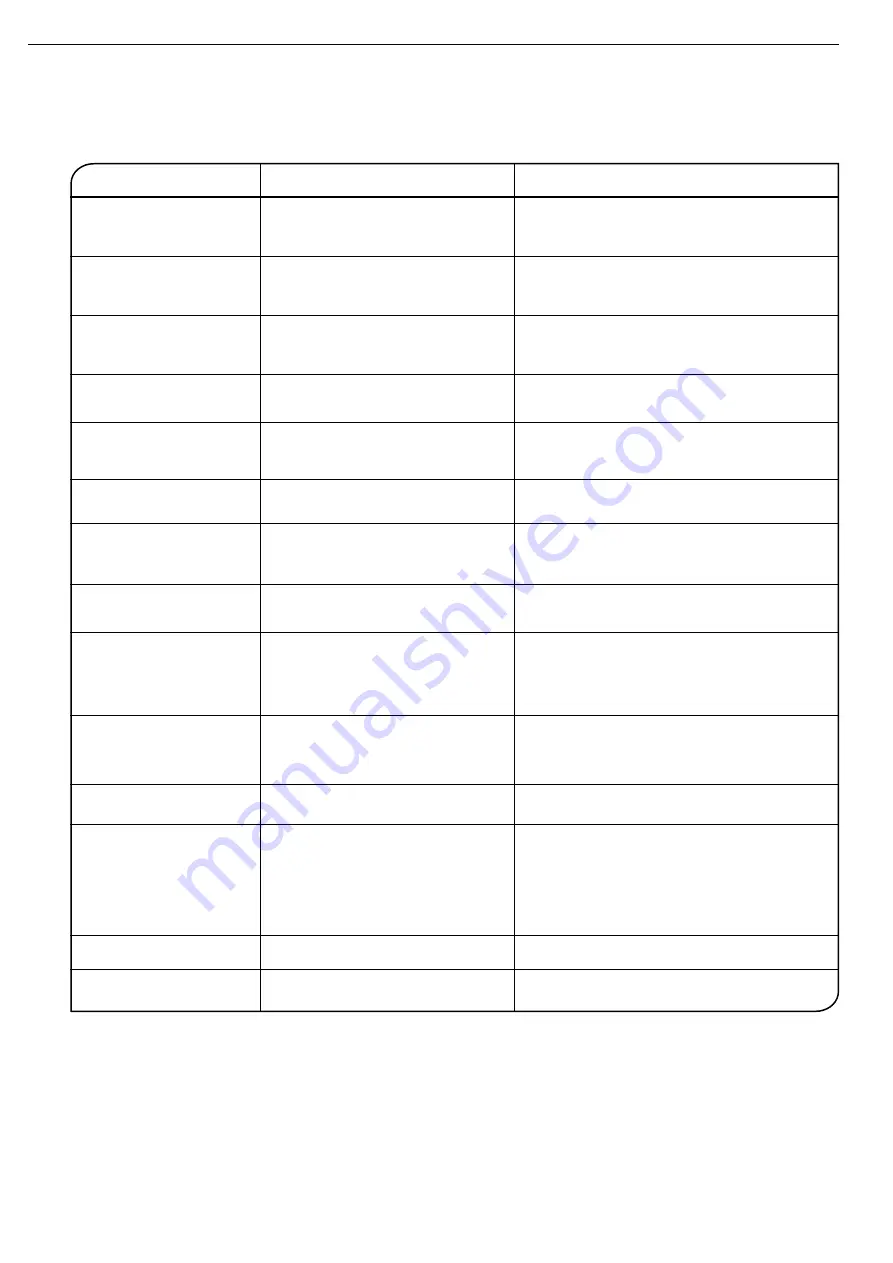
12
4
instructions
for
use
series
drh
1/2/3/4 -
dst
/
n
/
s
-
dst
/
r
-
drt
MAN16MG05
6.7.1 Main anomalies and malfunctionings
The most common conditions of bad functioning are shown, where reasonably predictable, in relation to the
individual operating functions of the DRH electric wire rope hoist and related trolleys.
it won’t start
it won’t start
it won’t start
it starts partially
(in one direction only)
the movement does not stop
in the due space
the movement does not stop
at the end of the run
the movement continues
even after releasing
the relative button
excessively loud lifting reducer
excessively loud trolley reducer
shrill noise of the brake in the
braking phases
shrill noise of the wheels
(functioning in jolts)
shrill noise of the wire rope
and/of the drum/transmission
pulley
the hoist jumps during
the travelling
the hoist and/or the trolley move
slowly or the hoist lifts the load
with difficulty
live current is detected at the hook
the trolley skids on the tracks
and does not travel
X
X
-
X
X
inoltre il carico scivola
e non viene trattenuto
X
X
X
-
X
-
X
-
X
X
-
X
X
X
X
X
X
-
X
X
X
-
X
X
-
X
• ascent/descent limit switch
• ascent/descent contactor
• ascent/descent button
• overload device
• hoist motor
• lifting motor fuses
• hoist/trolley power cable
• power line
• low voltage transformer
• line contactor
• line fuses
• right/left limit switch
• right/left contactor
• right/left button
• trolley motor
• travelling motor fuses
• limit switches or button of the inhibited function (independent
from one another)
• missing phase
• brake of the function
• brake of the function
• limit switch of the function
• direction button broken
• related contactor
• “false contact”
• lacking lubrication
• beyond the service cycle
• too narrow play between wheel and girder
• lacking lubrication
• incorrect/too intense service
• dust present
• excessive play
• worn brake lining
• play between wheel and girder is incorrect
• lacking lubrication
• incorrect/too intense service
• worn rope or drum/pulleys
• lacking lubrication
• incorrect/too intense service
• incorrect contact between track and wheel
• couplings of sliding girder are not aligned
• drop in voltage
• overload (due to no overload device)
• seizure beginning in the reducer
• incorrect contact between track and wheel
• faulty or broken electrical system
• play between wheel and girder wing too narrow
• obstacle on girder wing
• oil or grease on girder wing
Lifting
hoist
Travelling
trolley
Possible cause of fault
FUNCTION
=>
FAULT
6.7
Breakdowns and solutions
=>
124 MAN16MG05
INSTRUCTIONS FOR USE SERIES DRH
1/2/3/4
- DST/N/S - DST/R - DRT
MAN16MG05
instructions
for
use
series
drh
1/2/3/4 -
dst
/
n
/
s
-
dst
/
r
-
drt
12
5
6.7.2 Breakdowns of components and possible solutions
Causes of bad functioning of individual parts and possible solutions
6.7.3 Authorised staff for intervention in case of breakdown
The staff authorised to intervene in most cases of breakdown, or where not indicated differently, are expert
maintenance people or trained with a specific preparation on mechanical and electrical parts. Where shown, however,
the intervention of specialised suitably-trained staff or the technical staff of the manufacturer is necessary.
