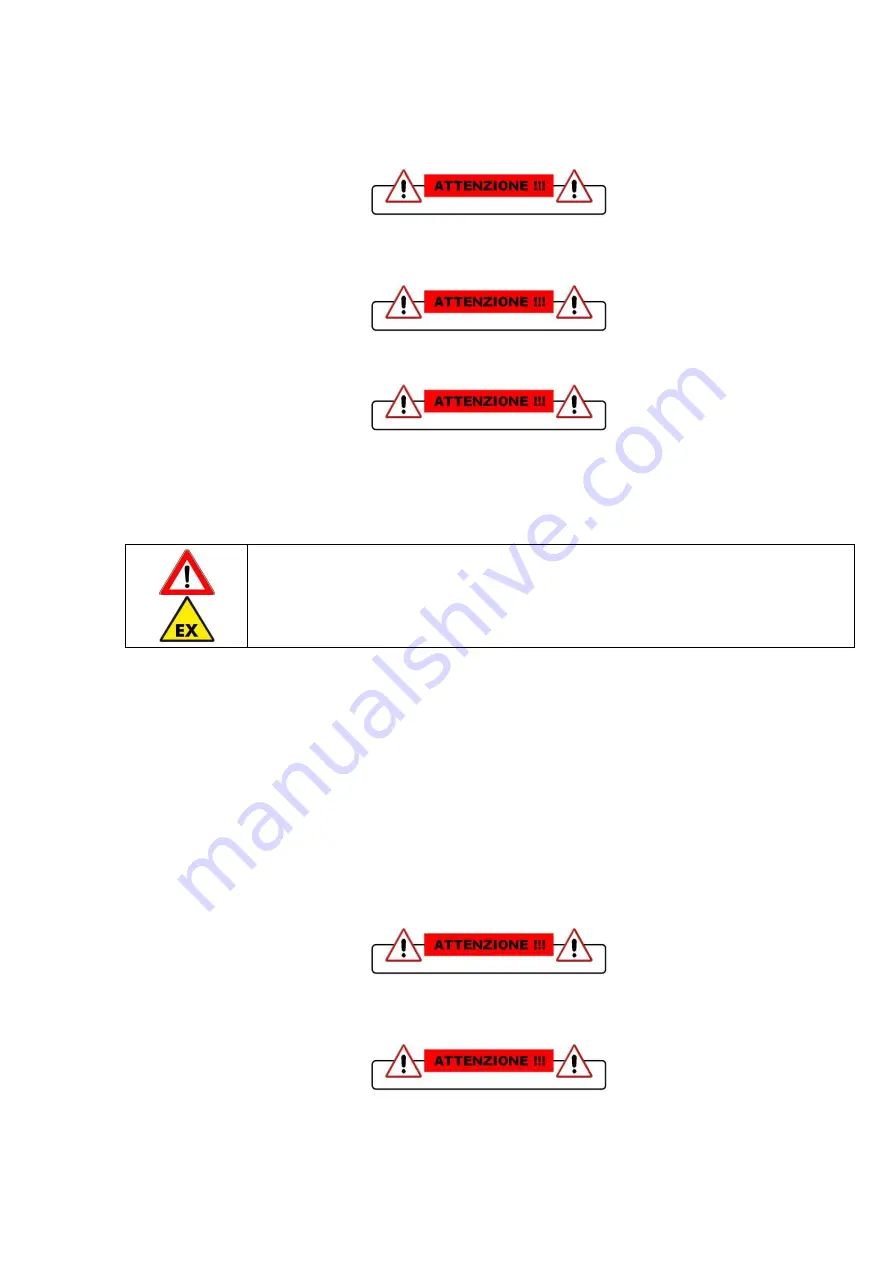
BG80 USE AND MAINTENANCE BOOKLET
Rev.1 of 23/04/2013 of BG80 uk agg2013 Page 26 of 40
To ensure that the mixer functions correctly, it should ideally be mounted at least 1 metre from the edge of
the ceiling, so that the propeller can also function in the presence of fermented substrates with high levels of
dry substance.
When planning and drilling the hole in the ceiling, a sufficient degree of distance must be maintained from the
outside edge of the tank, to enable the manoeuvres necessary to install and dismantle the mixer; a sufficient
degree of distance should also be maintained from any other tanks and equipment.
When planning and drilling the hole in the wall, remember that it is necessary to remove any insulation
material that may be present.
In order to obtain a resistant seal between the frame and the cement surface, the surfaces around the
structure must be smooth and consistent; there should be no rough edges around the hole in the
tank, any rough edges should be smoothed down.
Remove any insulation material from the outside of the tank. There should be no rough edges around the
hole in the tank, any rough edges should be smoothed down.
Risk of explosion in the event of a biogas leak!
In order to ensure correct sealing of the mixer frame, the cover of the tank must be
sufficiently level. There should be no cavities or irregularities!
8
8
.
.
1
1
.
.
2
2
.
.
GENERAL INSTRUCTIONS TO PREPARE THE SITE FOR WALL-MOUNTING
To mount the mixer, a 1,300 mm x 1,300 mm hole must be made in the wall.
The equipment should be installed so that the distance between the upper edge of the opening in the wall
and the upper edge of the wall of the tank is 0.5 m.
It should generally be positioned 4 - 5 m from the point through which the raw materials are introduced, so
that the propeller range can uniformly homogenise the solid substances that have been introduced.
The position of the mixer must be chosen in light of the position of any other pre-existing mixers.
The thrust of the mixer does not usually need to be altered.
The standard frame supplied by the manufacturer is inclined 30° to the left. In this way the flow of the mixed
product rotates in a clockwise direction; normally the swirl created by the mixing blade facilitates the rotary
motion of the mixed product.
When planning and drilling the hole in the ceiling, a sufficient degree of distance must be maintained from the
outside edge of the tank, to enable the manoeuvres necessary to install and dismantle the mixer; a sufficient
degree of distance should also be maintained from any other tanks and equipment.
In order to obtain a resistant seal between the frame and the cement surface, the surfaces around the
structure must be smooth and consistent; there should be no rough edges around the hole in the
tank, any rough edges should be smoothed down.