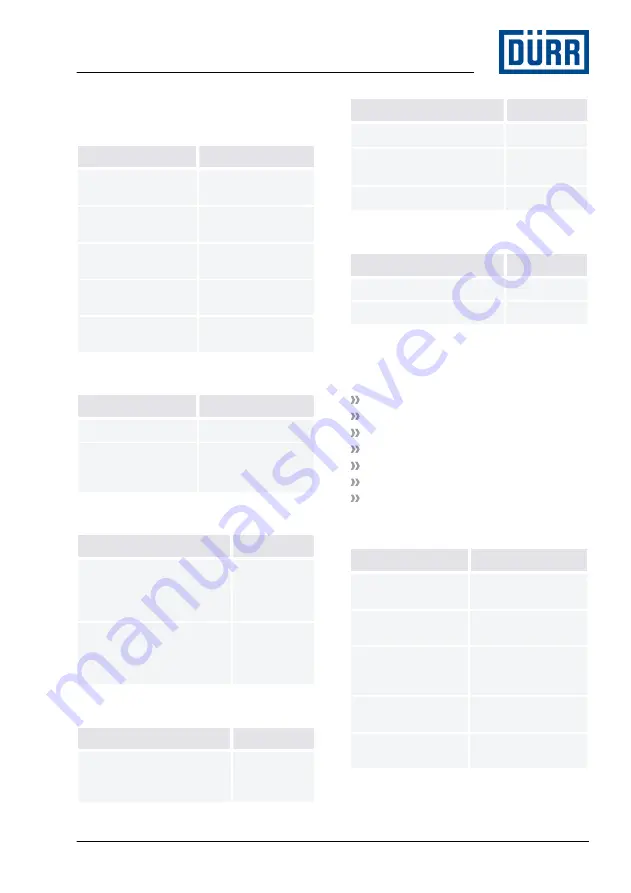
10
Technical data
10.1 Dimensions and weight
Detail
Value
Weight (without flow
cup)
480 g
Nozzle diameter
(with AL air cap)
1.0 to 2.2 mm
Nozzle diameter
(with EL air cap)
2.8 mm
Nozzle diameter
(with GL air cap)
4.0 mm
Nozzle diameter
(with RS air cap)
1.5 mm
10.2 Connections
Connection
Nominal width
Material
G3/8”/M 16 x 1.5
Air
1/4” (for BSP
threads and NPSM
threads)
10.3 Operating conditions
Detail
Value
Maximum allowable mate-
rial temperature when
operating with protective
gloves
40 °C
Maximum allowable mate-
rial temperature when
operating with heat-
resistant protective gloves
60 °C
10.4 Emissions
Detail
Value
Emission sound pressure
level L
pA
, A – according to
EN 14462
86 dB
Detail
Value
Uncertainty K
pA
5 dB
Sound power level L
WA
, A ֪
– according to EN14462
99.8 dB
Uncertainty K
WA
5 dB
10.5 Operating values
Detail
Value
Max. air pressure
4 bar
Air pressure, optimum
2 to 3 bar
10.6 Type plate
The type plate is placed on the housing and
features the following details:
Product designation
Material number
Year of manufacture
Serial number
EX labeling
Manufacturer
CE labeling
10.7 Materials used
Component
Material
Housing
Nickel plated alu-
minum
Compression
springs
Stainless steel
Materials in contact
with material
Stainless steel,
nickel plated alu-
minum
Seals in contact
with material
PTFE
Seals without mate-
rial contact
PE, PTFE
Technical data
05/2018
EcoGun 116 - MSG00017EN
27/44