6.7.4 Putting out of service
If the hoist cannot be repaired, proceed to the putting out of service operations, signalling the breakdown with a
sign; request the intervention of the assistance service.
wire rope jumps and loud noise
is heard
brakes skid
brake heats excessively
brake does not unblock
the brake tends to “stick”
the limit switch is blocked while
opening, it does not go back to
normal
buttons on push-button panel
are blocked “shut”
the contactors have “stuck”
contacts
motor too warm
motor won’t start
motor has trouble starting
motor hums and absorbs
a lot of power
short circuit in the winding
of the motor
false contact
• breakdown of wire rope and/or drum or pulleys
• lacking lubrication
• wear and tear of brake linings
• oil/grease present
• incorrect service
• incorrect regulation
• working in unsuitable environmental conditions
• lacking electrical power
• incorrect regulation
• working in unsuitable environmental conditions
or outside the running service
• obstruction of activating head
• incorrect striking
• connections cut off
• obstruction of push-button control panel
• use in unsuitable environmental conditions or for
unforeseen use
• voltage variations are > 10%
• little cooling
• environmental temperature > than that foreseen
• use of hoist does not conform to running service
foreseen
• burn out fuse
• contactor has cut off power
• overload, block due to high starting
frequencies, insufficient protection
• on starting the voltage or frequency are lowered
with respect to the nominal value
• faulty winding, rotor is in contact with the stator
• a power phase is locking
• reducer is blocked
• brake is blocked
• short circuit in the power cables
• short circuit in the motor
• breakdown in the winding
• involuntary activating of the function
• replace wire rope, and if necessary the drum or pulleys
• lubricate wire rope, drum and pulleys
• set the play or replace the gasket
• clean the gasket
• restore foreseen working conditions
• adjust brake
• restore the voltage valves
• adjust brake
• restore suitable conditions
• cleaning and restoring of correct conditions
• cleaning
• check the conductor
• restore the correct conditions of use
• ensure the correct voltage
• restore correct circulation of air
• gear characteristics of the motor
• adapt service conditions to those foreseen
• replace fuse
• check the contactor of the function
• rewind the motor to ensure better protection
• check control device
• improve the line or power supply conditions
• repair by a specialist
• check power supply and/or the contactor
• request intervention by a specialist
• check and if necessary set the brake
• eliminate the short circuit
• request the intervention of a specialist
• rewind the motor
• check the conductors of the push-button control panel
Possible causes of the fault
Possible actions to be taken
Type of fault
123
instructions
for
use
series
drh
1/2/3/4 -
dst
/
n
/
s
-
dst
/
r
-
drt
MAN16MG05
6.6.7 Replacing the hook side cheek of the hook block
Replacing the hook side cheek of the hook block for 2-rope fall hoists (fig. 222)
• Remove the label plate
-1-
before removing the fixing rivets (with a drill and tip Ø 3 mm).
• Remove the screw
-2-
and the clip
-3-
.
• Remove the snap ring
-4-
.
• Take off the transverse support
-5-
.
• Take off the hook side cheek
-6-
.
• Install the new hook side cheek with the procedure in reverse.
• Fix the label plate on the transverse support with 4 rivets Ø 3x7 mm
Replacing the hook side cheek of the hook block for 4-rope fall hoists (fig. 223)
External hook side cheek
• Remove the label plate
-1-
before removing the fixing rivets (with drill and tip ø3 mm).
• Remove the screw
-2-
and the clip
-3-
.
• Remove the external hook side cheek
-4-
.
• Install the new hook side cheek with the procedure in reverse.
• Fix the label plate on the hook side cheek with 4 rivets Ø 3x7mm.
Internal hook side cheek
• Remove the label plate
-1-
before removing the fixing rivets (with a drill and tip ø3 mm).
• Remove the screw
-2-
and the clip
-3-
.
• Remove the external hook side cheek
-4-
.
• Take off the pulley
-5-
.
• Remove the internal hook side cheek
-4-
.
• Install the new hook side cheek with the procedure in reverse.
• Fix the label plate on the hook side cheek with 4 rivets Ø 3x7mm.
Carry out the operation with the hook block dismantled from the hoist.
For the dismantling and the reassembling of the hook block, see paragraph 6.6.1.
To be able to carry out the following operations, the following are needed:
• Portable drill with ø 3 mm point for removing aluminium rivets
• Riveter for fixing plates with ø 3x7 mm rivets
fig. 222
fig. 223
4
1
3
5
6
2
3
1
4
5
4
2
125
KMAN16MG05
Summary of Contents for DRH 1 Series
Page 128: ...KMAN16MG05...
Page 129: ......