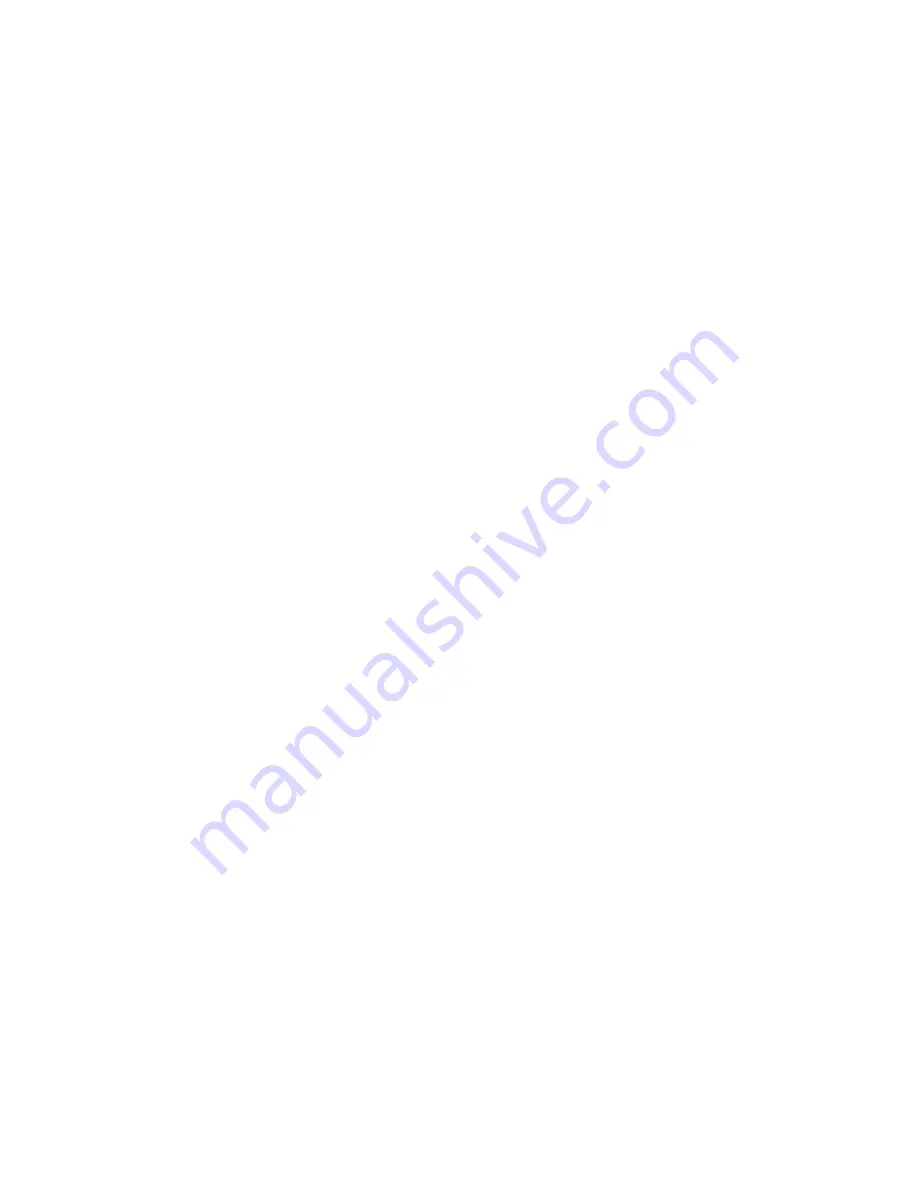
DINO 210XT
89
PLATFORM CONTROL CENTRE (UCB), SWITCHES
DMK:
DEAD-MAN-SWITCH
JST:
JOYSTICK
As the right side of the rocker switch is depressed, the movements are: boom up - down and turn
right - left.
As the left side of the rocker switch is depressed, the movements are: telescope out - in and
articulated arms up - down.
S4:
LOCKING EMERGENCY STOP SWITCH
Stops all other functions except the emergency descent and the sound signal, which remain
operational.
S5:
STOP SWITCH
Disconnects the control voltage from the control contactor of the electric motor and the stop relay of
the combustion engine.
S6:
START SWITCH
Controls the contactor of the electric motor and start solenoid of the combustion engine if the
combustion engine is used.
S10:
SOUND SIGNAL SWITCH
S11:
EMERGENCY DESCENT SWITCH
Controls the solenoid for the emergency descent unit which starts the unit and supplies the control
voltage to the control levers while the the emergency descent system is in operation.
S12:
PLATFORM LEVELLING FORWARD-BACKWARD
Control switch, non-locking lever switch.
The levelling is operated by pressing the button S29 and tuning the lever switch S12.
S29:
SELECTOR SWITCH FOR LEVELLING AND TURNING OF PLATFORM
Non-locking button switch.
Switches on the control voltage to the switches S12 and S36 as the button is pressed.
S31:
TELESCOPE IN
Non-locking pushbutton for retraction of the telescope.
S36:
PLATFORM TURN TO LEFT AND RIGHT
Non-locking lever switch.
Controls the relays K14 and K15.
The turning is operated by pressing the button S29 and turning the lever switch S36.
S41:
COMBUSTION ENGINE CHOKE
Non-locking button switch. Depressing the button activates the combustion engine choke.
Summary of Contents for 210XT
Page 2: ...DINO 210XT 2...
Page 3: ...DINO 210XT 3 OPERATING INSTRUCTIONS Valid from serial number 2945...
Page 6: ...DINO 210XT 6 REACH DIAGRAM...
Page 12: ...DINO 210XT 12...
Page 14: ...DINO 210XT 14...
Page 20: ...DINO 210XT 20 Notes...
Page 22: ...DINO 210XT 22...
Page 24: ...DINO 210XT 24...
Page 44: ...DINO 210XT 44 LUBRICATION PLAN...
Page 46: ...DINO 210XT 46 1...
Page 98: ...DINO 210XT 98 WIRING DIAGRAM...
Page 99: ...DINO 210XT 99 ELECTRIC DIAGRAM 2945...
Page 100: ...DINO 210XT 100...
Page 101: ...DINO 210XT 101...
Page 102: ...DINO 210XT 102...
Page 103: ...DINO 210XT 103...
Page 104: ...DINO 210XT 104...
Page 105: ...DINO 210XT 105...
Page 106: ...DINO 210XT 106...
Page 107: ...DINO 210XT 107...
Page 108: ...DINO 210XT 108...
Page 109: ...DINO 210XT 109...
Page 110: ...DINO 210XT 110...
Page 111: ...DINO 210XT 111...
Page 112: ...DINO 210XT 112...
Page 113: ...DINO 210XT 113...
Page 114: ...DINO 210XT 114...
Page 115: ...DINO 210XT 115...
Page 116: ...DINO 210XT 116 Notes...
Page 118: ...DINO 210XT 118 HYDRAULIC DIAGRAM 2945...
Page 119: ...DINO 210XT 119 Notes...