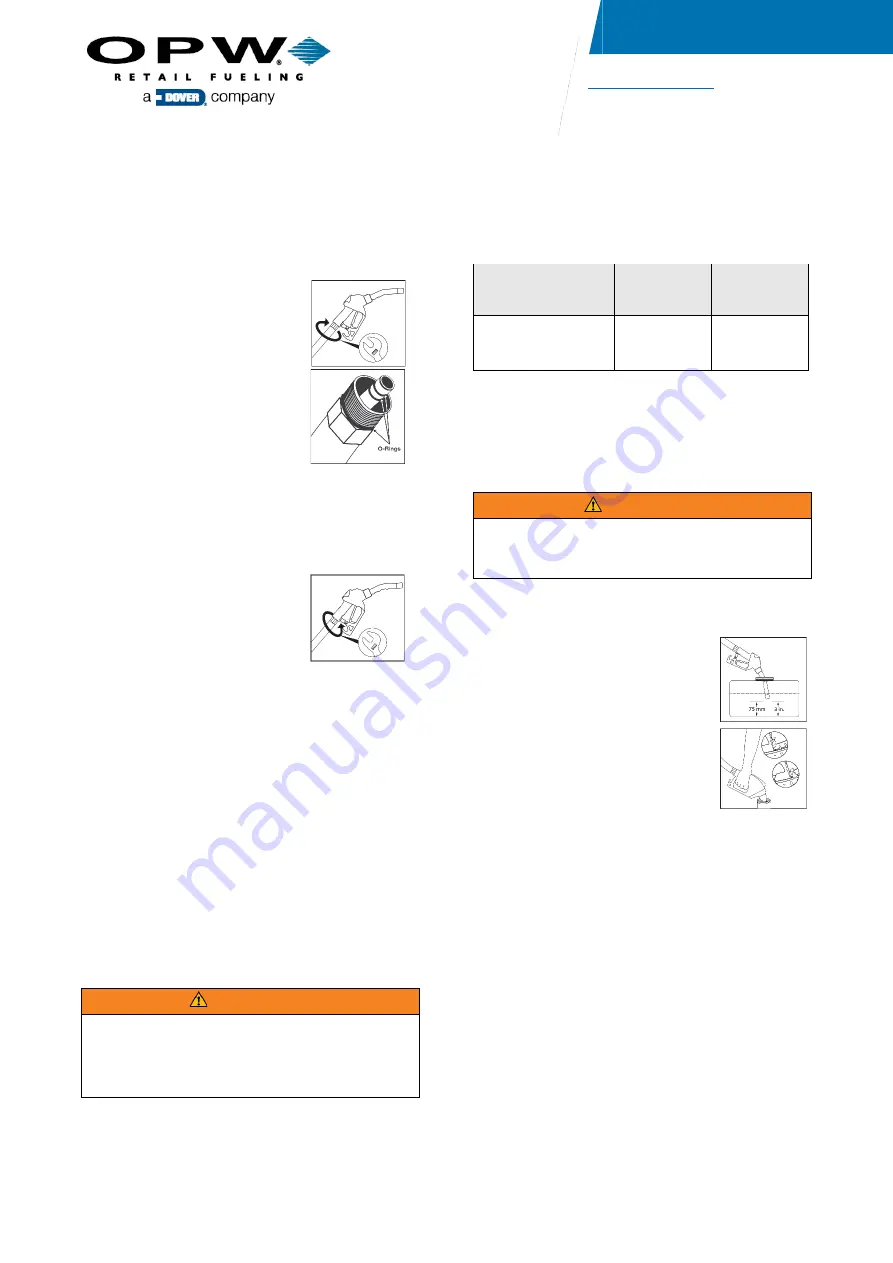
Please visit OPW’s website:
information or contact OPW Customer
Service at
+44 (0) 1756 799 773
(EU)
or
1-800-422-2525
(US)
opwglobal.com
3
DEFINING
| WHAT’S NEXT
214916 revision A
September 2019
•
Shut off power to the dispenser and close the
emergency shut-off valves under the dispenser. Relieve
system pressure before servicing or replacing dispensing
products, such as nozzles, swivels, or breakaways.
•
Refer to the most recent edition of National Safety
Standard.
•
If nozzle replacement, secure retractor before removing
the nozzle.
•
If nozzle replacement, remove old
nozzle with a wrench. Carefully
drain fuel from hose & nozzle into
approved container.
•
For a new facility installation,
purge/flush hose point before
installing nozzles. If nozzles are
used to purge/flush system, this
could result in foreign material in
nozzle’s main valve and cause a
nozzle not to shut off.
•
Verify selection of nozzle for application.
•
Do not use pipe sealant or PTFE tape on the inlet
threads of the nozzle.
•
Verify that O-rings are present on hose and not torn or
damaged. Coat O-rings with light oil for installation to
prevent damage.
•
Engage the external thread into the
nozzle or breakaway and tighten
the hose nut per hose instructions.
•
Flow test nozzles before putting
nozzles in service. See testing
instructions.
•
Check continuity. See testing instructions.
•
Check for leaks between all connections of hanging
hardware. Repair or replace, as required, if any leaks are
found.
•
Dispenser modifications may be necessary for proper
nozzle storage. Always comply with the dispenser
instructions and local codes.
•
Register your OPW product at www.opwglobal.com
•
After installation, each nozzle should be tested for proper
operation prior to being put into service.
EQUIPMENT REQUIRED
•
Stopwatch, approved 20 L grounded, vented, metal test
container, and megohmmeter.
CONTINUITY TEST
•
After installation of hanging hardware and prior to flow
test, check continuity following EN 60204-1 for proper
test equipment and method of testing.
WARNING
Fueling equipment is designed to operate in a
pressure range of 0,5 to 3,5 bar. If the pressure
exceeds 6 bar, the nozzle will open regardless of
lever position. Exceeding maximum pressure may
result in property damage, injury, or death.
FLOW TEST
•
Start stopwatch, initiate flow into an approved test
container, with the nozzle lever held in the fully open
position.
•
Check each hose point to verify a minimum flow rate*
and maximum flow rate**:
Model(s)
Maximum
Flow Rate
Minimum
Flow Rate
21AG, 21BG,
21AGV, 21BGV
45 L/min
8 L/min
If hose point does not comply, check system and repair
prior to putting into service.
*Minimum flow rate must be met in lowest hold-open clip position. If
hold-open clip is not present, minimum must be met in fully open
position.
**Maximum flow rate must not exceed when nozzle is in highest clip
position or in the fully open position.
WARNING
STATIC ELECTRICITY/FIRE HAZARD
Maintain contact between the nozzle spout and
approved test container during flow test.
SHUT-OFF TEST
•
Start flow into approved test container; place nozzle in
low clip position.
•
Immerse nozzle spout tip in the
dispensed fluid in the approved test
container. The nozzle tip must be at
least 75 mm from the bottom of the
container to prevent back-pressure in
the spout.
•
Nozzle must shut off.
•
Repeat procedure for all clip positions.
Nozzle must always shut off in all clip
positions.
•
Test each nozzle a minimum of five
(5) times in each clip position.
•
For models without hold-open racks, test at fully open
position only.
•
For Type I nozzles: If no shut off occurs, check to ensure
flow rate is greater than 8 L/min.
•
If flow rate is above minimum flow rate and there is no
shut-off, replace the nozzle.
•
Verify that the pump switches off when the nozzle is
returned to the dispenser nozzle boot.