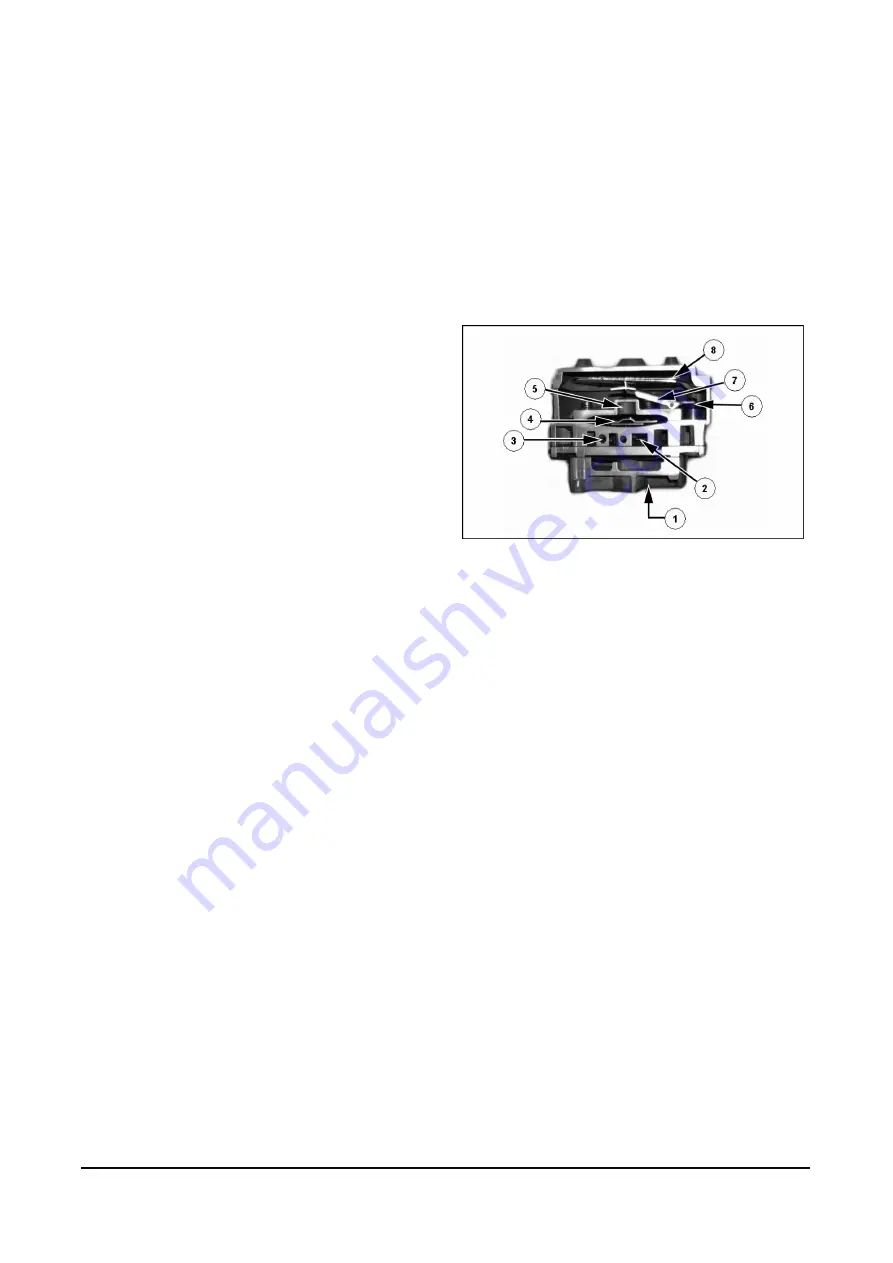
G643(E) Service Manual
Chapter 5. Engine Management System (EMS)
154
Liquid propane must be converted into a gaseous
form in order to be used as a fuel for the engine.
When the regulator receives the desired vacuum
signal it allows propane to flow to the mixer. As the
propane flows through the regulator the pressure is
reduced in two stages from tank pressure to slightly
less than atmospheric pressure. As the pressure of
the propane is reduced, the liquid propane vaporizes
and refrigeration occurs inside the regulator due to
the vaporization of liquid propane. To replace heat
lost to vaporization, engine coolant is supplied by
the engine driven water pump and pumped through
the regulator. Heat provided by this coolant is
transferred through to the fuel vaporization chamber.
N-2007 Operation
(Refer to Figure 6.)
Liquid propane, at tank pressure, enters the N-2007
through the fuel inlet port (1). Propane liquid then
flows through the primary valve (2). The primary
valve located at the inlet of the expansion chamber
(3), is controlled by the primary diaphragm (4),
which reacts to vapor pressure inside the expansion
chamber. Two springs are used to apply force on
the primary diaphragm in the primary diaphragm
chamber (5), keeping the primary valve open when
no fuel pressure is present.
A small port connects the expansion chamber to the
primary diaphragm chamber. At the outlet of the
expansion chamber is the secondary valve (6). The
secondary valve is held closed by the secondary
spring on the secondary valve lever (7). The
secondary diaphragm controls the secondary lever.
When the pressure in the expansion chamber
reaches 1.5 psig (10.3 kPa) it causes a
pressure/force imbalance across the primary
diaphragm (8). This force is greater than the primary
diaphragm spring pressure and will cause the
diaphragm to close the primary valve.
Since the fuel pressure has been reduced from tank
pressure to 1.5 psig (10.3 kPa) the liquid propane
vaporizes. As the propane vaporizes it takes on heat
from the expansion chamber. This heat is replaced
by engine coolant, which is pumped through the
coolant passage of the regulator. At this point vapor
propane will not flow past the expansion chamber of
the regulator until the secondary valve is opened. To
open the secondary valve, a negative pressure
signal must be received from the air/fuel mixer.
When the engine is cranking or running a negative
pressure signal (vacuum) travels through the vapor
fuel outlet connection of the regulator, which is the
regulator secondary chamber, and the vapor fuel
inlet of the mixer. The negative pressure in the
secondary chamber causes a pressure/force
imbalance on the secondary diaphragm, which
overcomes the secondary spring force, opening the
secondary valve and allowing vapor propane to flow
out of the expansion chamber, through the
secondary chamber to the mixer.
Figure 6. Parts View of N-2007 Regulator
Because vapor propane has now left the expansion
chamber, the pressure in the chamber will drop,
causing the primary diaphragm spring force to re-
open the primary valve allowing liquid propane to
enter the regulator, and the entire process starts
again. This creates a balanced condition between
the primary and secondary chambers allowing for a
constant flow of fuel to the mixer as long as the
demand from the engine is present. The fuel flow is
maintained at a constant output pressure, due to the
calibrated secondary spring. The amount of fuel
flowing will vary depending on how far the
secondary valve opens in response to the negative
pressure signal generated by the air/fuel mixer. The
strength of that negative pressure signal developed
by the mixer is directly related to the amount of air
flowing through the mixer into the engine. With this
process, the larger the quantity of air flowing into the
engine, the larger the amount of fuel flowing to the
mixer.