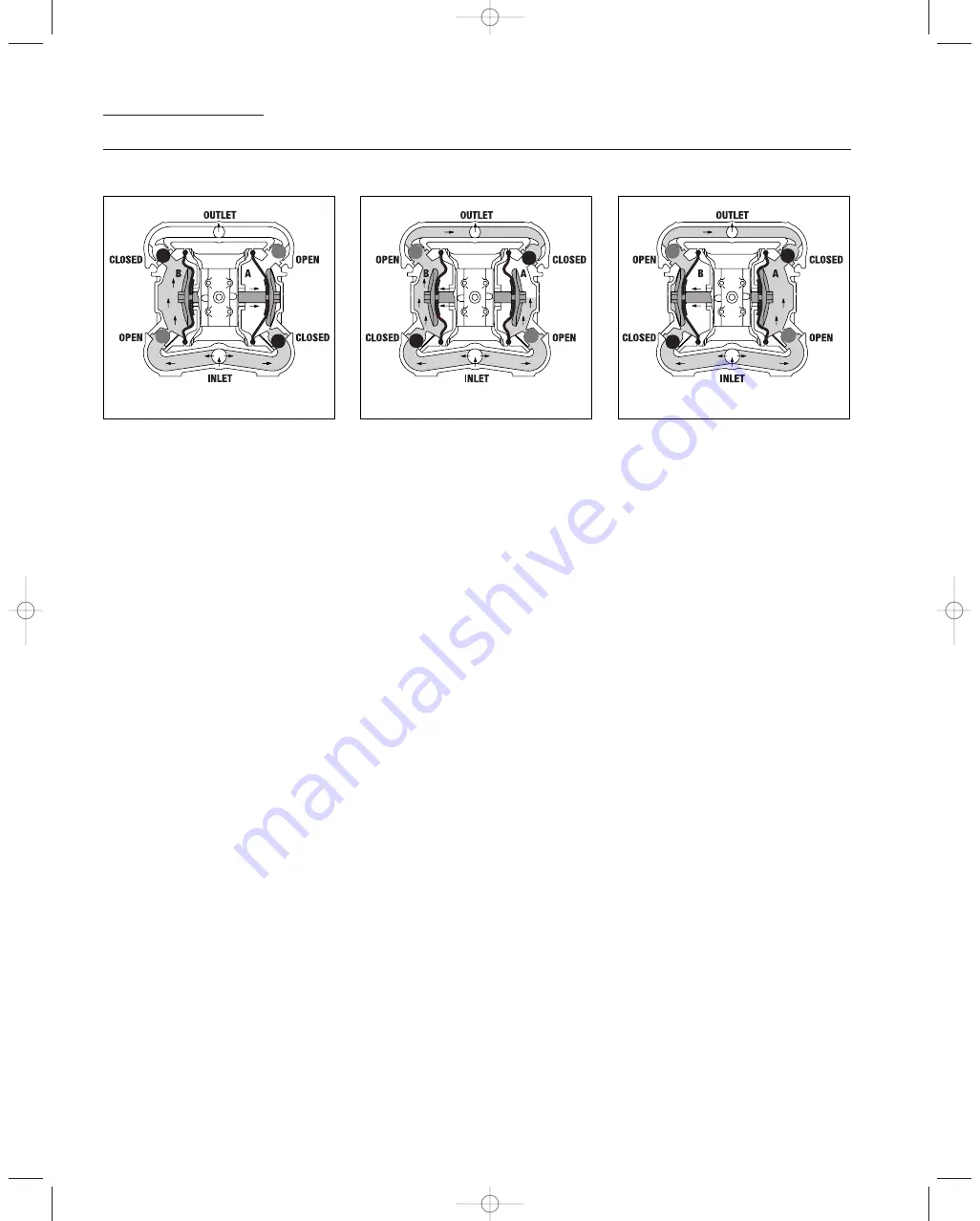
2
WILDEN PUMP & ENGINEERING, LLC
SECTION 2
THE WILDEN PUMP — HOW IT WORKS
The Wilden diaphragm pump is an air-operated, positive displacement, self-priming pump. These drawings show the flow pattern
through the pump upon its initial stroke. It is assumed the pump has no fluid in it prior to its initial stroke.
FIGURE 1
The air valve directs pres-
surized air to the back side of diaphragm
A. The compressed air is applied directly
to the liquid column separated by
elastomeric diaphragms. The diaphragm
acts as a separation membrane between
the compressed air and liquid, balancing
the load and removing mechanical stress
from the diaphragm. The compressed air
moves the diaphragm away from the
center block of the pump. The opposite
diaphragm is pulled in by the shaft
connected to the pressurized diaphragm.
Diaphragm B is on its suction stroke; air
behind the diaphragm has been forced
out to the atmosphere through the
exhaust port of the pump. The move-
ment of diaphragm B toward the center
block of the pump creates a vacuum
within chamber B. Atmospheric pressure
forces fluid into the inlet manifold forcing
the inlet valve ball off its seat. Liquid is
free to move past the inlet valve ball and
fill the liquid chamber (see shaded area).
FIGURE 2
When the pressurized
diaphragm, diaphragm A, reaches the
limit of its discharge stroke, the air valve
redirects pressurized air to the back side
of diaphragm B. The pressurized air
forces diaphragm B away from the center
block while pulling diaphragm A to the
center block. Diaphragm B is now on its
discharge stroke. Diaphragm B forces the
inlet valve ball onto its seat due to the
hydraulic forces developed in the liquid
chamber and manifold of the pump.
These same hydraulic forces lift the
discharge valve ball off its seat, while the
opposite discharge valve ball is forced
onto its seat, forcing fluid to flow through
the pump discharge. The movement of
diaphragm A toward the center block of
the pump creates a vacuum within liquid
chamber A. Atmospheric pressure forces
fluid into the inlet manifold of the pump.
The inlet valve ball is forced off its seat
allowing the fluid being pumped to fill the
liquid chamber.
FIGURE 3
At completion of the stroke,
the air valve again redirects air to the
back side of diaphragm A, which starts
diaphragm B on its exhaust stroke. As
the pump reaches its original starting
point, each diaphragm has gone through
one exhaust and one discharge stroke.
This constitutes one complete pumping
cycle. The pump may take several cycles
to completely prime depending on the
conditions of the application.
RIGHT STROKE
MID STROKE
LEFT STROKE
WIL_14070_E_01.qxd 1/4/06 6:29 AM Page 2