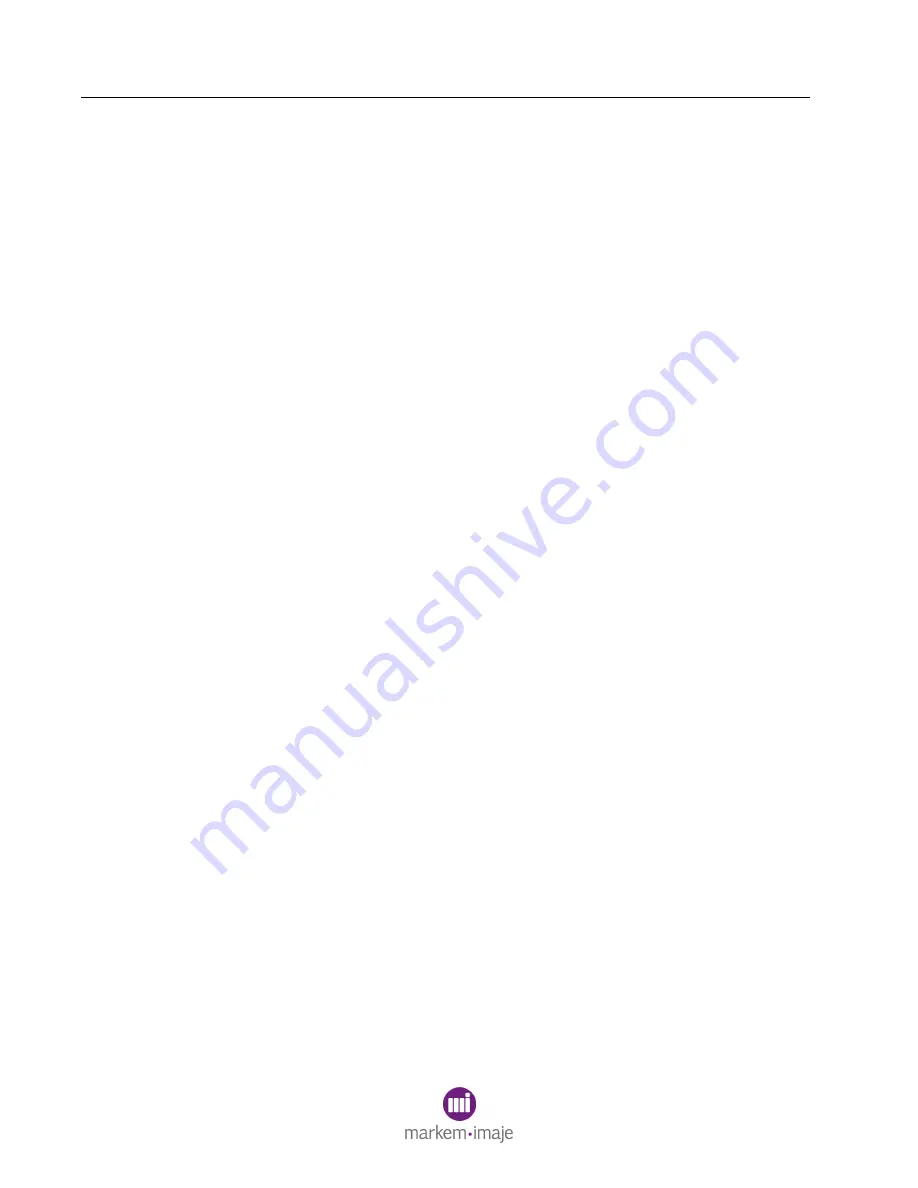
SECTION 6 Field Replaceable Parts
6–8
0855855eng
6/08
5
Replacing the Ink Delivery Module (IDM)
NOTE: This procedure should not be done while the IDM is hot.
Allow the IDM to cool before beginning.
