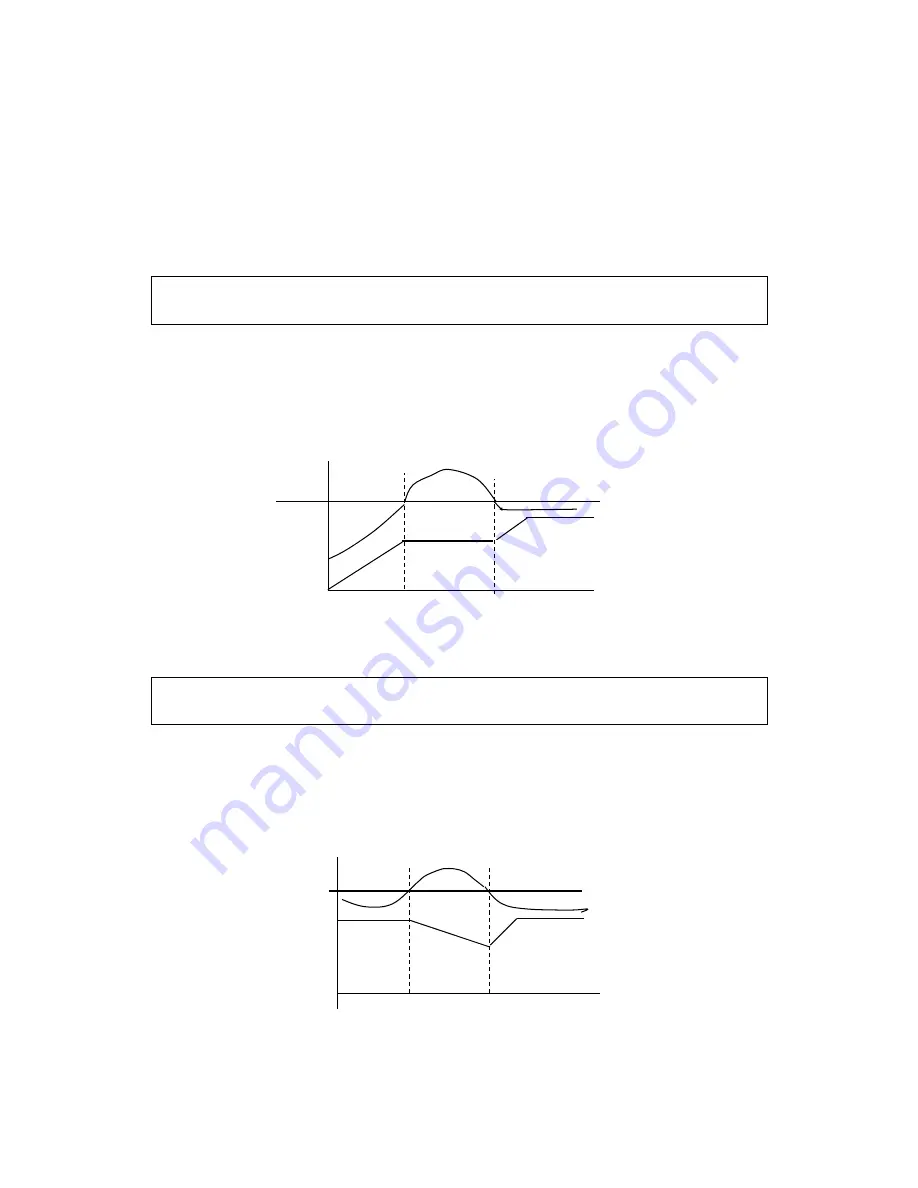
44
When the inverter is in decelerating, due to the effect of load inertia, the motor will produce a
return energy to the inverter and cause the DC voltage of the inverter to increase. So when the function
of overvoltage stall prevention is set valid and the DC voltage of the inverter becomes too high, the
inverter will stop decelerating till the DC side voltage decreases to its rated value, then the inverter
will go on to execute deceleration and the deceleration time will be extended automatically.
* Note: When the output voltage is higher the inverter will become abnormal or turn to
protection. In such case P079 can be set to 0 (Invalid), which is easy to cause overvoltage protection.
P080 Stall Prevention Level during Acceleration
Set Range: 0~200% Unit: 1% Factory Setting: 150
When the inverter is in accelerating, due to over load or too short acceleration time, the output
current of the inverter will go up quickly and exceed the rated standard level. When this happens, the
inverter will stop accelerating until the current returns under its rated value, will the inverter go on to
accelerate. When using the frequency track function the value of P080 should be lowered properly.
The greater the load initia quantity is, the smaller the value of P080 should be set. Otherwise it is
extremely easy to cause overcurrent protection.
I
Stall Prev. Level
Output frequency
T
100% current is the rated current of the motor. When this parameter is set to 0, the stall prevention
function is invalid.
P081 Stall Prevention Level at Constant Speed
Set Range: 0~200% Unit: 1 Factory Setting: 0
When the inverter is in constant running, due to load fuctuation and other reasons, the current
will go up. When the current exceeds its rated value, the inverter will lower the output frequency.
When the output current returns to its normal range the inverter will accelerate again to its set
frequency.
Stall prevention level
during running
Output frequency
T
100% current is the rated current of the motor. When this parameter is set to 0, the stall prevention
function is invalid.
Summary of Contents for DLM1-01D5S2G
Page 26: ...26 ...