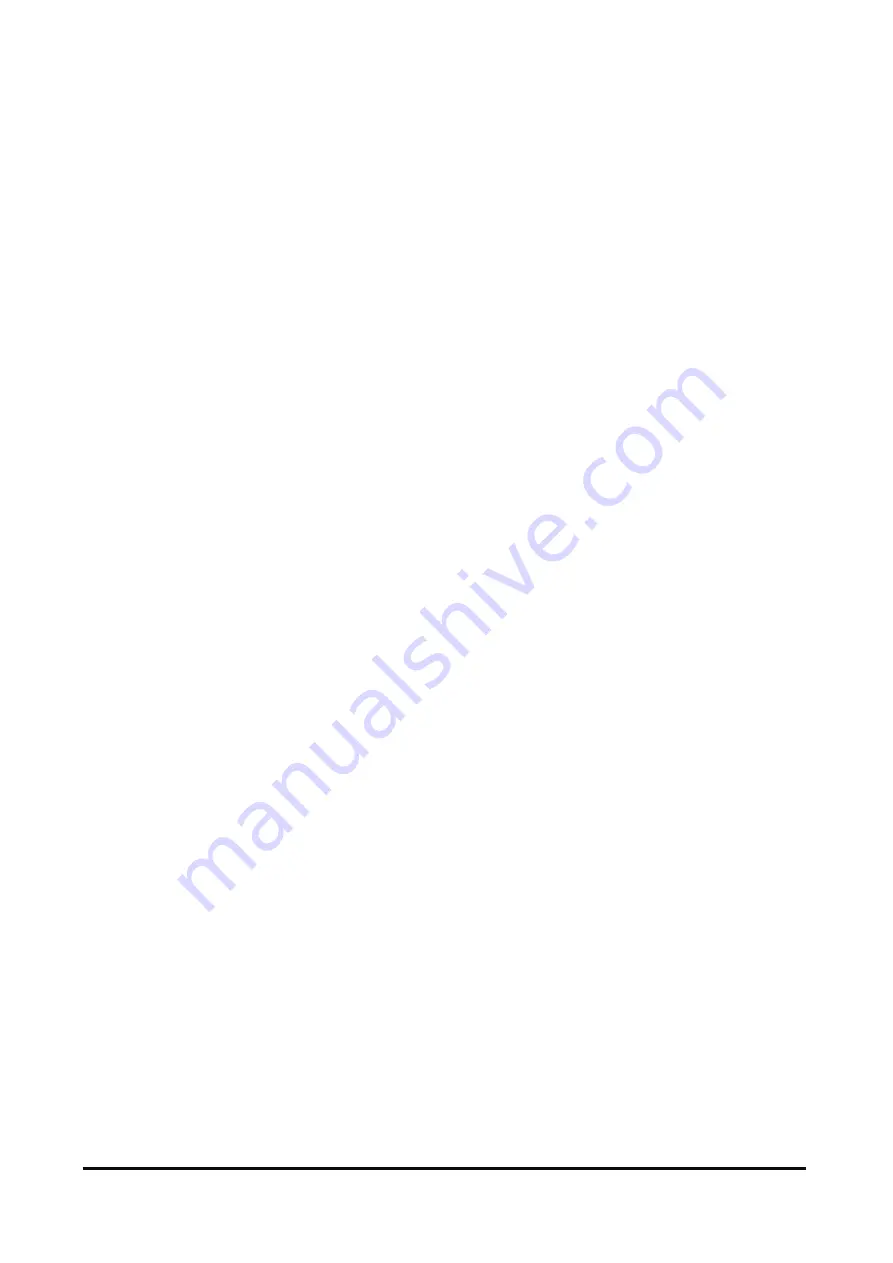
Vehicle Systems
Hydraulic System Operation
25
The hydraulic system has a hydraulic tank (13)
which holds a fluid for a hydraulic pump (12). A
hydraulic pump sends a pressure fluid to the
hydraulic actuator system and hydraulic steering
system. A pump fluid flows from hydraulic pump (12)
to priority valve (15), where a fluid divides. Part of
fluid goes to the hydraulic steering system. The
remaining fluid goes to the control valve (6) through
hydraulic line (17)..
The levers of control valve move spools in control
valve. The movement of spool makes a fluid for a lift
cylinder and/or tilt cylinder (8) and/or side shift
cylinder (5).
The return hydraulic fluid from each cylinder flows
through control valve, hydraulic line (17) and a filter-
return (14), and back to a hydraulic tank..
There is a safety unload function on the first block of
control valve that any function doesn’t work even
though any lever is shifted when operator leaves a
seat for more than 3 seconds. The solenoid valve
(10) for unload function is electrically connected to
the electric on-off switch beneath a seat. When the
operator leaves a seat for more than 3 seconds, the
solenoid valve (10) is off, which let a system
pressure go down to less than 7 bar. Once the
operator sits on a seat, the solenoid valve is on and
immediately all functions work normally.
There is a safety lift lock function on lift block that a
lowering of carriage or mast is impossible if the lift
lever is shifted for lowering when operator leaves a
seat for more than 3 seconds or a start key is off.
The solenoid valve (7) for lift lock is electrically
connected to the electric on-off switch beneath a
seat. When the operator leaves a seat for more
than 3 seconds or a start key is off, the solenoid
valve becomes off, which leads to block the lowing
flow passage. Once a start key is on and operator
sits on seat,, the solenoid valve becomes on and
immediately a lowering works normally
On the emergency that lowering doesn’t work
normally, the needle valve on lift block needs to
be loosened about half counterclockwise turn ,
which makes it possible to lower the mast or
carriage when lift spool is shifted for lowering.
After lowering the mast or carriage to the ground
absolutely and a start key off, the possible
causes can be inspected. Its detailed trouble
shooting guide will be shown in TESTING and
ADJUSTING.
The relief valve-main (11) releases the excessive
pressure to the hydraulic tank when the pressure in
the lift circuit goes higher than a setting pressure
shown a CONTROL VALVE SECTION of
SPECIFICATION. The relief valve-auxiliary (9)
release the excessive pressure to the hydraulic tank
when the pressure in tilt circuit and auxiliary circuit
goes higher than a setting pressure shown a
CONTROL VALVE SECTION of SPECIFICATION.
The speed at which lift cylinders are lowered is
controlled by the flow regulator valve integrated into
lift spool.
Flow protector (2) & (4) integrated to lift cylinder acts
as a fuse valve if the line between control valve (flow
regulator) and flow protector is broken when the lift
cylinder is raised or lowered. This prevents the
sudden fall of mast or carriage if a hydraulic line is
broken.
The tilt backward, forward speed, side shift cylinder
speed are controlled by adjustable flow control kit in
control valve.
There is a counter-balance valve (or, tilt lock valve)
in tilt speed to prevent cavitation (development of air
pocket) in tilt cylinder.
For a complete hydraulic circuit, see the foldout, in
the back of this module.