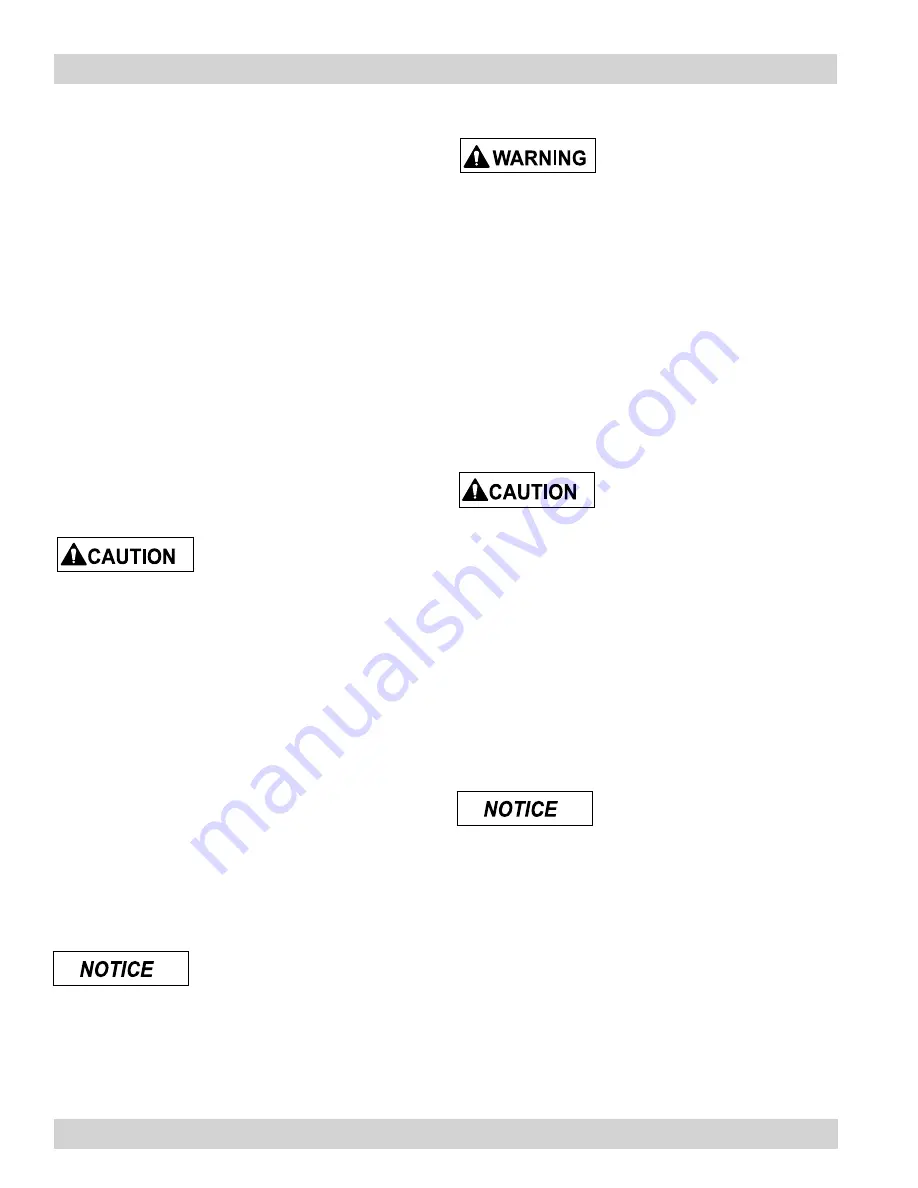
5
Donaldson Company, Inc.
Inspection on Arrival
1. Inspect collector upon delivery.
2. Report any damage to the delivery carrier.
3. Request a written inspection report from the Claims
Inspector to substantiate any damage claim.
4. File claims with the delivery carrier.
5. Compare collector received with description of
product ordered.
6. Report incomplete shipments to the delivery carrier
and your Donaldson Torit representative.
7. Remove crates and shipping straps. Remove loose
components and accessory packages before lifting
collector from truck.
8. Check for hardware that may have loosened during
shipping.
9. Use caution removing temporary covers.
Installation Codes and Procedures
Codes may regulate recirculating
filtered air in your facility.
Consult with the appropriate authorities
having jurisdiction to ensure compliance
with all national and local codes regarding
recirculating filtered air.
Safe and efficient operation of the collector depends on
proper installation.
Authorities with jurisdiction should be consulted
before installing to verify local codes and installation
procedures. In the absence of such codes, install
collector according to the National Electric Code,
NFPA No. 70-latest edition and NFPA 91 (NFPA 654 if
combustible dust is present).
A qualified installation and service agent must complete
installation and service of this equipment.
All shipping materials, including shipping covers, must
be removed from the collector prior to or during collector
installation.
Failure to remove shipping
materials from the collector will
compromise collector performance.
Inspect collector to ensure all hardware is properly
installed and tight prior to operating collector.
Installation
Use proper equipment and adopt
all safety precautions needed for
servicing equipment.
Electrical service or maintenance work must
be performed by a qualified electrician and
comply with all applicable national and local
codes.
Turn power off and lock out electrical
power sources before performing service or
maintenance work.
Do not install in classified hazardous
atmospheres without an enclosure rated for
the application.
Turn compressed air supply OFF, bleed and
lock out lines before performing service or
maintenance work.
Site selection must account for
wind, seismic zone, and other
load conditions when selecting the location for
collectors.
Codes may regulate acceptable locations for
installing dust collectors. Consult with the
appropriate authorities having jurisdiction to
ensure compliance with all national and local
codes regarding dust collector installation.
Collectors must be anchored in a manner
consistent with local code requirements.
Anchors must be sufficient to support dead,
live, seismic, and other anticipated loads.
Consult a qualified engineer for final selection
of anchorage.
Do not set compressed-air
pressure above 100-psig as
component damage can occur.
All compressed air components must be sized
to meet the system requirements of 90-100-psig
supply pressure.
The compressed-air supply must be oil
and moisture free. Contamination in the
compressed air used to clean filters will result
in poor cleaning, cleaning valve failure, or poor
collector performance.
Purge compressed air lines to remove
debris before connecting to the collector’s
compressed air manifold.
Summary of Contents for PowerCore VH 1-4
Page 43: ......