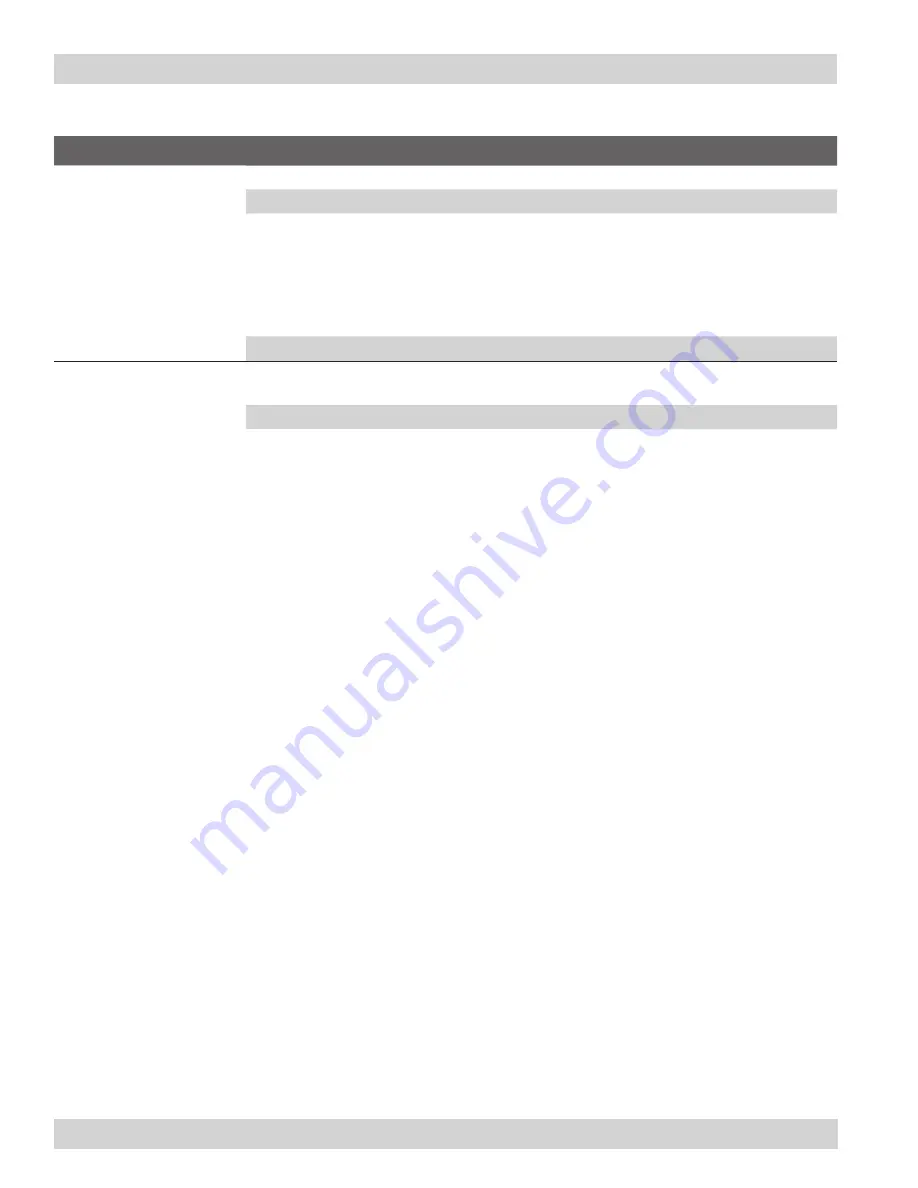
31
Donaldson Company, Inc.
Problem
Probable Cause
Remedy
Total loss of suction
Blower motor stopped
Check motor started overloads, fuses and interlocks.
Check motor connections and windings.
Filters plugged
Check that the dust removal container is not full and
that the equipment served is operating. Turn fan OFF
and allow the controller to perform several complete
cleaning cycles. Remove each filter bag, vacuum
outside surfaces, and reinstall. Replace damaged or
torn filters.
Obstructed ductwork
Check and remove obstructions.
Clean-air outlet
discharging dust
Filter bags not installed
correctly
See Filter Bag Replacement.
Torn or damaged filters
Replace as necessary.
Troubleshooting
Summary of Contents for Dalamatic Cased DLMC 1/2/15
Page 35: ......