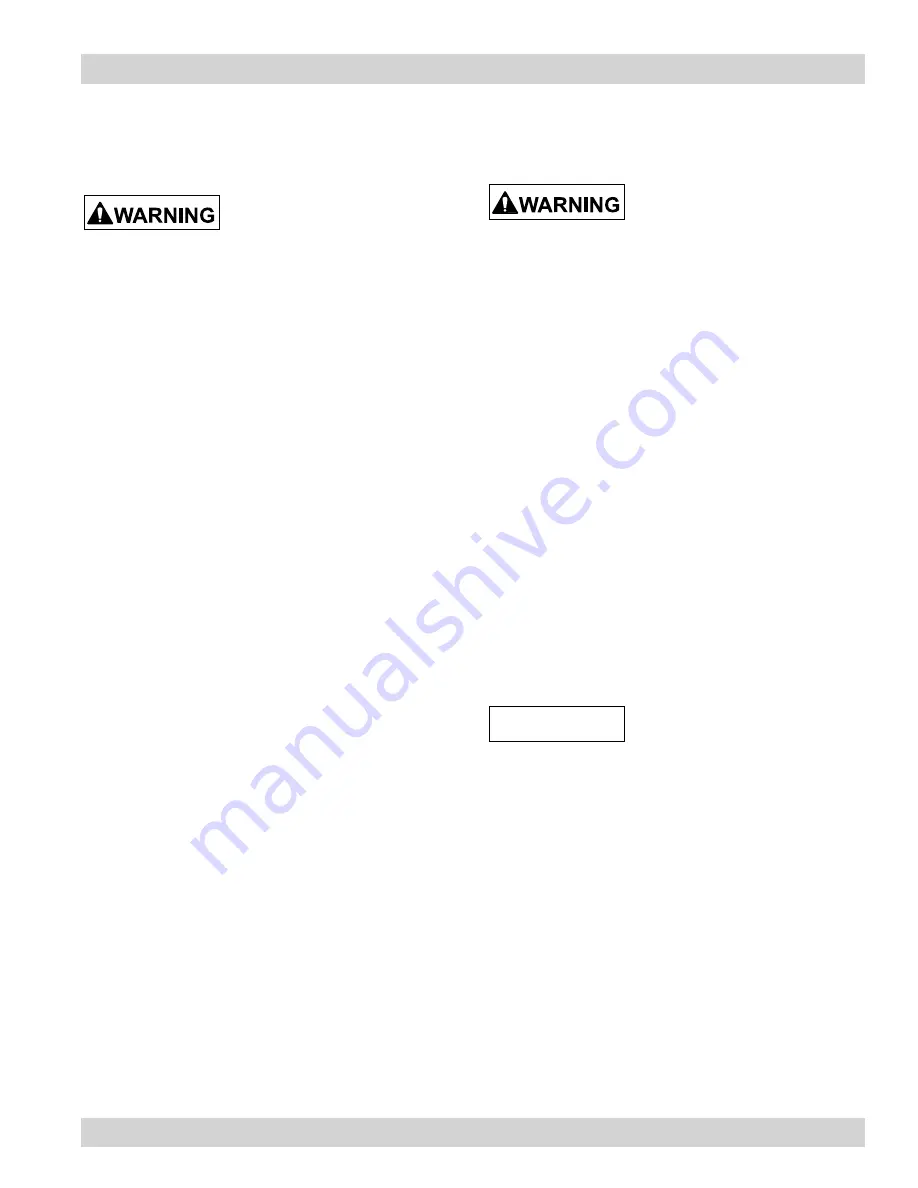
Mini-Mist, MM 500 and MM 1200
12
Maintenance Information
Instruct all personnel on safe use and maintenance
procedures.
Use proper equipment and adopt
all safety precautions needed
for servicing equipment. Electrical service
or maintenance work must be performed by
a qualified electrician and comply with all
applicable national and local codes.
Turn power off and lock out electrical
power sources before performing service or
maintenance work.
Do not install in classified hazardous
atmospheres without an enclosure rated for
the application.
Operational Checklist
1. Monitor the physical condition of the collector and
repair or replace any damaged components.
Routine inspections will minimize downtime and
maintain optimum system performance. This
is particularly important on continuous-duty
applications.
2. Monitor pressure drop across filters.
Abnormal changes in pressure drop indicate a
change in operating conditions and possibly a fault
to be corrected. For example, prolonged lack of
compressed air will cause an excess build-up of dust
on the filters resulting in increased pressure drop.
Cleaning off-line with no flow usually restores the
filters to normal pressure drop.
3. Monitor exhaust.
Filter Removal and Installation
Use proper safety and protective
equipment when removing
contaminants and filters.
Dirty filters may be heavier than they appear.
Use care when removing filters to avoid
personal injury.
1. Turn power to unit OFF.
2. Examine the door seal and seal frame, and replace
as necessary. Check the door gutters and rubber
drain flap for accumulations and obstructions, clean
as necessary.
3. Inspect the cabinet interior and remove any foreign
material that may have accumulated.
Impinger
1. Clean or soak the impinger in mild detergent or
solvent, or in severe cases, steam.
2. Re-install with the handle facing you.
Pre-Filters
1. Wash or soak the 1-in aluminum pre-filter in mild
detergent or solvent. This pre-filter can be washed
several times before replacing.
Do not use high-pressure
washing. Filter damage will
occur.
2. When replacing, observe the direction-of-flow arrow
on the filter frame, and install accordingly.
3. Dispose of filters in accordance with local
procedures.
4-in Wire Mesh
1. Soak the filter in an appropriate wash tank Rince and
dry.
2. Re-install with the handle facing you.
NOTICE