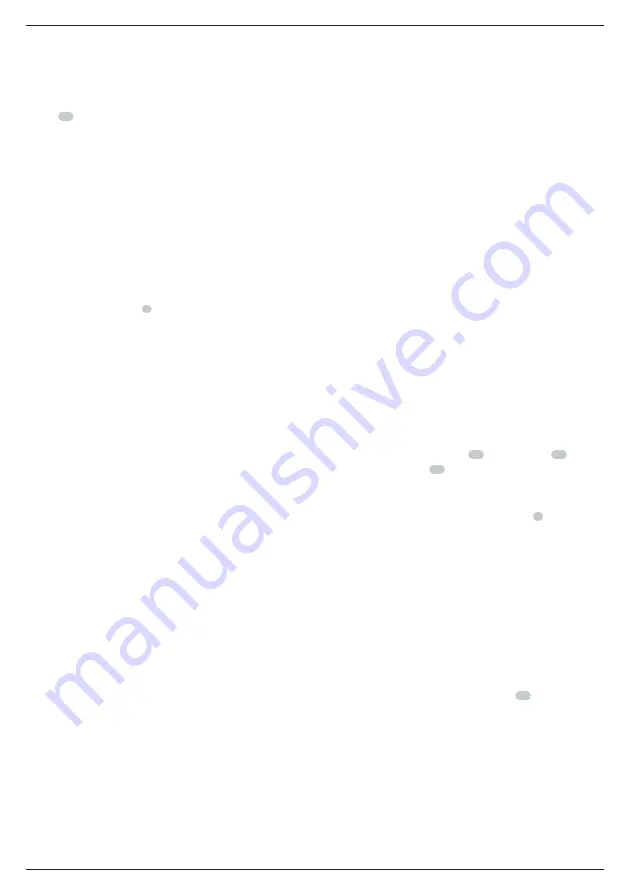
54
EnGLIsh
nOTE:
Edge grinding and cutting can be performed with Type
27 wheels designed and specified for this purpose;
6 mm
thick
wheels are designed for surface grinding while thinner Type
27 wheels need to be examined for the manufacturer's label to
see if they can be used for surface grinding or only edge grinding/
cutting. A Type A (cut‑off)
wheel guard
must be used for any
wheel where surface grinding is forbidden. A Type A (cut‑off)
(previously called type 1/41)
wheel guard
must be used for for
any dual purpose (combined grinding and cutting‑off abrasive)
wheels. Cutting can also be performed by using a Type 1/41
wheel and a Type A cut‑off
wheel guard
previously called Type
1/41 guard.
nOTE:
See the
Accessory and Guard Applications Chart
to
select the proper guard / accessory combination.
Mounting and Removing Guard (Fig. F)
CAUTION:
Guards must be used with all grinding wheels,
cut-off wheels, diamond coated wheels, sanding flap
discs, wire brushes, and wire wheels. The tool may be used
without a guard only when sanding with conventional
sanding discs. Some
D
e
WALT
models are provided with a
guard intended for use with depressed
centre
wheels (Type
27) and hubbed grinding wheels (Type 27). The same
guard is designed for use with sanding flap discs (Type
27 and 29) and wire brushes. A Type A guard must be used
for any cutting application. Grinding with wheels other
than Type 27 and 29 require different accessory guards.
Mounting instructions for these accessory guards are
included in the accessory package.
1. Open the guard
release lever
(
10
). Align the lugs (
16
) on the
guard with the slots (
17
) on the gear case.
2. Push the guard down until the guard lugs engage and
rotate freely in the groove on the gear case hub.
3. With the guard latch open, rotate the guard (
9
) into the
desired working position. The guard body should be
positioned between the spindle and the operator to provide
maximum operator protection.
4. Close the guard latch to secure the guard on the gear case.
You should not be able to rotate the guard by hand when
the latch is closed. Do not operate the grinder with a loose
guard or the clamp lever in open position.
5. To remove the guard, open the guard latch, rotate the guard
so that the arrows are aligned and pull up on the guard.
nOTE:
The guard is pre‑adjusted to the diameter of the gear
case hub at the factory. If, after a period of time, the guard
becomes loose, tighten the adjusting screw
18
with clamp
lever in the closed position.
CAUTION:
Do not tighten the adjusting screw with the
clamp lever in open position. Undetectable damage to the
guard or the mounting hub may result.
CAUTION:
If guard cannot be tightened by adjusting
clamp, do not use tool and take the tool and guard to a
service
centre
to repair or replace the guard.
Guards
CAUTION: Guards must be used with all grinding
wheels, cutting wheels, sanding flap discs, wire
brushes, and wire wheels.
The tool may be used without
a guard only when sanding with conventional sanding
discs. Refer to Figure A to see guards provided with the unit.
Some applications may require purchasing the correct
guard from your local dealer or
authorised
service
centre
.
CAUTION:
When using a Type A (cut-off)
wheel guard
for facial grinding, the
wheel guard
may interfere with
the workpiece causing poor control.
CAUTION:
When using a Type B (grinding)
wheel guard
for cutting-off operations with bonded abrasive wheels,
there is an increased risk of exposure to emitted sparks and
particles, as well as exposure to wheel fragments in the
event of wheel burst.
CAUTION:
When using a Type A (cut-off), Type B (grinding)
wheel guard
for cutting-off and facial operations in
concrete or masonry, there is an increased risk of exposure
to dust and loss of control resulting in kickback.
Rotating the Gear Case (Fig. E)
To improve user comfort, the gear case will rotate 90 ° for
cutting operations.
1. Remove the four corner screws attaching the gear case to
motor housing.
2. Without separating the gear case from motor housing,
rotate the gear case head to desired position.
nOTE:
If the gear case and motor housing become
separated by more than 3 mm, the tool must be serviced
and re‑assembled by a
D
e
WALT
service center. Failure to
have the tool serviced may motor and bearing failure.
3. Reinstall screws to attach the gear case to the motor
housing. Tighten screws to 12.5 in.‑lbs. torque.
Overtightening could cause screws to strip.
Attaching the Auxiliary Handle (Fig. D)
WARNING:
This handle SHOULD BE USED AT ALL
TIMES to maintain complete control of the tool.
Always make sure the handle is tight.
Screw the auxiliary handle
5
tightly into one of the threaded
mounting holes of the gear case.
Fuel Gauge Battery Packs (Fig. C)
Some
D
e
WALT
battery packs include a fuel gauge which
consists of three green LED lights that indicate the level of
charge remaining in the battery pack.
To actuate the fuel gauge, press and hold the fuel gauge
button
29
. A combination of the three green LED lights will
illuminate designating the level of charge left. When the level
of charge in the battery is below the usable limit, the fuel gauge
will not illuminate and the battery will need to be recharged.
nOTE:
The fuel gauge is only an indication of the charge left on
the battery pack. It does not indicate tool functionality and is
subject to variation based on product components, temperature
and end‑user application.