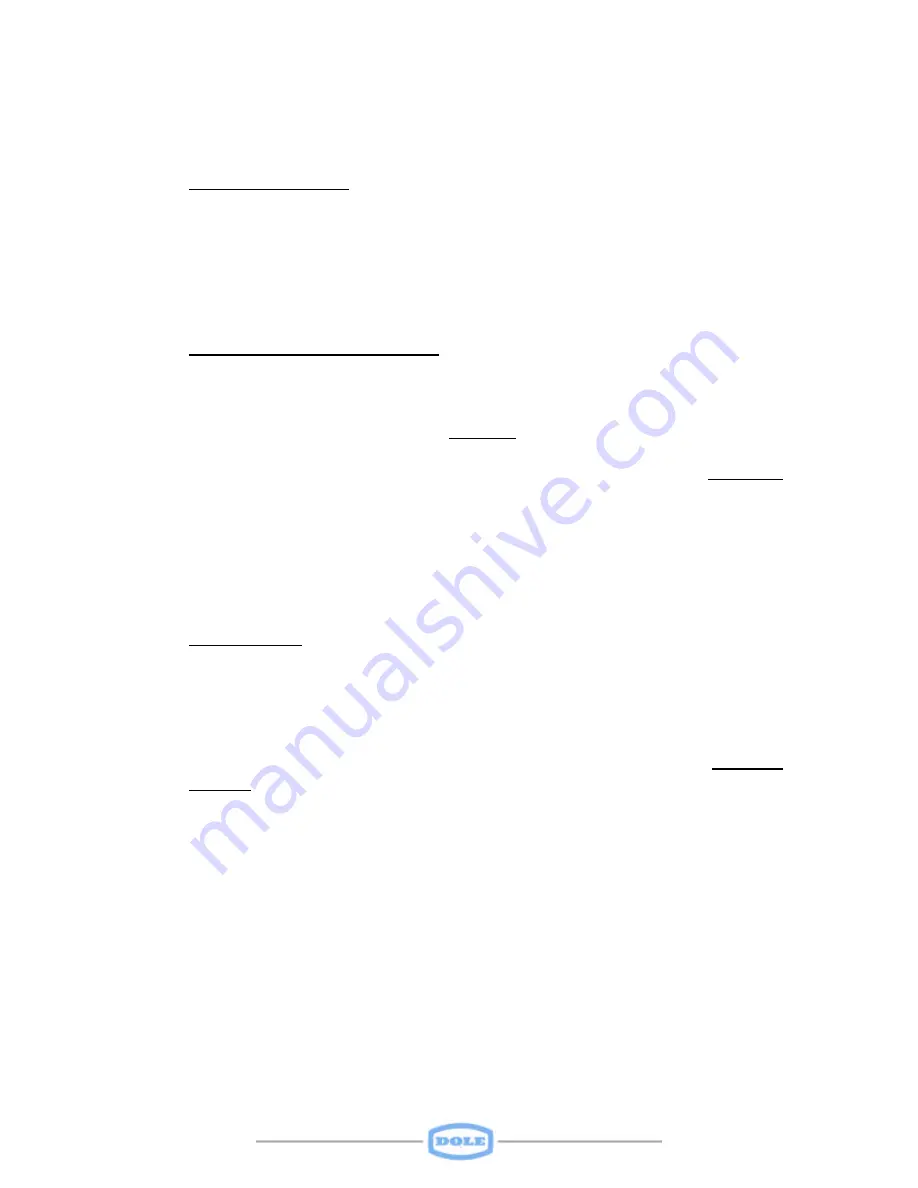
17
DO NOT add refrigerant unless sight glass indicates in undercharge
condition after running the compressor for at least two hours.
8. Crankcase Oil Level
After the compressor has been in operation for at least two hours check
the compressor crankcase oil level. The oil level in the crankcase oil sight
glass should stabilize at the center of the sight glass, with compressor
operating. After initial inspection of crankcase oil level, check level at
least once a week.
9. Setting Water Regulating Valve
The water-regulating valve will have been factory preset to 210-psig-
compressor discharge pressure and for best operating efficiency should
be maintained at that level. To increase compressor discharge pressure,
adjust the valve counter clockwise. This will decrease cooling water flow
and cause the compressor discharge pressure to rise. To decrease
compressor discharge pressure adjust the valve clockwise. This will
increase the water flow and cause the compressor discharge pressure to
fall.
COMPRESSOR DISCHARGE SHOULD NOT BE ALLOWED TO
RISE ABOVE 250 PSIG OR TO DECREASE BELOW 150 PSIG.
10. Miscellaneous
For efficient freezing, plates should be kept free of frost. When the freezer
is not in use the doors should be left open to aid in defrosting plate
surfaces.
Different thickness of product may be frozen simultaneously in separate
stations . This is not an efficient method of freezing since thicker packages
take longer to freeze than thinner ones and production freezing rates will
be lower than would be the case if all packages were the same thickness.