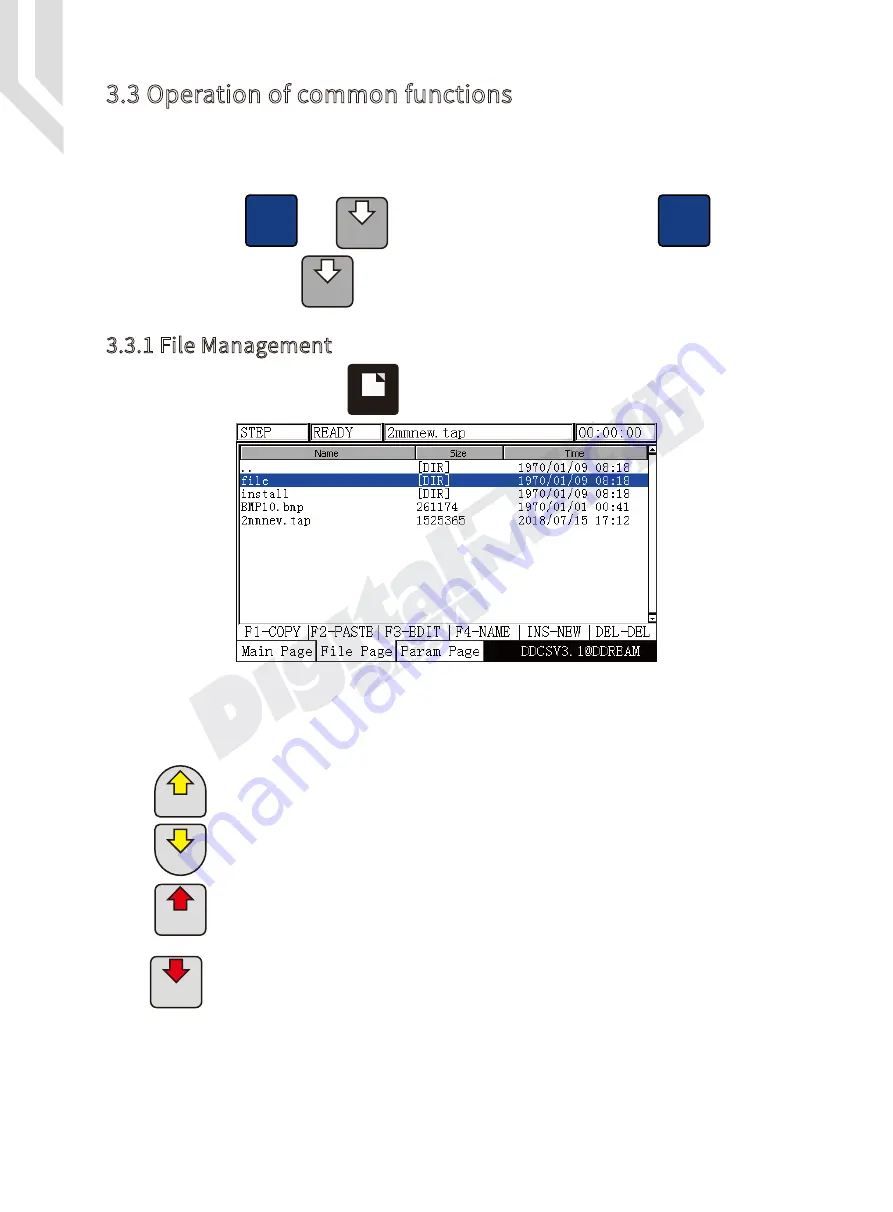
Page -28
Digital Dream Standalone Motion Controller DDCS V3.1
DDCS V3.1 Users Manual
Shift
The displays will show all folders and files in the root directory. The Name of folders and
files, the size of files and the time and date of manipulation. The blue strip indicates the current
valid target location.
3.3 Operation of common functions
3.3.1 File Management
Figure 3-6 File management page
For example: + indicates that you should first press and then
release this key,then press
When in the Main Page press to enter the File Page, See Figure 3-6 :
Press If the blue bar is at “ . .” , the Enter button will change to the last directory. If the
blue bar highlights a folder, it will open the folder. If the blue bar highlights a G code file, this
button will load the G code and go back to the Main Page for processing. If the blue bar high-
lights a .set file, it will upgrade the system. In this case make sure you delete the settings file
or the upgrade will overwrite the original settings file too and you will lose your settings.
Press to move up
Press to move down
Press to quit the file management page
TIP
Do not press two keys at the same time
HOME
Z
-
ENTER
Z
+
Z
CANCEL
PAGE R
Shift
Y-
ZERO
Y
+
Y
A
-
PROBE
MODIFY
A
-
PROBE
MODIFY