5.1
What You Will Need
•
4mm Allen wrench
•
Large flathead screwdriver
•
1/2 inch open-end wrench
•
5/8 inch or 7/8 inch open-end wrench
5.2
Preparation
1. Check to see if there is a full ink bottle in the machine by opening
the ink door. If a full ink bottle is present, remove it.
2. Power off the Model 5200/5400 and disconnect the power cable.
3. Remove the front cover by loosening the five large captive
screws.
NOTE: The ground wire may need to be disconnected from the print
station.
5.3
Removal
1. Loosen the screw for the ink bottle guide. Lower the guide and
retighten the screw (1, Figure 6-5).
2. Use two wrenches to disconnect the ink lines from the IDM (2,
Figure 6-5). Bend them forward to be out of the way.
3. Wear an antistatic wrist strap connected to the earth point that
connects the green and yellow ground wire from the user
interface (1, Figure 6-18). Remove the control board (2, Figure 6-
18) and place it in the static-shielding bag. Close the bag.
4. Unplug the transformer connector from the printhead volt board.
5. Disconnect two IDM connectors from the backplane board (4,
Figure 6-5), and work them out of the wire duct (5, Figure 6-5).
6. Disconnect the IDM ground line (6, Figure 6-5).
7. Loosen the four cap screws located under the enclosure (7,
Figure 6-5) approximately one turn.
8. Slide the IDM forward in the keyhole slots, and lift it out of the
print station enclosure.
Summary of Contents for Markem-Imaje 5200
Page 1: ...s e r v i c e g u i d e ...
Page 2: ......
Page 4: ...iv 0855855eng 6 08 ...
Page 13: ...Model 5200 5400 Service Guide SECTION 1 General Information ...
Page 14: ......
Page 22: ...SECTION 1 General Information 1 8 0855855eng 6 08 FRONT REAR ...
Page 28: ...SECTION 1 General Information 1 14 0855855eng 6 08 ...
Page 29: ...Model 5200 5400 Service Guide SECTION 2 Basic Operation ...
Page 30: ......
Page 42: ...SECTION 2 Basic Operation 2 12 0855855eng 6 08 ...
Page 43: ...Model 5200 5400 Service Guide SECTION 3 Care and Cleaning ...
Page 44: ......
Page 54: ...SECTION 3 Care and Cleaning 3 10 0855855eng 6 08 ...
Page 55: ...Model 5200 5400 Service Guide SECTION 4 Diagnostic Tools ...
Page 56: ......
Page 89: ...Model 5200 5400 Service Guide SECTION 5 Troubleshooting ...
Page 90: ......
Page 102: ...SECTION 5 Troubleshooting 5 12 0855855eng 6 08 ...
Page 103: ...Model 5200 5400 Service Guide SECTION 6 Field Replaceable Parts ...
Page 104: ......
Page 133: ...SECTION 6 Field Replaceable Parts 0855855eng 6 08 6 29 Figure 6 23 Figure 6 24 1 1 ...
Page 150: ......
Page 151: ......
Page 152: ......
Page 153: ......
Page 154: ......
Page 155: ......
Page 156: ......
Page 157: ......
Page 158: ......
Page 159: ......
Page 160: ......
Page 161: ......
Page 162: ......
Page 163: ......
Page 164: ......
Page 165: ......
Page 166: ......
Page 167: ......
Page 168: ......
Page 169: ......
Page 170: ......
Page 171: ......
Page 172: ......
Page 173: ......
Page 174: ......
Page 175: ......
Page 176: ......
Page 177: ......
Page 178: ......
Page 179: ......
Page 180: ......
Page 181: ......
Page 182: ......
Page 183: ......
Page 184: ......
Page 185: ......
Page 186: ......
Page 187: ......
Page 188: ......
Page 189: ......
Page 190: ......
Page 191: ......
Page 192: ......
Page 193: ......
Page 194: ......
Page 195: ......
Page 196: ......
Page 197: ......
Page 198: ......
Page 199: ......
Page 200: ...User Documentation Department ...